Challenges in traditional manufacturing processes
Traditional manufacturing processes often face challenges stemming from outdated equipment and machinery. These outdated tools can result in inefficiencies in production, leading to increased downtime and maintenance costs. Additionally, manual processes in traditional manufacturing can be prone to human error, impacting the quality and consistency of output.
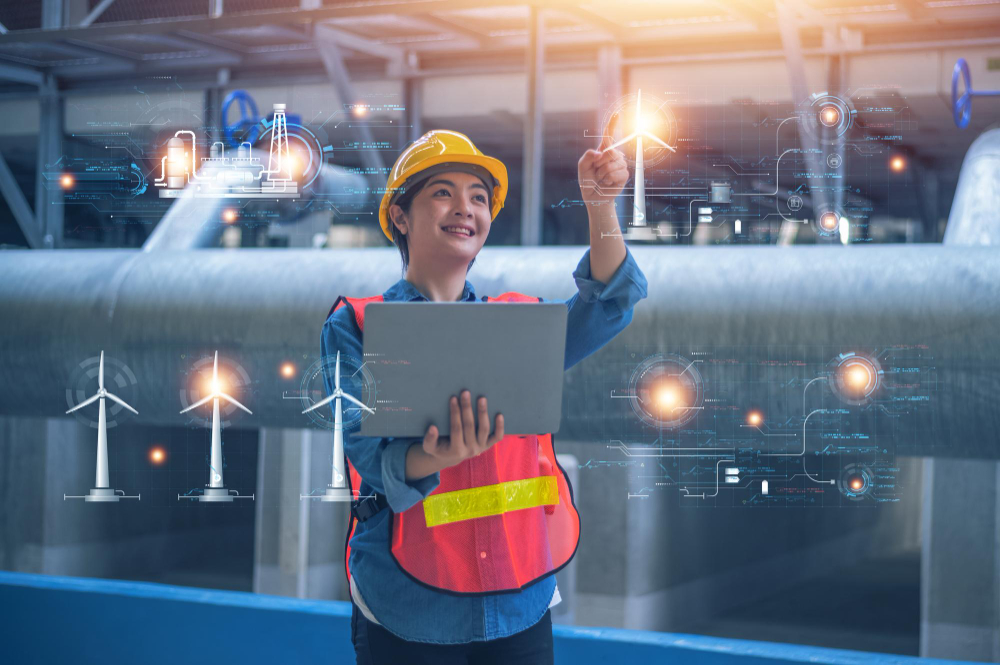
Another common challenge in traditional manufacturing is the lack of real-time monitoring and data analysis capabilities. Without access to up-to-date information on production metrics, such as equipment performance and energy consumption, manufacturers may struggle to identify areas for improvement and optimization. This can hinder decision-making processes and limit the ability to adapt to changing market demands swiftly.
Integration of Internet of Things (IoT) in smart factories
In the realm of manufacturing, the integration of Internet of Things (IoT) in smart factories has revolutionized operations and processes. IoT devices and sensors enable real-time data collection and communication, providing manufacturers with valuable insights for optimizing production efficiency and enhancing quality control. By connecting machines, equipment, and systems, IoT paves the way for predictive maintenance, efficient resource utilization, and seamless coordination across the factory floor.
Furthermore, the implementation of IoT in smart factories enhances connectivity and automation, fostering a more agile and responsive manufacturing environment. Through continuous monitoring and analysis of data generated by IoT devices, manufacturers can identify bottlenecks, streamline workflows, and make data-driven decisions to improve overall productivity. With the ability to remotely access and control equipment, track inventory levels, and monitor energy consumption, smart factories empowered by IoT technologies are at the forefront of the industry’s transformation towards smart manufacturing.
Benefits of energy-efficient practices in manufacturing
Energy-efficient practices in manufacturing offer a myriad of advantages for businesses aiming to enhance their bottom line. Reduced energy consumption not only leads to cost savings but also contributes to a cleaner environment by lowering carbon emissions. By adopting energy-efficient technologies and strategies, manufacturers can significantly decrease their energy bills and improve their overall operational efficiency.
Moreover, embracing energy-efficient practices can bolster a company’s reputation and attractiveness to environmentally-conscious consumers and investors. Demonstrating a commitment to sustainability through reduced energy usage can set manufacturers apart from competitors and showcase their dedication to corporate social responsibility. Additionally, energy-efficient practices can enhance overall process efficiency and productivity, leading to improved competitiveness and long-term viability in the market.
Role of artificial intelligence in optimizing energy usage
Artificial intelligence (AI) plays a crucial role in optimizing energy usage within manufacturing settings. Through AI algorithms and machine learning capabilities, factories can analyze large sets of data to identify patterns and trends in energy consumption. By leveraging this technology, manufacturers can make data-driven decisions to enhance operational efficiency, minimize energy wastage, and ultimately reduce costs associated with energy usage. AI enables real-time monitoring and control of energy systems, allowing for proactive adjustments to optimize energy usage based on production demands and external factors.
Furthermore, AI can assist in predictive maintenance of energy equipment, identifying potential issues before they escalate and lead to inefficiencies. By implementing AI-driven predictive maintenance strategies, manufacturers can prevent costly downtime and prolong the lifespan of energy systems. The ability of AI to continuously learn and adapt from data insights enables factories to constantly refine and improve energy usage practices, contributing to overall sustainability and competitiveness in the manufacturing sector.
Technological advancements in energy management systems
Energy management systems have witnessed remarkable technological advancements in recent years. These systems are now equipped with real-time monitoring capabilities, enabling manufacturers to track energy usage continuously. Additionally, the integration of predictive analytics tools has allowed for more accurate forecasting of energy needs, optimizing energy consumption in smart factories.
Moreover, the implementation of Internet of Things (IoT) devices has revolutionized energy management systems by providing interconnected sensors and devices that enable data collection and analysis in real time. This seamless connectivity allows for better control and automation of energy usage, leading to improved efficiency and cost savings for manufacturers.
Importance of data analytics in monitoring energy consumption
Data analytics plays a pivotal role in the manufacturing sector by providing valuable insights into energy consumption patterns. By analyzing real-time data from various sources, manufacturers can identify areas where energy is being underutilized or wasted. This allows for targeted interventions to optimize energy usage and reduce costs, ultimately leading to a more sustainable operation.
Moreover, data analytics enables manufacturers to predict future energy consumption trends based on historical data and external factors. This proactive approach helps in better planning and resource allocation, ensuring smooth operations and efficient energy management. In essence, the use of data analytics in monitoring energy consumption not only leads to cost savings but also contributes to environmental sustainability by reducing carbon emissions.
Case studies of successful implementation of energy efficiency in smart factories
In one notable case study, a renowned automotive manufacturer implemented energy-efficient practices in their smart factory, resulting in a significant reduction in overall energy consumption. By integrating IoT devices to monitor and control machinery operations, the company optimized energy usage during production cycles. This successful implementation not only decreased energy costs but also enhanced the factory’s operational efficiency and sustainability.
Another compelling example comes from a leading electronics manufacturer that leveraged artificial intelligence to optimize energy usage in their smart factory. By analyzing real-time energy data and machine performance metrics, the company identified opportunities to streamline energy consumption without compromising production output. As a result, the manufacturer achieved substantial energy savings while maintaining high levels of productivity, demonstrating the impact of AI-driven solutions in enhancing energy efficiency in modern manufacturing facilities.
Strategies for reducing carbon footprint in manufacturing
Manufacturers are increasingly adopting sustainable practices to reduce their carbon footprint and contribute to a greener environment. One effective strategy is implementing energy-efficient technologies and processes throughout the manufacturing chain. By optimizing energy usage and reducing waste, companies can significantly decrease their carbon emissions and operating costs simultaneously.
Another key approach to reducing the carbon footprint in manufacturing is the adoption of renewable energy sources. By harnessing solar, wind, or hydro power, factories can lessen their reliance on fossil fuels and transition towards cleaner forms of energy production. This not only helps in reducing greenhouse gas emissions but also enhances the overall sustainability of the manufacturing operations.
Impact of renewable energy sources on sustainability in factories
Renewable energy sources have emerged as a key factor in enhancing sustainability within manufacturing facilities. By harnessing energy from sources such as wind, solar, and hydropower, factories can significantly reduce their carbon footprint and environmental impact. Implementing renewable energy solutions not only supports global efforts towards combating climate change but also helps in achieving long-term cost savings and energy independence.
Utilizing renewable energy sources in factories not only contributes to a greener environment but also enhances the overall operational resilience of the facility. By diversifying energy resources and reducing dependency on traditional fossil fuels, manufacturers can mitigate risks associated with fluctuating energy prices and supply chain disruptions. Furthermore, adopting renewable energy technologies showcases a commitment to corporate social responsibility and underscores the role of factories as stewards of sustainable practices within their communities.
Training and education for employees on energy conservation practices
One crucial aspect of ensuring energy efficiency in manufacturing processes is the training and education of employees on energy conservation practices. Empowering employees with the necessary knowledge and skills can significantly contribute to reducing energy consumption within a factory setting. By instilling a culture of energy conservation among staff members, companies can cultivate a more sustainable approach to their operations.
Training programs can cover various topics such as understanding energy usage patterns, identifying energy-saving opportunities, and adopting best practices for energy conservation. Through hands-on training sessions and engaging educational materials, employees can become more conscious of their energy consumption habits and actively seek ways to minimize waste. Ultimately, investing in the training and education of employees on energy conservation practices not only benefits the environment but also contributes to cost savings and enhances the overall efficiency of manufacturing operations.
Regulatory guidelines for energy efficiency in manufacturing
Regulatory guidelines play a crucial role in shaping the energy efficiency landscape within manufacturing industries. These guidelines serve as a roadmap for businesses to adhere to specific standards and practices aimed at reducing energy waste and promoting sustainability. By enforcing regulations related to energy consumption, emissions control, and resource management, authorities can ensure that manufacturers are held accountable for their environmental impact.
Moreover, regulatory guidelines create a level playing field for all businesses operating within the manufacturing sector. By setting common standards and expectations, these guidelines help establish a sense of uniformity and consistency across the industry. This fosters healthy competition and motivates companies to continuously improve their energy efficiency practices to meet and exceed regulatory requirements. Compliance with these guidelines not only benefits the environment but also contributes to cost savings and operational efficiency for manufacturers.
Collaboration between manufacturers and technology providers for sustainable solutions
Manufacturers and technology providers are increasingly recognizing the importance of collaboration to drive sustainable solutions within the industry. By working together, these stakeholders can leverage each other’s expertise and resources to develop innovative technologies and practices that promote energy efficiency and environmental conservation in manufacturing processes. Such collaborative efforts not only benefit the companies involved but also contribute to the overall sustainability of the industrial sector.
Through partnerships between manufacturers and technology providers, industry-specific challenges can be addressed more effectively, leading to the development of tailored solutions that meet the unique requirements of each manufacturing environment. By sharing knowledge and resources, manufacturers can implement cutting-edge technologies and best practices that enhance energy efficiency, reduce waste generation, and minimize the environmental impact of their operations. Ultimately, collaboration between manufacturers and technology providers paves the way for the creation of more sustainable and environmentally-friendly manufacturing practices that align with global efforts to address climate change and promote sustainability.
• Collaboration between manufacturers and technology providers is essential for driving sustainable solutions within the industry
• By working together, stakeholders can leverage expertise and resources to develop innovative technologies and practices
• Partnerships lead to tailored solutions that address industry-specific challenges effectively
• Sharing knowledge and resources enhances energy efficiency, reduces waste generation, and minimizes environmental impact
• Collaborative efforts contribute to overall sustainability of the industrial sector
• Ultimately, collaboration paves the way for more environmentally-friendly manufacturing practices
Future trends in energy efficiency for smart factories
As smart factories continue to evolve, future trends in energy efficiency are poised to revolutionize manufacturing processes. Advanced technologies such as machine learning algorithms and real-time data analytics are set to play a key role in optimizing energy consumption. These tools can provide insights into energy usage patterns, enabling factories to adjust operations for maximum efficiency.
Additionally, the integration of renewable energy sources like solar and wind power is gaining momentum in smart factories. By harnessing clean energy sources, manufacturers can not only reduce their carbon footprint but also achieve cost savings in the long run. This shift towards sustainable practices aligns with the global push for environmental conservation and is expected to drive further innovation in energy efficiency for smart factories.
Additional Resources:
[catlist categorypage=”yes”]
Table of Contents
Categories:
[categories orderby=name]
Latest Posts:
[sbs_latest_posts]
FAQs:
What are some challenges faced in traditional manufacturing processes?
Some challenges in traditional manufacturing processes include outdated equipment, inefficient use of resources, and lack of real-time data for decision making.
How does the integration of Internet of Things (IoT) benefit smart factories?
IoT integration allows for real-time monitoring and control of equipment, predictive maintenance, and optimization of energy usage, leading to increased efficiency and cost savings.
What are the benefits of implementing energy-efficient practices in manufacturing?
Benefits of energy-efficient practices include reduced operating costs, lower carbon emissions, increased sustainability, and compliance with regulations.
How does artificial intelligence help in optimizing energy usage in smart factories?
Artificial intelligence algorithms can analyze data to identify patterns, predict energy consumption, and optimize operations for maximum energy efficiency.
What are some technological advancements in energy management systems for smart factories?
Technological advancements include smart sensors, cloud-based monitoring systems, energy analytics software, and automated controls for better energy management.
How important is data analytics in monitoring energy consumption in manufacturing?
Data analytics enables manufacturers to track energy usage, identify inefficiencies, and make informed decisions to optimize energy consumption and reduce costs.
Can you provide examples of successful implementation of energy efficiency in smart factories?
Case studies include companies using energy-efficient lighting, HVAC systems, and automated controls to reduce energy consumption and improve sustainability.
What strategies can be used to reduce carbon footprint in manufacturing?
Strategies include energy-efficient equipment, renewable energy sources, waste reduction, and recycling programs to minimize carbon emissions in the manufacturing process.
How do renewable energy sources impact sustainability in factories?
Renewable energy sources such as solar panels and wind turbines reduce reliance on fossil fuels, lower carbon emissions, and increase sustainability in manufacturing operations.
Is training and education important for employees on energy conservation practices?
Yes, training and education programs help employees understand the importance of energy conservation, how to use energy-efficient practices, and how to contribute to sustainability goals.
What are some regulatory guidelines for energy efficiency in manufacturing?
Regulatory guidelines include energy efficiency standards, emissions limits, and reporting requirements to ensure compliance with environmental regulations and promote sustainable practices.
How can manufacturers collaborate with technology providers for sustainable solutions?
Collaboration with technology providers enables manufacturers to access innovative solutions, expertise, and resources to implement energy-efficient practices and achieve sustainability goals.
What are some future trends in energy efficiency for smart factories?
Future trends include the use of artificial intelligence, IoT integration, renewable energy sources, and advanced energy management systems to further optimize energy usage and sustainability in manufacturing operations.