Benefits of Implementing Digital Twin Technology in Smart Factory Design
Digital twin technology offers a myriad of benefits when integrated into smart factory design. Firstly, it enables real-time monitoring and analysis of operations, providing valuable insights for optimizing efficiency and productivity. By creating a digital replica of the physical factory environment, manufacturers can simulate different scenarios and make data-driven decisions to enhance overall performance.
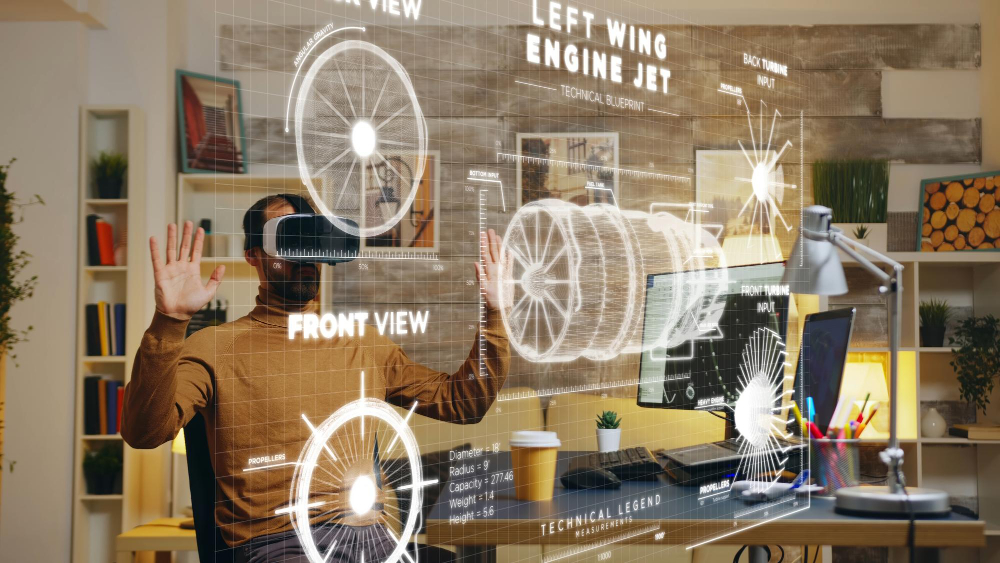
Moreover, digital twins facilitate predictive maintenance, helping to prevent costly downtime by identifying potential issues before they escalate. Through continuous monitoring of equipment and processes, smart factories can proactively address maintenance needs, ensuring smooth operations and reducing unplanned disruptions. This proactive approach not only improves operational efficiency but also extends the lifespan of machinery, ultimately leading to cost savings and higher levels of productivity.
Understanding the Concept of Digital Twin Technology in Manufacturing
Digital twin technology in manufacturing refers to the creation of a virtual representation that mirrors a physical product, process, or system. This virtual counterpart allows for real-time monitoring, analysis, and optimization, offering valuable insights for improving operational efficiency and performance. By integrating data from sensors, machinery, and various sources, digital twins provide a holistic view that enables manufacturers to make informed decisions and drive innovation.
The concept of digital twins extends beyond mere visualization to encompass predictive capabilities and simulations. Through advanced analytics and algorithms, digital twins can simulate scenarios, predict outcomes, and facilitate scenario planning in a risk-free environment. This predictive maintenance approach enables proactive interventions, reducing downtime, enhancing reliability, and ultimately leading to cost savings for manufacturers.
Applications of Digital Twin Technology in Smart Factory Simulation
Digital twin technology plays a crucial role in smart factory simulation by creating virtual replicas of physical assets and processes. These digital twins enable manufacturers to simulate and analyze different scenarios without disrupting actual operations. By harnessing real-time data and advanced analytics, smart factories can optimize production processes, identify potential bottlenecks, and enhance overall operational efficiency. Furthermore, simulation through digital twins allows for predictive maintenance strategies, reducing downtime and extending the lifespan of equipment.
In addition to process optimization, digital twin technology in smart factory simulation facilitates continuous improvement and innovation. Manufacturers can test new ideas, product variations, and manufacturing techniques in a risk-free virtual environment before implementing them on the factory floor. This not only accelerates the development cycle but also enhances product quality and customization capabilities. By simulating various conditions and parameters, smart factories can refine their production strategies, minimize waste, and meet the evolving demands of the market with agility and precision.
Challenges Faced in Adopting Digital Twin Technology for Smart Factory Design
One of the main challenges faced in adopting digital twin technology for smart factory design is the high initial investment required. Implementing digital twin technology involves significant costs related to hardware, software, and infrastructure setup. This financial commitment can deter some companies from fully embracing this technology, especially smaller manufacturers with limited budgets. Additionally, the complexity of integrating digital twin technology with existing manufacturing systems and processes can pose a significant hurdle. Ensuring seamless compatibility and data synchronization across different platforms and devices can be a time-consuming and resource-intensive task for manufacturers.
Another challenge in adopting digital twin technology for smart factory design is the lack of skilled workforce proficient in leveraging this advanced technology. Developing and maintaining digital twin models requires specialized knowledge in data analytics, simulation techniques, and IoT connectivity. Companies may struggle to find qualified personnel capable of implementing and managing digital twin technology effectively. Furthermore, the continuous evolution of digital twin capabilities and the need to stay updated with the latest trends and innovations add another layer of complexity to the talent acquisition and training process for manufacturers looking to adopt this technology.
Role of Internet of Things (IoT) in Enhancing Digital Twin Technology for Smart Factories
The Internet of Things (IoT) plays a crucial role in advancing the capabilities of digital twin technology within smart factories. By connecting physical objects and devices to the internet, IoT enables real-time data collection and communication, which is essential for creating accurate digital twin models. Through IoT sensors, smart factories can gather vast amounts of data from machines, equipment, and processes, allowing digital twins to mirror the physical environment with high fidelity. This real-time data integration enhances the predictive capabilities of digital twins, enabling manufacturers to monitor and optimize production processes effectively.
Furthermore, IoT integration in digital twin technology enables remote monitoring and control of smart factory operations. Manufacturers can leverage IoT-connected devices to remotely access and analyze real-time data generated by digital twins, facilitating quick decision-making and intervention when needed. By combining the power of IoT and digital twin technology, smart factories can achieve greater operational efficiency, predictive maintenance, and overall performance optimization.
Integration of Artificial Intelligence (AI) in Digital Twin Technology for Smart Factory Optimization
Artificial Intelligence (AI) plays a pivotal role in optimizing smart factories through the integration with digital twin technology. The combination of AI algorithms and digital twins enables real-time data analysis, predictive maintenance, and process optimization. With AI, digital twins can simulate various scenarios, identify patterns, and make data-driven decisions to enhance operational efficiency and productivity in smart factories.
Moreover, the implementation of AI in digital twin technology can facilitate autonomous decision-making processes within smart factories. By leveraging machine learning and cognitive computing, AI-powered digital twins can adapt to changing circumstances, forecast potential issues, and recommend optimal solutions. This advanced capability not only streamlines operations but also empowers organizations to proactively address challenges and improve overall performance in smart factory environments.
Advantages of Real-Time Data Monitoring and Analysis Using Digital Twin Technology
Real-time data monitoring and analysis utilizing digital twin technology offers unparalleled advantages in the realm of smart factories. One of the primary benefits is the ability to track and analyze various operational metrics instantly, providing real-time insights into the factory’s performance. This enables quick decision-making and adjustments to optimize processes, enhance productivity, and ensure efficient operations.
Moreover, the continuous monitoring and analysis of data through digital twins empower manufacturers to identify potential issues or anomalies promptly. By detecting deviations from the norm in real-time, proactive measures can be taken to prevent downtime, reduce maintenance costs, and improve overall equipment effectiveness. This predictive capability not only enhances operational efficiency but also supports the implementation of preventive maintenance strategies, ultimately leading to increased uptime and reduced disruptions in the manufacturing processes.
Improving Operational Efficiency Through Predictive Maintenance with Digital Twin Technology
Digital twin technology offers a valuable solution for enhancing operational efficiency through predictive maintenance in smart factories. By creating a digital replica of physical assets and systems, manufacturers can monitor equipment performance in real time and predict potential failures before they occur. This proactive approach to maintenance helps prevent costly downtimes and improves overall productivity in the manufacturing process.
Furthermore, the integration of digital twin technology with predictive maintenance algorithms enables smart factories to optimize their maintenance schedules based on actual equipment condition and usage data. By analyzing historical and real-time data, manufacturers can make informed decisions on when to perform maintenance tasks, leading to reduced maintenance costs and prolonged equipment lifespan. This predictive approach not only enhances operational efficiency but also contributes to a more sustainable and profitable manufacturing environment.
Enhancing Product Quality and Innovation with Digital Twin Technology in Smart Factories
Digital twin technology plays a crucial role in revolutionizing smart factories by enhancing product quality and driving innovation. By creating a digital replica of physical assets and processes, manufacturers can closely monitor and analyze operations in real-time, identifying potential issues before they escalate. This proactive approach allows for quick adjustments and optimizations, leading to improved product quality and reduced downtime.
Furthermore, digital twins enable manufacturers to simulate different scenarios and test new ideas without disrupting actual production processes. This flexibility fosters innovation as companies can experiment with design changes, process improvements, and new technologies in a virtual environment before implementing them on the factory floor. This rapid prototyping and testing help accelerate product development cycles, promote creativity, and ultimately, enhance competitiveness in the market.
The Future of Smart Factory Design and Simulation with Digital Twin Technology
As smart factory design continues to evolve, the integration of digital twin technology is set to play an increasingly vital role in shaping the future of manufacturing processes. By creating virtual replicas of physical assets, digital twins enable real-time monitoring, analysis, and optimization, leading to enhanced operational efficiency and productivity. This technology allows manufacturers to simulate various scenarios to predict outcomes, troubleshoot issues, and make informed decisions, ultimately driving innovation and improving overall performance.
Moreover, the utilization of digital twins in smart factory design offers the potential for predictive maintenance capabilities, reducing unplanned downtime and increasing equipment lifespan. With the ability to anticipate maintenance needs based on data analysis and machine learning algorithms, manufacturers can proactively address issues before they escalate, resulting in cost savings and improved asset reliability. The seamless integration of digital twin technology into smart factory simulation signals a transformative shift towards a more interconnected and data-driven approach to manufacturing, paving the way for a new era of efficiency and competitiveness in the industry.
Case Studies Highlighting Successful Implementation of Digital Twin Technology in Smart Factories
One notable case study showcasing the successful implementation of digital twin technology in a smart factory is seen at a leading automotive manufacturer. By creating a digital replica of their production line, the company was able to monitor equipment performance in real-time, predict maintenance needs, and optimize production processes efficiently. This resulted in a significant reduction in unplanned downtime and increased overall productivity.
In another instance, a global electronics manufacturer utilized digital twin technology to enhance product quality and innovation in their smart factory. By integrating IoT sensors with their digital twin model, the company gained valuable insights into the manufacturing process, allowing them to identify and address quality issues promptly. This proactive approach not only improved the quality of their products but also enabled faster design iterations and continuous innovation to meet evolving customer demands.
Key Considerations for Implementing Digital Twin Technology in Smart Factory Design
When considering the implementation of digital twin technology in smart factory design, it is crucial to prioritize data security and privacy. Ensuring that sensitive information is protected and that the digital twin system is safeguarded against cyber threats is essential for maintaining the integrity of the manufacturing process. Additionally, establishing clear data governance protocols and access controls can help prevent unauthorized use of the digital twin technology and preserve the confidentiality of proprietary information.
Moreover, it is important to engage all stakeholders in the implementation process to foster collaboration and ensure alignment with organizational objectives. Involving manufacturing experts, IT professionals, and other relevant personnel from the outset can help identify critical requirements, address potential challenges, and streamline the integration of digital twin technology into existing operations. By fostering a culture of collaboration and knowledge sharing, companies can leverage the expertise of diverse teams to unlock the full potential of digital twin technology in smart factory design.
Collaboration Opportunities for Manufacturers and Technology Providers in Advancing Digital Twin Technology for Smart Factories
Manufacturers and technology providers have a unique opportunity to collaborate in advancing the implementation of digital twin technology in smart factories. By combining their expertise, manufacturers can provide valuable insights into the specific requirements and challenges faced on the factory floor, while technology providers can offer innovative solutions and technical know-how to enhance the digital twin systems. This collaboration can lead to the development of more tailored and efficient digital twin solutions that cater to the unique needs of different manufacturing processes.
Moreover, manufacturers can benefit from the knowledge and experience of technology providers in leveraging advanced technologies such as artificial intelligence and Internet of Things to further optimize their smart factory operations. By working together, manufacturers can stay at the forefront of technological advancements and ensure that their digital twin systems are continuously updated and improved to meet the evolving demands of the industry. This collaboration fosters a symbiotic relationship where manufacturers can harness the power of cutting-edge technologies to drive operational excellence and innovation in their smart factories.
Additional Resources:
[catlist categorypage=”yes”]
Table of Contents
Categories:
[categories orderby=name]
Latest Posts:
[sbs_latest_posts]
FAQs:
What are the benefits of implementing Digital Twin Technology in smart factory design?
Implementing Digital Twin Technology allows for real-time monitoring and analysis, predictive maintenance, enhanced product quality and innovation, and improved operational efficiency in smart factories.
How can manufacturers understand the concept of Digital Twin Technology in manufacturing?
Manufacturers can understand Digital Twin Technology as a virtual representation of a physical object or system that allows for simulation, monitoring, and optimization of processes in manufacturing.
What are some applications of Digital Twin Technology in smart factory simulation?
Digital Twin Technology can be used for virtual testing of new processes, predictive maintenance planning, virtual commissioning of production lines, and optimizing production schedules in smart factories.
What challenges are faced in adopting Digital Twin Technology for smart factory design?
Challenges in adopting Digital Twin Technology include data integration issues, high initial investment costs, cybersecurity concerns, and the need for specialized skills and expertise.
How does the Internet of Things (IoT) enhance Digital Twin Technology for smart factories?
IoT devices provide real-time data collection, connectivity, and communication between physical objects and their digital twins, enabling more accurate monitoring and analysis in smart factories.
What is the role of Artificial Intelligence (AI) in Digital Twin Technology for smart factory optimization?
AI algorithms can analyze large amounts of data from digital twins to optimize processes, predict maintenance needs, improve decision-making, and enhance overall efficiency in smart factories.
What are the advantages of real-time data monitoring and analysis using Digital Twin Technology?
Real-time data monitoring and analysis allow for quick identification of issues, improved decision-making, proactive maintenance planning, and overall increased operational efficiency in smart factories.
How can predictive maintenance be improved through Digital Twin Technology in smart factories?
Digital Twin Technology enables predictive maintenance by analyzing real-time data from physical assets, predicting potential failures, and scheduling maintenance activities to prevent costly downtime in smart factories.
How can Digital Twin Technology enhance product quality and innovation in smart factories?
Digital Twin Technology allows for virtual testing of new product designs, continuous monitoring of production processes, and feedback loops for rapid improvements, leading to higher product quality and innovation in smart factories.
What does the future of smart factory design and simulation look like with Digital Twin Technology?
The future of smart factory design and simulation with Digital Twin Technology includes more advanced virtual representations, increased automation, improved collaboration between physical and digital systems, and enhanced overall efficiency in manufacturing.
Can you provide some case studies highlighting successful implementation of Digital Twin Technology in smart factories?
Yes, case studies showcasing successful implementations of Digital Twin Technology in smart factories can demonstrate real-world benefits such as cost savings, increased productivity, reduced downtime, and improved product quality.
What are some key considerations for manufacturers when implementing Digital Twin Technology in smart factory design?
Key considerations for manufacturers include defining clear objectives, ensuring data accuracy and security, investing in necessary infrastructure and technology, training employees on new systems, and continuously evaluating and improving processes.
How can manufacturers and technology providers collaborate to advance Digital Twin Technology for smart factories?
Manufacturers and technology providers can collaborate by sharing expertise, resources, and data to develop innovative solutions, conducting joint research and development projects, and establishing partnerships to drive the adoption and advancement of Digital Twin Technology in smart factories.