Smart Factory Integration Challenges
Smart factories hold the promise of increased efficiency, productivity, and flexibility in manufacturing processes. However, the integration of various systems and technologies within the smart factory environment poses significant challenges. One of the primary hurdles faced by manufacturers is the seamless connectivity between different devices, sensors, and machines. When these components cannot communicate effectively with each other, it can lead to disruptions in production and data flow, impacting overall operational performance.
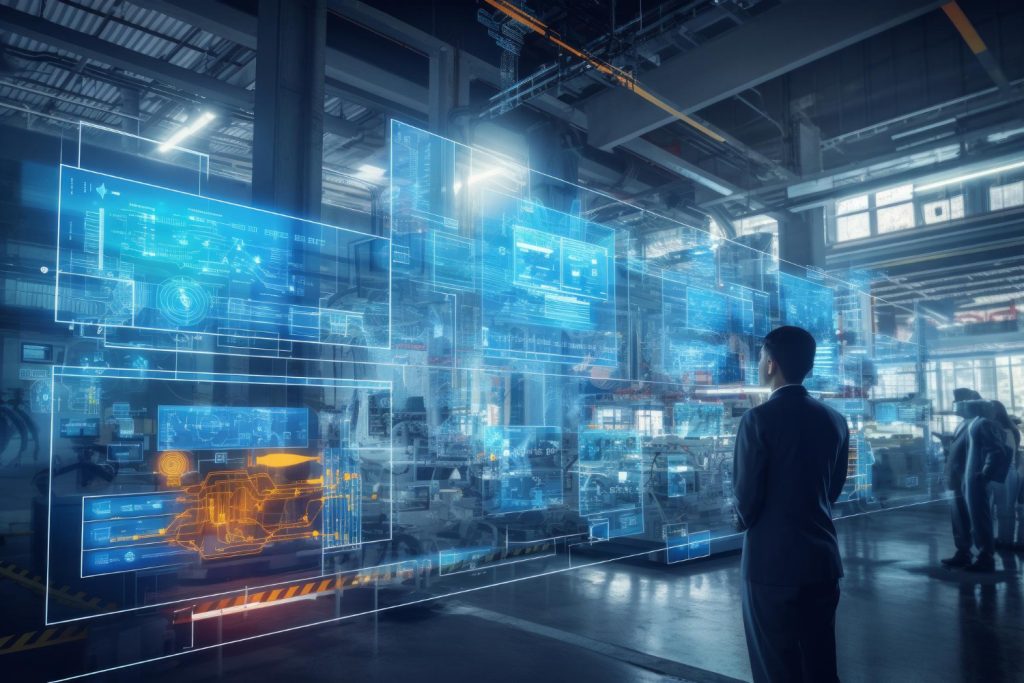
Another key challenge in smart factory integration is the compatibility issues that arise when trying to connect new, advanced technologies with existing legacy systems. Often, these older systems were not designed with interoperability in mind, making it difficult to integrate them into the modern smart factory ecosystem. This lack of compatibility can result in data silos, inefficiencies, and reduced visibility into the manufacturing process. By addressing these connectivity challenges head-on, manufacturers can unlock the full potential of their smart factory initiatives and drive greater business outcomes.
Understanding the Importance of Connectivity
In the realm of smart factories, connectivity serves as the backbone that intertwines different systems and technologies into a coherent network. It enables seamless communication between various devices, sensors, and machines, fostering real-time data exchange and analysis. Connectivity plays a crucial role in streamlining operations, optimizing efficiency, and enabling predictive maintenance in manufacturing processes.
The importance of connectivity lies in its ability to facilitate the automation of tasks, enhance decision-making processes, and improve overall productivity in smart factories. By establishing robust connections between different components within the factory ecosystem, organizations can unleash the full potential of Industry 4.0 technologies and drive innovation. Ultimately, understanding the pivotal role of connectivity is essential for harnessing the myriad benefits of smart factory integration and staying competitive in a rapidly evolving industrial landscape.
Identifying Common Connectivity Issues in Smart Factories
Smart factories, equipped with cutting-edge technology and automation systems, rely heavily on seamless connectivity to ensure smooth operations. However, numerous common connectivity issues can hinder the efficiency of these smart facilities. One prevalent challenge is network congestion, where the high volume of data transmission overwhelms the network bandwidth, leading to delays and disruptions in communication between devices and systems. This congestion can result in bottlenecks that impede the real-time exchange of crucial information, impacting overall productivity.
Another common issue faced in smart factories is interoperability concerns among various devices and software applications. The inability of different technologies to communicate effectively and share data can create siloed information systems, causing inefficiencies and limiting the scope of data analysis. This lack of interoperability often arises due to incompatible protocols, standards, or interfaces used by different equipment and software components within the factory environment. As a result, achieving a harmonized ecosystem where all devices can seamlessly interact and share data becomes a significant challenge for manufacturers striving for optimal efficiency in their operations.
• Network congestion can overwhelm bandwidth, causing delays and disruptions in communication
• Interoperability concerns among devices and software applications can create siloed information systems
• Incompatible protocols, standards, or interfaces hinder seamless interaction and data sharing
• Achieving a harmonized ecosystem for optimal efficiency becomes challenging
The Impact of Connectivity Hurdles on Operations
Connectivity hurdles in smart factories can significantly hinder operational efficiency and productivity. When communication breakdowns occur between different systems and devices, it can lead to delays in production, inaccurate data transmission, and a lack of real-time insights. This can disrupt the overall flow of operations, impacting the timely delivery of goods, increasing downtime, and ultimately affecting the bottom line.
Moreover, connectivity issues can also impede the ability to make informed decisions based on real-time data analysis. In a smart factory environment where data-driven insights are crucial for optimizing processes and enhancing overall performance, poor connectivity can result in outdated or incomplete information being used for decision-making. This can lead to suboptimal strategies, missed opportunities for improvement, and a failure to adapt quickly to changing market demands.
Strategies for Overcoming Connectivity Challenges
One effective strategy for overcoming connectivity challenges in smart factories is to conduct a comprehensive assessment of the existing infrastructure. By identifying weak points and bottlenecks, companies can proactively address connectivity issues before they become major obstacles. This assessment should include an evaluation of current communication protocols, network configurations, and hardware components to pinpoint areas that require improvement.
Furthermore, implementing redundancy measures can help mitigate connectivity disruptions in smart factories. By creating backup systems and alternative communication pathways, companies can ensure continuous operations even in the event of network failures. Redundancy measures can range from simple failover mechanisms to more complex dual-redundancy setups, depending on the specific needs and criticality of the processes involved.
Implementing Robust Communication Protocols
To ensure seamless communication within a smart factory environment, implementing robust communication protocols is crucial. These protocols serve as the foundation for transmitting data between different devices and systems, creating a reliable network infrastructure. By establishing standardized protocols, such as MQTT or OPC UA, smart factories can enhance interoperability and data exchange efficiency.
Moreover, robust communication protocols help in reducing latency issues and enhancing real-time data transmission. By prioritizing protocols that support low-latency communication, smart factories can improve the speed and accuracy of decision-making processes. Additionally, implementing secure protocols with built-in encryption mechanisms can safeguard sensitive data from potential cyber threats, ensuring the overall integrity and confidentiality of communication within the factory setting.
Leveraging IoT Technology for Seamless Integration
Implementing IoT technology can significantly enhance the connectivity within smart factories. By utilizing IoT devices such as sensors and actuators, various machines and equipment can communicate seamlessly with each other, enabling real-time data sharing and analysis. This interconnected network of IoT devices forms the backbone of a smart factory, facilitating efficient production processes and predictive maintenance capabilities.
Moreover, leveraging IoT technology allows for the integration of advanced analytics and machine learning algorithms, which can optimize production workflows and detect potential issues before they escalate. With IoT sensors collecting data at every step of the manufacturing process, factory operators can gain valuable insights into operational efficiencies and make informed decisions to improve overall productivity. The seamless integration of IoT technology not only streamlines operations but also paves the way for future innovations in the smart factory environment.
The Role of Data Security in Smart Factory Connectivity
Data security plays a critical role in the seamless functioning of smart factories. As these interconnected systems rely on a vast amount of data exchange between machines and components, ensuring the confidentiality, integrity, and availability of this information is paramount. Cybersecurity measures need to be implemented to safeguard against potential breaches or unauthorized access that could compromise sensitive production data.
Moreover, protecting data in smart factories is not only vital for operational efficiency but also for maintaining customer trust and regulatory compliance. Any security vulnerabilities in the connectivity infrastructure could lead to disruptions in production schedules, data loss, or even financial losses. Therefore, adopting robust encryption protocols, access controls, and monitoring mechanisms are necessary components of a comprehensive data security strategy in smart factory environments.
Addressing Compatibility Issues with Legacy Systems
Modernizing a smart factory often involves integrating new technologies with existing legacy systems, presenting compatibility challenges. Legacy systems, built on outdated architectures and protocols, may struggle to communicate effectively with newer IoT devices and software. This disparity can hinder data flow and lead to operational inefficiencies within the factory environment.
To address compatibility issues with legacy systems, it is crucial to conduct a thorough assessment of the existing infrastructure. This evaluation helps highlight potential points of friction and informs the development of tailored integration strategies. By bridging the gap between legacy systems and newer technologies through custom solutions or middleware, smart factories can optimize connectivity and streamline operations for enhanced productivity.
Training Employees for Effective System Integration
Effective system integration in smart factories relies heavily on the knowledge and skills of the employees tasked with this critical responsibility. Proper training is essential to ensure that employees have a deep understanding of the complex systems and technologies involved in smart factory operations. By providing comprehensive training programs, organizations can empower their staff to successfully integrate various systems, troubleshoot issues, and optimize overall efficiency.
Training sessions should cover a range of topics, including the basics of system architecture, data communication protocols, and troubleshooting techniques. Hands-on exercises and simulations can also be beneficial in giving employees practical experience in system integration. Additionally, ongoing training and upskilling opportunities are crucial to keep employees abreast of the latest advancements in smart factory technologies and practices, enabling them to adapt to changing requirements and continuously improve system integration processes.
Utilizing Cloud Solutions for Improved Connectivity
Cloud solutions have become increasingly popular in the realm of smart factory integration due to their ability to provide scalable and flexible connectivity options. By utilizing cloud platforms, manufacturers can access vital data and applications from anywhere, enabling seamless communication between devices and systems. This remote accessibility enhances real-time decision-making processes and facilitates collaboration among different departments within the factory environment.
In addition to improving connectivity, cloud solutions offer enhanced data storage capabilities and robust security features to protect sensitive information. By leveraging cloud technology, smart factories can centralize data management, streamline operations, and ensure seamless communication between various interconnected devices and machines. This integration not only enhances efficiency and productivity but also lays a solid foundation for future technological advancements in the manufacturing industry.
Monitoring and Managing Connectivity Performance
One essential aspect of ensuring the smooth operation of a smart factory is monitoring and managing connectivity performance. By continuously tracking the performance metrics of the network, devices, and systems, manufacturers can proactively identify and address any potential issues before they escalate. This real-time monitoring allows for quick interventions and adjustments to maintain optimal connectivity levels throughout the production process.
Effective management of connectivity performance involves not only monitoring data transmission speeds and network reliability but also evaluating the overall system efficiency. By analyzing data flow patterns and identifying bottlenecks in the network, manufacturers can streamline operations and enhance productivity. Additionally, regular performance assessments enable companies to make informed decisions regarding upgrades or modifications to the existing infrastructure, ensuring that the smart factory remains agile and responsive to changing demands.
Future Trends in Smart Factory Integration Technologies
The future of smart factory integration technologies is poised for significant advancements in the coming years. One trend that is gaining momentum is the adoption of artificial intelligence (AI) and machine learning algorithms to optimize production processes. These technologies can enable factories to predict maintenance needs, analyze data in real-time, and enhance overall operational efficiency.
Another prominent trend on the horizon is the widespread implementation of digital twins in smart factories. Digital twins create virtual replicas of physical assets and processes, providing real-time insights and analysis to improve decision-making. By leveraging digital twins, manufacturers can simulate different scenarios, troubleshoot issues, and optimize performance without disrupting operations. This innovation is expected to revolutionize the way smart factories operate and drive further integration of cutting-edge technologies.
Additional Resources:
[catlist categorypage=”yes”]
Table of Contents
Categories:
[categories orderby=name]
Latest Posts:
[sbs_latest_posts]
FAQs:
What are some common challenges faced in integrating smart factory technologies?
Some common challenges include connectivity issues, compatibility with legacy systems, data security concerns, and the need for employee training.
Why is connectivity important in smart factory integration?
Connectivity is crucial for seamless communication between different devices and systems in a smart factory, enabling efficient operations and data sharing.
How can smart factories overcome connectivity hurdles?
Smart factories can overcome connectivity challenges by implementing robust communication protocols, leveraging IoT technology, utilizing cloud solutions, and monitoring connectivity performance.
What role does data security play in smart factory connectivity?
Data security is essential to protect sensitive information and prevent cyber threats in smart factory environments where large amounts of data are exchanged between devices.
How can employees be trained for effective system integration in smart factories?
Employees can be trained through workshops, seminars, and hands-on experience to understand and effectively utilize the various technologies and systems in a smart factory.
What are some future trends in smart factory integration technologies?
Future trends include the use of advanced communication protocols, increased adoption of IoT devices, improved data security measures, and the integration of AI and machine learning technologies.