Challenges in Traditional Manufacturing Processes
Streamlining production workflows in traditional manufacturing processes poses a significant challenge for many industries. The reliance on manual labor often leads to inefficiencies, errors, and inconsistencies in the production line. This can result in delays, increased production costs, and compromised product quality. Moreover, the lack of automation in traditional manufacturing hampers the ability to meet the demands of a rapidly changing market, leading to potential loss of competitive edge.
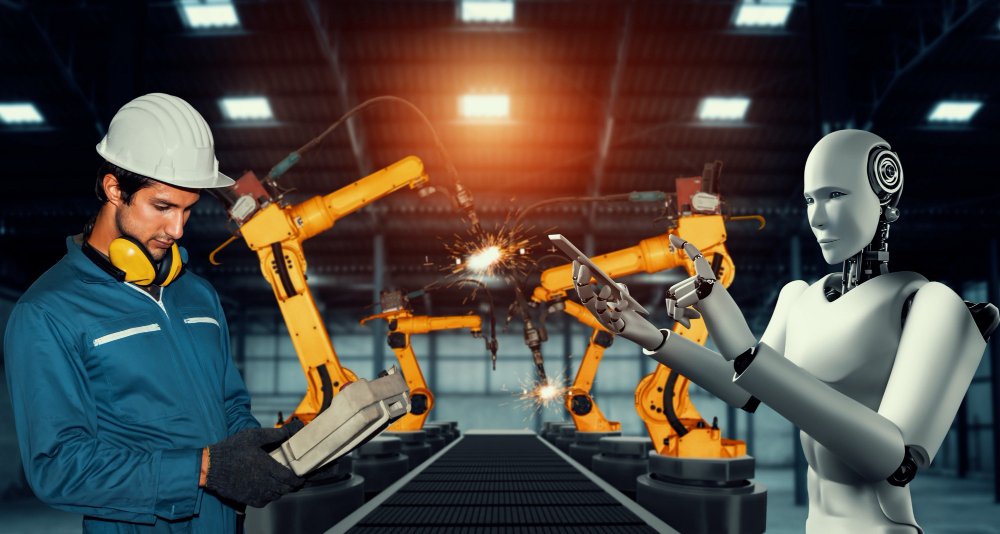
Another key challenge in traditional manufacturing is the limited flexibility to adapt to dynamic market conditions and changing consumer preferences. The rigid nature of traditional production methods makes it difficult for manufacturers to quickly adjust production schedules, respond to fluctuations in demand, or introduce new products in a timely manner. This lack of agility can hinder the overall competitiveness of businesses and restrict their ability to capitalize on emerging opportunities in the market.
Benefits of Implementing Robotics in Manufacturing
Robotics integration in manufacturing processes offers a myriad of advantages, with one of the key benefits being the significant increase in production efficiency. By automating repetitive and labor-intensive tasks, robots can work consistently and tirelessly without the limitations that human workers may face. This not only speeds up the manufacturing process but also reduces the margin of error, leading to higher quality outputs and decreased production time.
Moreover, implementing robotics in manufacturing can result in cost savings for companies. While the initial investment in robotics technology may seem substantial, the long-term savings in terms of reduced labor costs, increased productivity, and minimized waste can outweigh the upfront expenses. Additionally, with the precision and accuracy that robots bring to the production line, there is a decrease in the likelihood of defects or errors, ultimately saving resources and time that would otherwise be spent on rectifying mistakes.
Integration of Robotics in Smart Factories
The integration of robotics in smart factories has revolutionized the manufacturing industry. These advanced machines are designed to perform a wide range of tasks with precision and efficiency, leading to improved production processes and overall operational effectiveness. By seamlessly incorporating robotics into smart factories, companies are able to streamline their operations, optimize workflow, and meet the demands of a rapidly evolving market.
Smart factories equipped with robotics are able to automate repetitive tasks, increasing productivity and freeing up human workers to focus on more complex and creative endeavors. This automation not only enhances efficiency but also ensures consistent quality control throughout the manufacturing process. With real-time data analysis and predictive maintenance capabilities, robotics in smart factories pave the way for proactive decision-making and cost-effective measures that drive the industry towards greater success and sustainability.
Automation of Repetitive Tasks through Robotics
Automation of repetitive tasks through robotics has revolutionized the manufacturing industry by streamlining production processes and minimizing human error. Robots are programmed to perform monotonous tasks with precision and consistency, resulting in increased efficiency and productivity in manufacturing facilities. By taking over tasks such as assembly, welding, and packaging, robots free up human workers to focus on more complex and value-added responsibilities.
Furthermore, the use of robotics in automating repetitive tasks leads to improved product quality and consistency. Robots have the capability to operate 24/7 without fatigue or distraction, ensuring that every product is manufactured to the same high standards. This level of precision and reliability not only enhances the overall quality control process but also boosts customer satisfaction by delivering products that meet or exceed expectations.
Enhancing Efficiency and Productivity with Robotics
Incorporating robotics into manufacturing processes has revolutionized the efficiency and productivity of production lines. With the ability to work tirelessly and consistently at high speeds, robots can significantly reduce cycle times and increase output levels. This improved efficiency allows companies to meet customer demands more effectively and stay competitive in the market.
Moreover, robots are capable of performing intricate tasks with precision and accuracy, eliminating human errors and ensuring a higher quality of products. By streamlining operations and enhancing the overall workflow, robotics not only boost productivity but also enhance the reputation of manufacturers for delivering top-notch goods. The seamless integration of robotics in manufacturing facilities paves the way for a more efficient and productive future in the industry.
Improving Quality Control with Robotics
Robotic systems have revolutionized quality control processes in manufacturing by offering unparalleled precision and consistency. These automated systems can perform intricate inspections and measurements with accuracy beyond the capabilities of human workers. By utilizing advanced sensors and technologies, robots can detect even the slightest imperfections or deviations from specifications, ensuring that only products meeting the highest standards are allowed to proceed down the production line.
Furthermore, the integration of artificial intelligence and machine learning algorithms in robotic quality control systems has enabled real-time analysis of vast amounts of data. This capability allows for predictive maintenance and proactive adjustments to manufacturing processes, leading to continuous improvement in product quality. By identifying potential issues before they escalate, manufacturers can minimize defects and maintain a higher level of quality throughout the production cycle.
Cost Savings through Robotics Implementation
Implementing robotics in manufacturing processes can significantly impact cost savings for companies. By automating repetitive tasks, robots can work around the clock without the need for breaks, leading to increased production output without incurring additional labor costs. This enhanced efficiency not only reduces operational expenses but also minimizes the margin of error, ultimately improving the overall quality of products.
Moreover, robotics can help streamline supply chain management by optimizing inventory control and production scheduling. By accurately forecasting demand and adjusting production levels accordingly, companies can prevent overstocking or understocking of materials, thus reducing storage costs and minimizing wastage. These cost-saving benefits make robotics a valuable investment for companies looking to enhance their competitiveness in the ever-evolving manufacturing landscape.
Data Analytics and Robotics in Manufacturing
Data analytics and robotics play a crucial role in modern manufacturing processes by providing valuable insights and improving operational efficiency. Robotics collect vast amounts of data during production, and data analytics tools help in analyzing this information to identify patterns, trends, and potential areas for optimization. By combining the power of robotics and data analytics, manufacturers can make more informed decisions, enhance predictive maintenance strategies, and streamline their operations for increased productivity.
Moreover, the integration of data analytics with robotics enables real-time monitoring of manufacturing processes, allowing for quick adjustments and better control over quality standards. This proactive approach helps in minimizing defects, reducing downtime, and ultimately improving overall product quality. With the continuous advancements in technology, the synergy between data analytics and robotics is expected to revolutionize the manufacturing industry, paving the way for smarter, more efficient production methods and higher customer satisfaction levels.
Ensuring Safety in Smart Manufacturing Environments
Safety is a paramount concern in smart manufacturing environments where humans and robots work collaboratively. To ensure a safe workplace, risk assessments are conducted to identify potential hazards and implement appropriate safety measures. This includes installing safety barriers, emergency stop devices, and sensors that can detect human presence to prevent accidents during operation.
Furthermore, regular training and communication on safety protocols are essential for both human workers and robots. Employees need to be educated on how to interact with robots safely and understand the importance of following safety guidelines at all times. Additionally, robots are programmed with built-in safety features such as power and force limitations to prevent injuries to human workers in the vicinity. By prioritizing safety in smart manufacturing environments, businesses can create a culture of safety consciousness and minimize the risk of incidents occurring.
Future Trends in Robotics for Smart Manufacturing
As smart manufacturing continues to evolve, future trends in robotics are poised to revolutionize the industry. One key aspect that is gaining traction is the incorporation of artificial intelligence (AI) and machine learning algorithms into robotics systems. This integration enables robots to make autonomous decisions, learn from experience, and adapt to changing environments, thereby enhancing their efficiency and versatility in manufacturing processes.
Another significant trend on the horizon is the rise of collaborative robots, also known as cobots. These robots are designed to work alongside human employees, assisting them with various tasks and promoting a safer and more productive working environment. With their advanced sensors and ability to interact safely with humans, cobots are becoming increasingly popular in smart manufacturing facilities, where they can handle intricate tasks that require human-like dexterity and precision.
Training and Upskilling for Robotics Integration
As the manufacturing industry continues to embrace robotics technology, the need for proper training and upskilling of employees becomes crucial. Integrating robots into the manufacturing process requires a workforce that is well-equipped with the knowledge and skills to operate and manage these advanced systems effectively. Without adequate training, employees may struggle to adapt to the new technologies, leading to inefficiencies and potential safety risks in the production environment.
Investing in training programs that focus on robotics integration not only benefits the employees by enhancing their technical abilities but also contributes to the overall success of the manufacturing operation. By providing hands-on training and educational resources, companies can ensure that their workforce is proficient in working alongside robots and utilizing them to maximize efficiency and productivity. Furthermore, continuous upskilling programs enable employees to stay abreast of the latest advancements in robotics technology, ensuring that the manufacturing process remains cutting-edge and competitive in the industry.
Collaborative Robots (Cobots) in Manufacturing
Collaborative robots, also known as cobots, are revolutionizing the manufacturing industry by working alongside human operators in a shared workspace. Unlike traditional industrial robots that require safety cages to keep humans at a distance, cobots are designed to collaborate with workers on the factory floor, enhancing efficiency and productivity. These cobots are equipped with advanced sensors and software that allow them to safely interact with humans, making them ideal for automating repetitive tasks while ensuring a high level of safety.
The versatility of cobots makes them suitable for a wide range of manufacturing processes, from assembly and pick-and-place operations to quality inspection and packaging. With their user-friendly interfaces and easy programming capabilities, cobots can be quickly deployed and reconfigured to handle different tasks, providing manufacturers with flexibility and agility in responding to changing production demands. By integrating cobots into their production lines, manufacturers can streamline operations, improve workflow efficiency, and ultimately enhance their competitiveness in the fast-paced global market.
Environmental Sustainability in Smart Manufacturing with Robotics
Manufacturing processes have a significant impact on the environment, with energy consumption, waste generation, and resource usage being major concerns. By integrating robotics into smart manufacturing systems, companies can reduce their environmental footprint. Robots are designed to operate efficiently, optimizing energy usage and minimizing waste production. Additionally, they can be programmed to perform tasks with precision, reducing material wastage and contributing to a more sustainable manufacturing process.
Moreover, the use of robotics in smart manufacturing can also lead to a decrease in harmful emissions. With automated processes that are fine-tuned for efficiency, there is less reliance on traditional manufacturing methods that contribute to air and water pollution. By embracing robotics technology, companies can take a step towards achieving environmental sustainability in their manufacturing operations, aligning with global efforts to minimize the impact of industrial activities on the planet.
Additional Resources:
[catlist categorypage=”yes”]
Table of Contents
Categories:
[categories orderby=name]
Latest posts:
[sbs_latest_posts]
FAQs:
How can robotics help improve environmental sustainability in manufacturing?
Robotics can help reduce waste, energy consumption, and emissions in manufacturing processes, leading to a more environmentally sustainable operation.
What are some benefits of integrating robotics into smart manufacturing for environmental sustainability?
Some benefits include reducing carbon footprint, minimizing resource use, and optimizing production processes to be more eco-friendly.
How does automation of repetitive tasks through robotics contribute to environmental sustainability?
By automating repetitive tasks, robots can perform them more efficiently and accurately, reducing errors and waste in the manufacturing process.
Can robotics help enhance efficiency and productivity while also being environmentally friendly?
Yes, robotics can optimize production processes, improve cycle times, and increase output, all while minimizing environmental impact.
How does implementing robotics in manufacturing help improve quality control?
Robotics can perform precision tasks with consistency, leading to higher quality products and reducing the need for rework or scrap, which can be harmful to the environment.
Are there cost savings associated with implementing robotics in smart manufacturing?
Yes, cost savings can be achieved through increased efficiency, reduced waste, lower energy consumption, and improved resource utilization with the help of robotics.
How can data analytics be used in conjunction with robotics for environmental sustainability in manufacturing?
Data analytics can help optimize robotic processes, identify opportunities for improvement, and track environmental performance metrics to ensure sustainable operations.
What are some future trends in robotics for smart manufacturing that could further enhance environmental sustainability?
Future trends may include the use of artificial intelligence, predictive maintenance, advanced sensors, and collaborative robots to drive even greater efficiencies and sustainability in manufacturing.
How can companies ensure safety in smart manufacturing environments with the integration of robotics?
Companies can implement proper training, safety protocols, risk assessments, and monitoring systems to ensure the safe operation of robots in manufacturing environments.
Is training and upskilling important for successful integration of robotics in manufacturing?
Yes, providing training and upskilling opportunities for employees is crucial to maximize the benefits of robotics integration and ensure a smooth transition to a more sustainable manufacturing operation.