Challenges in Implementing Sustainable Practices
Implementing sustainable practices in manufacturing processes faces several challenges. One common obstacle is the initial investment required to transition to more environmentally friendly technologies and materials. Companies often need to allocate significant resources to upgrade existing systems, which can be a deterrent for some organizations, especially smaller ones with limited budgets.
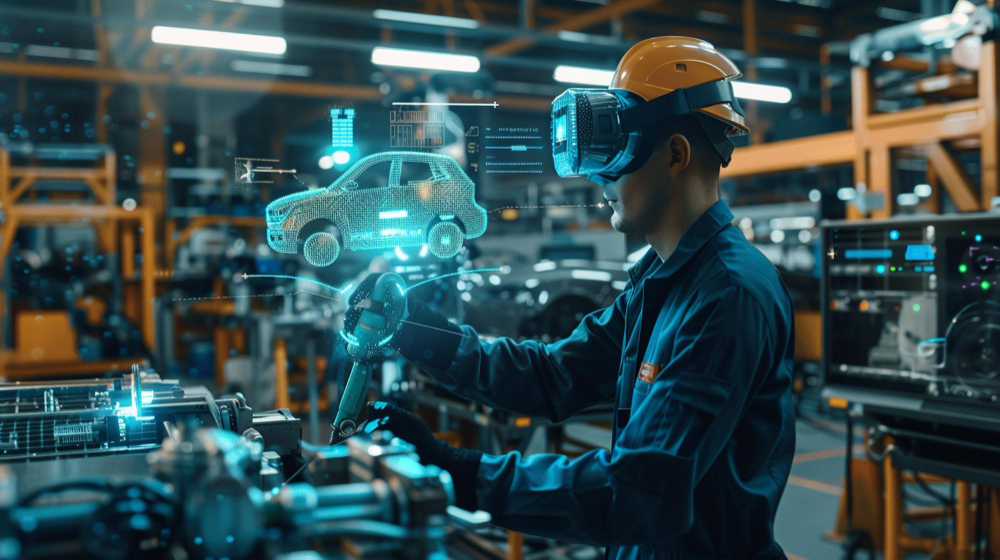
Moreover, changing established practices and workflows to align with sustainable principles can be met with resistance from employees who may be accustomed to traditional methods. Overcoming this inertia and fostering a culture of sustainability within the organization requires effective communication and engagement strategies to ensure buy-in from all levels of the workforce. Additionally, navigating complex regulatory frameworks and staying compliant with evolving environmental standards pose further challenges for businesses striving to integrate sustainability into their operations.
Benefits of Sustainable Manufacturing in Smart Factories
Sustainable manufacturing practices in smart factories offer a multitude of benefits that extend beyond environmental considerations. By integrating sustainable measures into their operations, companies can significantly reduce costs associated with energy consumption and waste production. This can lead to improved profitability and long-term financial stability for businesses that prioritize sustainability.
Moreover, sustainable manufacturing in smart factories can enhance brand reputation and attract environmentally conscious consumers. As more customers demand ethically sourced and eco-friendly products, companies that embrace sustainable practices can gain a competitive edge in the market. By demonstrating a commitment to environmental responsibility, organizations can build brand loyalty and establish themselves as leaders in sustainable manufacturing.
• Reducing costs associated with energy consumption and waste production
• Improved profitability and long-term financial stability for businesses
• Enhancing brand reputation and attracting environmentally conscious consumers
• Gaining a competitive edge in the market by offering ethically sourced and eco-friendly products
• Building brand loyalty and establishing as leaders in sustainable manufacturing.
Integration of Renewable Energy Sources
The integration of renewable energy sources in smart factories is becoming increasingly prevalent as industries strive to reduce their environmental footprint. Solar panels, wind turbines, and geothermal systems are being utilized to harness clean energy, decreasing reliance on traditional fossil fuels. This shift not only helps in lowering carbon emissions but also contributes to long-term cost savings for businesses through reduced energy expenses.
By incorporating renewable energy sources into manufacturing processes, companies are solidifying their commitment to sustainability and demonstrating their responsibility towards environmental stewardship. This transition is not without its challenges, as initial investment costs and technology integration can pose hurdles. However, the long-term benefits of using renewable energy, such as improved brand reputation, regulatory compliance, and energy independence, make it a worthwhile endeavor for smart factories looking to align with global sustainability goals.
Efficient Use of Resources
Efficient use of resources is a key component in the shift towards sustainable manufacturing practices. By optimizing the use of raw materials, energy, and water, companies can reduce their environmental impact while also cutting costs. This involves implementing strategies to minimize waste and improve resource productivity throughout the manufacturing process.
One way to achieve efficient resource use is by conducting thorough energy audits to identify areas where energy can be conserved or replaced with renewable sources. Additionally, incorporating process improvements such as recycling and reusing materials can help decrease the overall resource consumption. Overall, embracing efficient use of resources not only benefits the environment but also adds value to the business by enhancing operational efficiency and competitiveness in the market.
Reduction of Waste and Emissions
In the realm of sustainable manufacturing, the reduction of waste and emissions plays a pivotal role in promoting environmental stewardship and operational efficiency. By implementing strategic measures such as optimizing production processes, enhancing energy efficiency, and recycling materials, companies can significantly minimize their environmental footprint while also cutting down on costs associated with waste disposal and emissions control.
Efforts to reduce waste and emissions extend beyond the factory floor, encompassing the entire supply chain. Collaboration with suppliers to enhance transparency, implement green procurement practices, and establish recycling processes helps in fostering a more sustainable ecosystem. Moreover, adopting circular economy principles, where products are designed for reuse, remanufacturing, and recycling, further contributes to reducing waste and emissions across the product lifecycle.
Implementation of Circular Economy Principles
Circular economy principles are increasingly being integrated into manufacturing processes to promote sustainability and resource efficiency. This approach emphasizes the reuse, refurbishment, and recycling of materials to minimize waste generation and maximize the value of resources. By adopting circular economy practices, businesses can reduce their environmental footprint, decrease reliance on finite resources, and drive innovation in product design and manufacturing techniques.
One key aspect of implementing circular economy principles is the shift towards a more holistic and interconnected approach to production and consumption. This involves rethinking how products are designed, manufactured, used, and disposed of to create a closed-loop system where materials and resources are continuously cycled back into the supply chain. By embracing this circularity mindset, manufacturers can not only reduce their environmental impact but also unlock new business opportunities and foster collaboration across industries to create a more sustainable future.
Adoption of Lean Manufacturing Techniques
Lean manufacturing techniques have gained significant popularity in the manufacturing industry due to their capacity to streamline processes and improve efficiency. By minimizing waste and optimizing production cycles, companies can reduce costs and increase productivity. Through the identification and elimination of non-value-added activities, lean manufacturing helps enhance overall operational performance.
One key aspect of adopting lean manufacturing techniques is fostering a culture of continuous improvement within the organization. This involves empowering employees at all levels to identify opportunities for enhancement and implement sustainable changes. By embracing a mindset of continuous learning and innovation, companies can drive long-term success and stay competitive in the ever-evolving market landscape.
Utilization of Advanced Technologies
Advanced technologies play a pivotal role in shaping the landscape of sustainable manufacturing practices. Through the integration of innovative solutions such as Internet of Things (IoT), Artificial Intelligence (AI), and robotics, manufacturers are able to optimize production processes, minimize energy consumption, and reduce waste generation. These cutting-edge technologies enable real-time monitoring of operations, predictive maintenance of equipment, and data-driven decision-making, leading to enhanced efficiency and productivity in smart factories.
Furthermore, the utilization of advanced technologies facilitates the implementation of circular economy principles by enabling remanufacturing, recycling, and reuse of materials and products within the manufacturing ecosystem. By leveraging automation and digitalization, companies can achieve higher resource utilization rates, lower environmental impact, and improved cost-effectiveness. The seamless integration of advanced technologies not only drives operational excellence but also fosters a culture of innovation and sustainability within the manufacturing industry.
Employee Training and Engagement
Employee training and engagement play a crucial role in the successful implementation of sustainable manufacturing practices. By providing employees with the necessary skills and knowledge, companies can empower their workforce to actively participate in sustainability initiatives. Training programs can help employees understand the importance of sustainable practices, as well as how their individual actions contribute to the overall environmental and social impact of the organization.
Engagement is equally important in fostering a culture of sustainability within the workplace. When employees feel engaged and valued, they are more likely to embrace sustainability goals and actively seek ways to improve processes and reduce environmental impact. Organizations can encourage employee engagement through open communication, recognition of achievements, and by involving employees in decision-making processes related to sustainability initiatives. By fostering a sense of ownership and shared responsibility, companies can create a dedicated and motivated workforce committed to driving sustainable change.
Collaboration with Suppliers for Sustainability
Collaboration with suppliers is essential for the success of sustainability initiatives in manufacturing. By forming strong partnerships with suppliers, companies can ensure that sustainability standards and practices are upheld throughout the entire supply chain. This collaboration involves open communication, shared goals, and mutual accountability to drive positive environmental and social impacts.
When suppliers are actively engaged in sustainability efforts, it creates a ripple effect that extends beyond the individual company. By working together to implement sustainable practices, companies and their suppliers can collectively reduce waste, optimize resource usage, and minimize environmental footprint across the entire production process. This collaborative approach not only benefits the environment but also fosters long-term relationships built on trust and shared values.
Monitoring and Reporting Sustainability Metrics
Monitoring and reporting sustainability metrics plays a crucial role in the successful implementation of sustainable manufacturing practices. By regularly tracking key performance indicators related to environmental impact, resource consumption, and waste generation, companies can identify areas for improvement and set targets for reducing their carbon footprint. This data-driven approach allows organizations to measure their progress towards sustainability goals and make informed decisions to optimize their operations.
In addition to internal monitoring, reporting sustainability metrics enhances transparency and accountability to stakeholders, including customers, investors, and regulatory bodies. By disclosing information on their environmental performance and the steps taken to mitigate their impact, companies build trust and credibility among their stakeholders. Furthermore, sharing sustainability reports publicly not only demonstrates a commitment to sustainability but also encourages industry peers to adopt similar practices, collectively driving progress towards a more sustainable future.
Continuous Improvement Strategies
Continuous improvement strategies are essential in the realm of sustainable manufacturing. By continuously assessing and refining processes, companies can identify areas for enhancement and make incremental changes to drive greater sustainability. This iterative approach not only fosters ongoing progress but also cultivates a culture of innovation and adaptability within the organization.
Moreover, continuous improvement strategies help companies stay abreast of evolving sustainability trends and best practices. In a rapidly changing landscape, being able to pivot and adjust strategies in real-time is paramount to remaining competitive and meeting the demands of both consumers and regulatory bodies. Embracing a mindset of continuous improvement ensures that companies are not only responsive to current challenges but also primed to seize future opportunities for sustainable growth.
Global Impact of Sustainable Manufacturing Practices
Sustainable manufacturing practices have the profound ability to extend their positive impact far beyond local boundaries. By adopting sustainable measures such as reducing waste, conserving energy, and embracing renewable resources, manufacturers worldwide can collectively work towards mitigating environmental degradation and promoting a greener future. This global shift towards sustainability not only benefits the environment but also contributes to enhanced social responsibility and economic growth on a global scale.
Furthermore, the adoption of sustainable manufacturing practices can lead to the establishment of more resilient supply chains that are better equipped to withstand global challenges such as climate change and resource scarcity. By fostering collaboration between industries, countries, and stakeholders, sustainable practices pave the way for a more interconnected and sustainable global economy. As manufacturers increasingly prioritize sustainable initiatives, the ripple effect of these environmentally conscious decisions can be felt across borders, driving positive change and inspiring a new era of responsible manufacturing practices.
Additional Resources:
[catlist categorypage=”yes”]
Table of Contents
Categories:
[categories orderby=name]
Latest Posts:
[sbs_latest_posts]
FAQs:
What are some challenges in implementing sustainable practices in manufacturing?
Some challenges in implementing sustainable practices in manufacturing include initial investment costs, resistance to change from employees, and lack of awareness about the benefits of sustainability.
What are the benefits of sustainable manufacturing in smart factories?
The benefits of sustainable manufacturing in smart factories include increased energy efficiency, reduced operating costs, improved production quality, and enhanced brand reputation.
How can renewable energy sources be integrated into manufacturing processes?
Renewable energy sources can be integrated into manufacturing processes through the installation of solar panels, wind turbines, and other renewable energy systems to reduce reliance on non-renewable energy sources.
How can the efficient use of resources help in sustainable manufacturing?
The efficient use of resources in manufacturing can help reduce waste, minimize energy consumption, and optimize production processes to improve overall sustainability performance.
What is the importance of implementing circular economy principles in manufacturing?
Implementing circular economy principles in manufacturing can help reduce waste generation, promote resource efficiency, and create new revenue streams through the reuse and recycling of materials.
How does employee training and engagement play a role in sustainable manufacturing practices?
Employee training and engagement are crucial in promoting a culture of sustainability within the organization, increasing awareness about sustainable practices, and encouraging employees to actively participate in sustainability initiatives.
Why is collaboration with suppliers important for sustainability in manufacturing?
Collaborating with suppliers for sustainability can help ensure the responsible sourcing of materials, reduce environmental impact across the supply chain, and drive innovation in sustainable manufacturing practices.
How can monitoring and reporting sustainability metrics help in improving sustainability performance?
Monitoring and reporting sustainability metrics can provide valuable insights into the environmental impact of manufacturing operations, identify areas for improvement, and track progress towards sustainability goals.
What are some continuous improvement strategies for sustainable manufacturing practices?
Continuous improvement strategies for sustainable manufacturing practices include setting clear sustainability goals, conducting regular audits, implementing feedback mechanisms, and investing in research and development for sustainable technologies.