Key Components of Cyber-Physical Systems in Smart Factories
Cyber-physical systems (CPS) in smart factories consist of interconnected components that merge computational algorithms and physical processes. These systems rely on a network of sensors and actuators to collect and exchange data in real time. One key component is the integration of cloud computing infrastructure, enabling seamless communication and data storage for optimal operational efficiency.
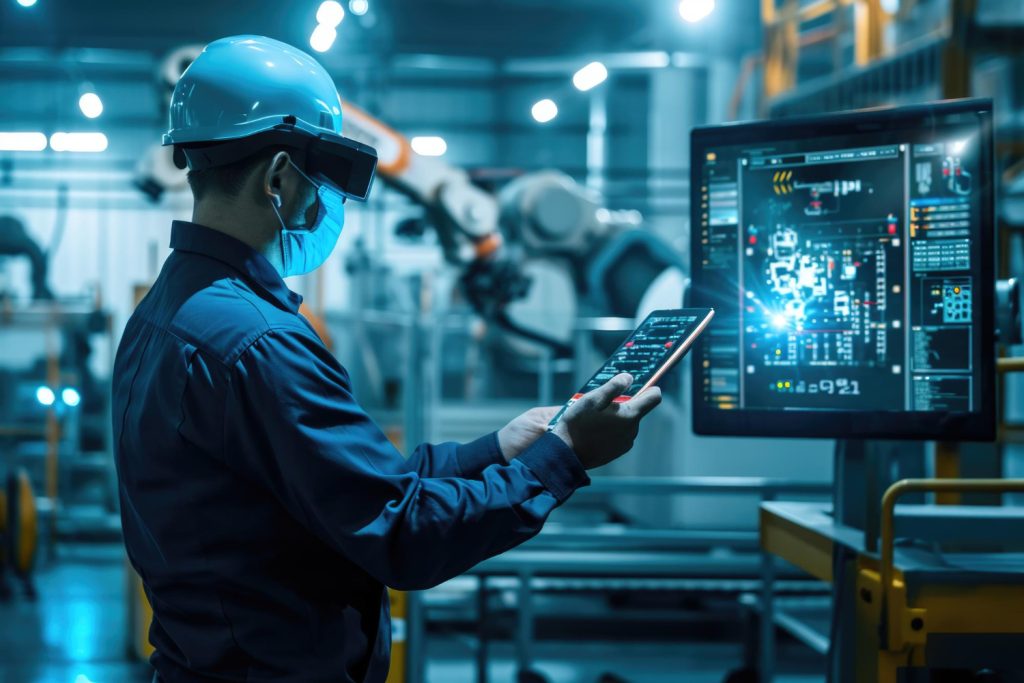
Another essential element of CPS in smart factories is the use of advanced robotics and automation technologies. These technologies enhance production processes by performing complex tasks with precision and speed. Collaborative robots, known as cobots, work alongside human operators to streamline workflows and boost productivity. Integration of machine learning algorithms further refines these systems, enabling predictive maintenance and intelligent decision-making for smoother operations.
The Role of Internet of Things (IoT) in Smart Factories
The Internet of Things (IoT) plays a crucial role in revolutionizing the operations of smart factories. By enabling the connection of physical devices and machinery to the internet, IoT technology allows for real-time monitoring and control of production processes. This interconnected system of devices provides valuable data to manufacturers, helping them optimize efficiency, reduce downtime, and improve overall productivity in the factory environment.
Furthermore, IoT in smart factories facilitates predictive maintenance by collecting and analyzing data on equipment performance. By utilizing sensors and data analytics, manufacturers can anticipate potential issues before they occur, allowing for proactive maintenance measures to be implemented. This predictive approach not only minimizes unexpected equipment failures but also extends the lifespan of machinery, ultimately leading to cost savings and increased reliability in manufacturing operations.
Advantages of Implementing Cyber-Physical Systems in Manufacturing
Implementing Cyber-Physical Systems (CPS) in manufacturing brings a multitude of advantages to the industry. One of the key benefits is the ability to improve efficiency and productivity significantly. By integrating physical machinery with digital technologies, tasks can be automated, processes can be streamlined, and data can be analyzed in real-time, leading to optimized operations and reduced downtime. This not only enhances overall output but also allows for faster decision-making based on accurate and up-to-date information, ultimately boosting profitability for manufacturers.
Moreover, the implementation of CPS in manufacturing facilitates predictive maintenance, which is a proactive approach to equipment upkeep. By utilizing sensors and data analytics, machines can signal when maintenance is required before a breakdown occurs. This predictive capability not only saves time and money by preventing unplanned downtime but also extends the lifespan of equipment and reduces the likelihood of costly repairs. Overall, predictive maintenance contributes to a more sustainable and reliable manufacturing process, ensuring continuous operation and enhancing the longevity of assets.
• Improved efficiency and productivity
• Automation of tasks and streamlined processes
• Real-time data analysis for optimized operations
• Faster decision-making based on accurate information
• Reduced downtime leading to increased profitability
Furthermore, the implementation of CPS in manufacturing also enables better resource utilization. Through real-time monitoring and control of machinery, manufacturers can identify inefficiencies in production processes and make necessary adjustments promptly. This proactive approach not only minimizes waste but also optimizes resource allocation, ultimately reducing operational costs and improving overall sustainability.
In addition to enhancing efficiency and resource utilization, Cyber-Physical Systems in manufacturing also contribute to improved safety measures. By integrating sensors and actuators into equipment, CPS can detect potential hazards or malfunctions before they escalate into dangerous situations. This early warning system enhances workplace safety by preventing accidents and ensuring a secure environment for workers. Ultimately, prioritizing safety through CPS implementation leads to a more reliable manufacturing process with minimized risks of injury or damage.
Overall, the advantages of implementing Cyber-Physical Systems in manufacturing are vast and impactful. From boosting efficiency and productivity to enabling predictive maintenance, optimizing resource utilization, improving safety measures, manufacturers stand to benefit greatly from embracing this innovative technology. By harnessing the power of CPS, companies can stay competitive in today’s fast-paced market while driving continuous improvement within their operations for long-term success.
Challenges of Integrating Cyber-Physical Systems in Smart Factories
One major challenge of integrating cyber-physical systems in smart factories is the complexity of aligning different technology platforms and systems. With a multitude of devices, sensors, and software applications involved in smart factory operations, ensuring seamless connectivity and communication between these components can be a daunting task. Incompatibility issues can arise when trying to integrate legacy systems with new technologies, leading to disruptions in production processes and hindering the effectiveness of the cyber-physical infrastructure.
Another obstacle in the integration of cyber-physical systems in smart factories is the potential security risks associated with interconnected devices and networks. As smart factories rely heavily on data exchange and connectivity among various systems, the vulnerability to cyber threats increases significantly. Ensuring the cybersecurity of smart factory operations becomes a critical concern, as a breach in the system can lead to data theft, production downtime, or even physical damage to the manufacturing infrastructure. Finding robust solutions to safeguard sensitive information and protect against cyber attacks is paramount in the successful implementation of cyber-physical systems in smart factories.
Real-time Data Collection and Analysis in Smart Factories
Real-time data collection and analysis play a crucial role in optimizing operations within smart factories. By continuously monitoring and analyzing data from various sensors and devices throughout the manufacturing process, smart factories can make real-time adjustments to improve efficiency and productivity. This data-driven approach enables swift decision-making, leading to reduced downtime and waste, as well as enhanced overall performance.
Additionally, real-time data collection and analysis in smart factories allow for predictive maintenance strategies to be implemented effectively. By leveraging machine learning algorithms and artificial intelligence, manufacturers can identify potential equipment failures before they occur, thereby minimizing unplanned outages and costly repairs. This proactive maintenance approach not only extends the lifespan of machinery but also ensures smooth production schedules, ultimately contributing to increased profitability for smart factories.
Machine Learning and Artificial Intelligence in Smart Factory Operations
Machine learning and artificial intelligence play a crucial role in optimizing smart factory operations. These technologies enable machines to learn from data, identify patterns, and make decisions without human intervention. By incorporating machine learning algorithms, smart factories can enhance predictive maintenance, production scheduling, and quality control processes. Artificial intelligence systems can analyze vast amounts of data in real-time, leading to more efficient and proactive decision-making in manufacturing operations.
Moreover, machine learning and artificial intelligence empower smart factories to implement adaptive manufacturing strategies. These technologies enable machines to adjust production parameters based on real-time data and external factors, such as demand fluctuations or supply chain disruptions. By leveraging machine learning and artificial intelligence, smart factories can improve operational flexibility, reduce downtime, and enhance overall productivity levels.
Enhancing Productivity through Automation in Smart Factories
Automation plays a crucial role in enhancing productivity in smart factories. By implementing automated processes and technologies, manufacturers can streamline operations, reduce human error, and increase efficiency. Tasks that are repetitive or mundane can be automated, allowing employees to focus on more complex and strategic activities that add value to the production process.
Moreover, automation in smart factories enables continuous operation without the need for breaks or shift changes, leading to higher output levels and improved overall productivity. With the use of robotic systems, conveyor belts, and automated guided vehicles, manufacturers can optimize the flow of materials and products throughout the factory floor. This not only speeds up production but also minimizes bottlenecks and delays, ultimately boosting productivity and profitability for the company.
Ensuring Cybersecurity in Smart Factory Operations
Cybersecurity plays a critical role in safeguarding smart factory operations from potential cyber threats and attacks. As smart factories become more interconnected and reliant on digital technologies, ensuring the protection of sensitive data and operational processes is paramount. With the increasing adoption of Internet of Things (IoT) devices and connected technologies in manufacturing, the attack surface for cyber threats expands, making proactive security measures essential to prevent breaches.
Implementing robust cybersecurity measures involves a multi-layered approach that encompasses network security, encryption protocols, access control mechanisms, and regular security audits. It is crucial for smart factories to constantly monitor their systems for any unusual activities or suspicious behavior that could indicate a security breach. By staying vigilant and proactive in identifying and addressing potential vulnerabilities, smart factories can mitigate the risks associated with cyber threats and protect their operations from disruptions.
Interoperability and Compatibility of Systems in Smart Factories
Interoperability and compatibility of systems play a crucial role in the seamless functioning of smart factories. As smart factories rely on a network of interconnected devices and systems to operate efficiently, ensuring that these components can communicate with each other effectively is essential. Interoperability refers to the ability of different systems and devices to connect and work together without encountering compatibility issues.
In the context of smart factories, interoperability allows for the integration of various technologies such as IoT devices, robotics, and artificial intelligence systems to collaborate and share data in real-time. This ensures that production processes can be automated, monitored, and optimized without any disruptions. Additionally, compatibility between different systems guarantees that information can be exchanged accurately and consistently, enabling manufacturers to make informed decisions based on reliable data streams.
Future Trends in Cyber-Physical Systems for Smart Factories
As smart factories continue to evolve, future trends in cyber-physical systems are poised to revolutionize manufacturing operations even further. One key trend is the increased integration of artificial intelligence (AI) and machine learning algorithms into cyber-physical systems. This integration will enhance predictive maintenance capabilities, optimize production processes, and enable self-learning systems that continuously improve efficiency and quality control.
Another significant trend is the adoption of digital twins in smart factory settings. Digital twins are virtual replicas of physical systems that allow for real-time monitoring, analysis, and simulation of factory operations. By creating digital twins of production lines, equipment, and processes, manufacturers can identify potential inefficiencies, predict maintenance needs, and optimize resource utilization in a simulated environment before implementing changes on the factory floor. This trend is expected to drive further advancements in predictive analytics and decision-making capabilities within smart factories.
Case Studies of Successful Implementation of Cyber-Physical Systems in Manufacturing
In one notable case study, a leading automotive manufacturer successfully integrated cyber-physical systems into their production processes, resulting in a significant increase in efficiency and reduction in downtime. By implementing real-time data collection and analysis tools, the company was able to streamline operations, identify potential issues before they escalated, and make data-driven decisions to optimize their manufacturing processes.
Another example of successful implementation of cyber-physical systems can be seen in a large electronics assembly plant. Through the use of machine learning and artificial intelligence algorithms, the plant was able to enhance its quality control procedures by detecting defects in real-time and automatically adjusting production parameters to ensure consistent output quality. This not only boosted the overall productivity of the plant but also led to cost savings through reduced waste and rework.
The Impact of Industry 4.0 on Smart Factory Operations
Industry 4.0 has revolutionized smart factory operations by bridging the gap between physical and digital systems. This transformation has allowed for greater connectivity, communication, and automation within manufacturing processes, leading to increased efficiency and productivity. Smart factories equipped with Industry 4.0 technologies can now optimize production schedules, predict maintenance needs, and adapt to changing demands in real-time, enhancing overall operational performance.
Furthermore, Industry 4.0 has enabled smart factories to leverage advanced data analytics, machine learning, and artificial intelligence to drive informed decision-making and process optimization. By harnessing the power of data, manufacturers can gain valuable insights into their operations, identify trends, and improve overall quality control. This shift towards data-driven decision-making has not only streamlined production processes but has also paved the way for predictive maintenance, reducing downtime and enhancing resource utilization in smart factory environments.
Strategies for Implementing Cyber-Physical Systems in Smart Factories
To successfully implement cyber-physical systems in smart factories, a clear roadmap must be established. Firstly, conducting a thorough assessment of the existing infrastructure and identifying areas for improvement is crucial. This includes evaluating the compatibility of current systems with new technologies and ensuring that cybersecurity measures are robustly in place. Additionally, developing a well-defined strategy that aligns with the overall goals of the organization is essential. This strategy should outline key milestones, responsibilities, and timelines for implementation to ensure a smooth and efficient transition to cyber-physical systems.
Furthermore, investing in training and upskilling employees is imperative for the successful integration of cyber-physical systems in smart factories. Providing comprehensive training programs to equip staff with the necessary skills to operate and maintain new technologies is vital. Engaging employees throughout the implementation process and encouraging a culture of continuous learning and innovation can help foster a supportive environment for the adoption of cyber-physical systems. Additionally, establishing clear communication channels to address any concerns or feedback from employees can aid in overcoming resistance to change and driving successful implementation of these advanced systems.
Additional Resources:
[catlist categorypage=”yes”]
Table of Contents
Categories:
[categories orderby=name]
Latest Posts:
[sbs_latest_posts]
FAQs:
What are the key components of Cyber-Physical Systems in smart factories?
The key components of Cyber-Physical Systems in smart factories include sensors, actuators, connectivity, data analytics, and control systems.
How does the Internet of Things (IoT) play a role in smart factories?
IoT enables the networking of physical devices and objects, allowing for real-time data collection, monitoring, and control in smart factories.
What are the advantages of implementing Cyber-Physical Systems in manufacturing?
Implementing Cyber-Physical Systems in manufacturing can lead to increased efficiency, reduced downtime, improved quality control, and predictive maintenance.
What are some challenges of integrating Cyber-Physical Systems in smart factories?
Challenges of integrating Cyber-Physical Systems include high initial costs, potential cybersecurity risks, the need for skilled workforce, and compatibility issues with existing systems.
How does real-time data collection and analysis benefit smart factories?
Real-time data collection and analysis provide valuable insights for decision-making, process optimization, predictive maintenance, and overall efficiency in smart factories.
How are machine learning and artificial intelligence used in smart factory operations?
Machine learning and artificial intelligence algorithms are used to optimize production processes, predict equipment failures, automate tasks, and improve overall productivity in smart factories.
How can automation enhance productivity in smart factories?
Automation can streamline processes, reduce human error, increase production speed, and improve overall efficiency in smart factories.
Why is ensuring cybersecurity important in smart factory operations?
Ensuring cybersecurity is crucial to protect sensitive data, prevent unauthorized access, safeguard intellectual property, and maintain the integrity of smart factory operations.
What is the significance of interoperability and compatibility of systems in smart factories?
Interoperability and compatibility of systems enable seamless communication between different devices, machines, and software applications in smart factories, ensuring efficient operations.
What are some future trends in Cyber-Physical Systems for smart factories?
Future trends in Cyber-Physical Systems include the adoption of edge computing, digital twins, 5G technology, advanced robotics, and the continued integration of AI and machine learning.
Can you provide some case studies of successful implementation of Cyber-Physical Systems in manufacturing?
Case studies of successful implementation of Cyber-Physical Systems include companies like Siemens, Bosch, and General Electric, which have leveraged CPS to improve efficiency, quality, and innovation in their manufacturing processes.
What is the impact of Industry 4.0 on smart factory operations?
Industry 4.0, characterized by the integration of digital technologies into manufacturing, has revolutionized smart factory operations by enabling automation, data-driven decision-making, and enhanced connectivity throughout the production process.
What are some strategies for implementing Cyber-Physical Systems in smart factories?
Strategies for implementing Cyber-Physical Systems in smart factories include conducting thorough needs assessment, investing in training and education, ensuring data security measures, fostering collaboration between IT and OT teams, and continuously evaluating and optimizing system performance.