The Importance of Sustainable Manufacturing
Sustainable manufacturing has become a pivotal aspect of modern industrial operations. It involves adopting practices that minimize environmental impact, reduce resource consumption, and prioritize social responsibility. Companies worldwide are recognizing the importance of integrating sustainability into their production processes to align with global goals for a greener future.
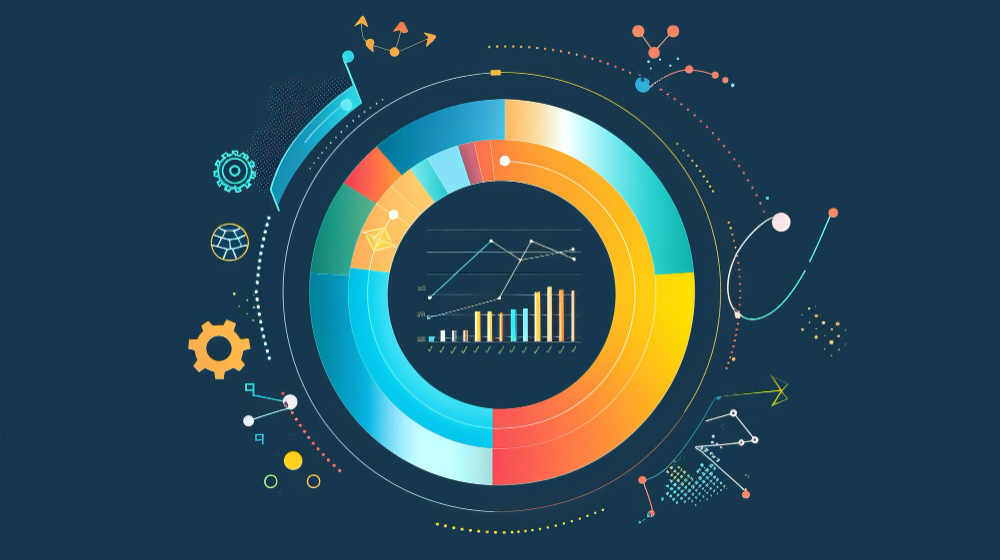
By embracing sustainable manufacturing principles, businesses can enhance their reputation, meet regulatory requirements, and appeal to eco-conscious consumers. Operating in a sustainable manner not only helps in preserving the environment but also leads to long-term cost savings through efficient resource utilization and waste reduction. In today’s competitive market, sustainable manufacturing is not just a moral obligation but also a strategic necessity for long-term business success.
The Principles of Circular Economy in Manufacturing
Circular economy in manufacturing emphasizes the importance of reducing waste and maximizing the use of resources throughout the production process. One of the key principles is designing products that can be easily disassembled and recycled at the end of their lifecycle. By creating products with a focus on durability and recyclability, manufacturers can contribute to a more sustainable and resource-efficient economy.
Another principle of circular economy in manufacturing is the concept of extending the lifespan of products through refurbishment, remanufacturing, or recycling. This approach aims to minimize the need for new raw materials by keeping products in use for as long as possible. By implementing strategies to repair and reutilize products, manufacturers can significantly reduce their environmental impact and contribute to the conservation of natural resources.
Advantages of Implementing Smart Factory Technologies
Smart factory technologies offer a myriad of benefits for manufacturing companies looking to streamline their operations. By incorporating automation and data-driven decision-making processes, smart factories can significantly enhance production efficiency. This leads to faster turnaround times, reduced labor costs, and ultimately, increased profitability for businesses. Additionally, real-time monitoring and predictive maintenance capabilities provided by smart technologies help minimize downtime and ensure continuous operation, further boosting overall productivity.
Another advantage of implementing smart factory technologies is the opportunity for customization and flexibility in manufacturing processes. With the ability to quickly adapt to changing market demands and individual customer specifications, companies can stay ahead of the competition and offer more personalized products. This adaptability also allows for efficient resource utilization and waste reduction, contributing to a more sustainable approach to manufacturing. Ultimately, smart factories enable companies to improve quality control, optimize supply chain management, and enhance overall operational performance.
Challenges of Transitioning to a Sustainable Manufacturing Model
Transitioning to a sustainable manufacturing model poses a myriad of challenges for companies across industries. One significant obstacle is the upfront financial investment required to implement eco-friendly practices and technologies. Many companies may find it challenging to allocate resources for sustainability initiatives, especially if they perceive these initiatives as additional costs rather than long-term investments in efficiency and reputation. Additionally, the lack of expertise and knowledge in sustainable manufacturing practices can serve as a barrier to successful transition. Companies may struggle to find the right talent capable of implementing and managing sustainable initiatives within their operations.
Another common challenge in transitioning to sustainable manufacturing is the need to overhaul existing processes and supply chains. In many cases, established manufacturing methods may be deeply ingrained in a company’s operations, making it difficult to pivot towards more sustainable alternatives. Resistance to change from employees and stakeholders accustomed to traditional practices can further impede progress towards a greener manufacturing model. Moreover, the complexity of global supply chains can complicate efforts to trace and reduce the environmental impact of raw materials and components used in production. Overcoming these challenges requires a coordinated effort and a willingness to adapt and innovate in the face of sustainability goals.
How Smart Factories Can Reduce Waste and Increase Efficiency
Smart factories are at the forefront of sustainable manufacturing practices thanks to their ability to reduce waste and increase operational efficiency. By leveraging advanced technologies such as Internet of Things (IoT), artificial intelligence (AI), and data analytics, smart factories can streamline production processes and optimize resource consumption. For example, real-time monitoring of equipment performance allows for predictive maintenance, preventing unplanned downtime and reducing overall waste.
Furthermore, the integration of automation systems in smart factories improves efficiency by minimizing human error and speeding up production cycles. Robots and autonomous vehicles can handle repetitive tasks with precision and consistency, leading to higher output rates and lower defect rates. This not only reduces waste but also enhances overall operational efficiency, making smart factories a key player in the transition towards more sustainable manufacturing models.
The Role of Automation in Sustainable Manufacturing
Automation plays a crucial role in enhancing sustainable manufacturing practices by streamlining processes, reducing human error, and optimizing resource utilization. By automating repetitive tasks, manufacturers can minimize their environmental impact and enhance efficiency within their operations. Automated systems can also help in monitoring energy consumption, waste generation, and emissions, enabling companies to make data-driven decisions to minimize their ecological footprint.
Furthermore, automation fosters consistency and precision in manufacturing processes, resulting in higher product quality and decreased material waste. By integrating automation technologies such as robotics and artificial intelligence, manufacturers can streamline their production lines while promoting sustainability. These automated systems not only improve operational efficiency but also contribute to the overall sustainability goals of a company, making automation an indispensable tool in the transition towards eco-friendly manufacturing practices.
Innovative Technologies Driving the Circular Economy in Manufacturing
In the realm of manufacturing, innovative technologies play a pivotal role in advancing the principles of a circular economy. One such technology making waves is 3D printing, which offers a sustainable alternative to traditional manufacturing processes. By using additive manufacturing techniques, companies can reduce material waste and energy consumption while creating intricate designs with precision. This technology not only promotes resource conservation but also enables on-demand production, minimizing excess inventory and optimizing supply chain efficiency.
Another groundbreaking technology driving the circular economy in manufacturing is the Internet of Things (IoT). Through interconnected sensors, devices, and machines, manufacturers can gather real-time data on equipment performance, energy usage, and production processes. This level of connectivity allows for predictive maintenance, optimal resource utilization, and enhanced product customization. By embracing IoT solutions, companies can streamline operations, decrease downtime, and foster a more sustainable manufacturing ecosystem.
• 3D printing offers a sustainable alternative to traditional manufacturing processes
• Additive manufacturing reduces material waste and energy consumption
• Enables creation of intricate designs with precision
• Promotes resource conservation and on-demand production
• Internet of Things (IoT) allows for real-time data gathering in manufacturing
• Interconnected sensors, devices, and machines optimize resource utilization
• Facilitates predictive maintenance and enhanced product customization
• Streamlines operations, decreases downtime, and fosters sustainability in manufacturing ecosystem
Case Studies of Successful Smart Factory Implementations
Smart factories have revolutionized the manufacturing industry by leveraging cutting-edge technologies to optimize processes and increase efficiency. One notable case study highlights a multinational automotive company that integrated smart factory technologies to streamline production, reduce downtime, and enhance quality control. By employing automation and real-time data analytics, the company significantly improved its manufacturing operations, leading to increased productivity and cost savings.
Another successful smart factory implementation involves a leading electronics manufacturer that adopted a data-driven approach to enhance its production processes. By implementing Internet of Things (IoT) devices and advanced robotics, the company was able to minimize defects, boost output, and improve overall operational performance. This transformation not only accelerated production cycles but also enabled the manufacturer to respond quickly to market demands and deliver high-quality products effectively.
The Environmental Impact of Traditional Manufacturing Processes
Traditional manufacturing processes have long been associated with significant negative effects on the environment. One key issue is the excessive use of natural resources, such as water and fossil fuels, resulting in depletion and pollution. The emission of greenhouse gases, toxic chemicals, and air pollutants during production contributes to global warming and air pollution, posing serious health risks to both humans and ecosystems.
Additionally, the generation of large quantities of waste, including hazardous materials and non-biodegradable byproducts, further exacerbates environmental degradation. Improper disposal of these wastes can contaminate soil, water bodies, and the atmosphere, leading to long-term environmental consequences. Overall, the environmental impact of traditional manufacturing processes underscores the urgent need for more sustainable and eco-friendly production practices.
Ways to Incorporate Circular Economy Practices in Manufacturing
Circular economy practices can be seamlessly integrated into manufacturing processes by focusing on strategies such as product redesign, resource optimization, and waste reduction. By designing products with longevity and repairability in mind, manufacturers can extend the lifespan of their products and minimize the need for frequent replacements. Additionally, implementing measures to reuse and recycle materials within the production cycle can significantly decrease the environmental impact of manufacturing operations. These practices not only contribute to a more sustainable approach to manufacturing but also create opportunities for cost savings and operational efficiency.
Furthermore, fostering collaboration and partnerships with suppliers, customers, and other stakeholders can play a crucial role in driving the adoption of circular economy practices in manufacturing. By working together to establish closed-loop systems and promote the exchange of resources and expertise, manufacturers can create a more circular and sustainable value chain. This collaborative approach not only enhances resource efficiency and waste reduction but also fosters innovation and encourages the development of new business models that prioritize environmental and social responsibility.
The Economic Benefits of Adopting Sustainable Manufacturing Practices
Incorporating sustainable manufacturing practices not only benefits the environment but also brings significant economic advantages to businesses. By reducing energy consumption, optimizing resources, and minimizing waste generation, companies can lower their production costs and increase their overall profitability. Moreover, adopting sustainable practices can enhance a company’s reputation and attract environmentally-conscious consumers, leading to a competitive edge in the market.
Additionally, sustainable manufacturing practices can drive innovation and foster a culture of continuous improvement within organizations. Companies that prioritize sustainability often invest in research and development to develop more efficient processes and eco-friendly products. These innovations can open up new markets, increase market share, and create new revenue streams, positioning businesses for long-term growth and success.
Collaboration and Partnerships in Advancing Sustainable Manufacturing
Collaboration among industry players is essential for advancing sustainable manufacturing practices. By working together, companies can share knowledge, resources, and best practices to collectively reduce environmental impact and improve efficiency. Partnerships between manufacturers, suppliers, and other stakeholders can lead to innovative solutions that address complex sustainability challenges.
Furthermore, collaborating with research institutions and government agencies can foster the development of new technologies and policies that support sustainable manufacturing. By bringing together expertise from various sectors, these partnerships can drive forward the adoption of environmentally friendly practices and promote the circular economy in the manufacturing industry.
Future Trends in Smart Factory and Circular Economy Integration
As industries continue to evolve, the integration of smart factory technologies and circular economy principles is set to shape the future of manufacturing. The convergence of real-time data analytics, artificial intelligence, and sustainable practices will drive unprecedented levels of efficiency, waste reduction, and resource optimization in production processes.
One of the key trends in this integration is the development of interconnected systems that allow for seamless communication between various components of the manufacturing ecosystem. This will enable predictive maintenance, enhanced energy management, and improved supply chain transparency, all contributing to a more sustainable and cost-effective operation. Such advancements will not only drive innovation and competitiveness but also pave the way for a greener and more environmentally conscious manufacturing landscape.
Additional Resources:
[catlist categorypage=”yes”]
Table of Contents
Categories:
[categories orderby=name]
Latest Posts:
[sbs_latest_posts]
FAQs:
What is the importance of sustainable manufacturing?
Sustainable manufacturing is important because it helps reduce environmental impact, improve resource efficiency, and meet growing consumer demand for eco-friendly products.
What are the principles of circular economy in manufacturing?
The principles of circular economy in manufacturing include designing products for durability and recyclability, promoting the reuse of materials, and minimizing waste throughout the production process.
What are some advantages of implementing smart factory technologies?
Implementing smart factory technologies can lead to increased efficiency, reduced waste, improved quality control, and enhanced production flexibility.
What are some challenges of transitioning to a sustainable manufacturing model?
Challenges of transitioning to a sustainable manufacturing model include high initial costs, resistance to change from traditional practices, and the need for skilled workforce training.
How can smart factories reduce waste and increase efficiency?
Smart factories can reduce waste and increase efficiency through real-time monitoring, predictive maintenance, and intelligent data analysis to optimize production processes.
What is the role of automation in sustainable manufacturing?
Automation plays a key role in sustainable manufacturing by increasing productivity, reducing human error, and minimizing energy consumption.
What are some innovative technologies driving the circular economy in manufacturing?
Some innovative technologies driving the circular economy in manufacturing include additive manufacturing, IoT sensors, blockchain for supply chain transparency, and AI-powered predictive analytics.
What are some ways to incorporate circular economy practices in manufacturing?
Ways to incorporate circular economy practices in manufacturing include implementing closed-loop systems, promoting product take-back programs, and collaborating with suppliers to source sustainable materials.
What are the economic benefits of adopting sustainable manufacturing practices?
The economic benefits of adopting sustainable manufacturing practices include cost savings from resource efficiency, increased market competitiveness, and improved brand reputation among environmentally-conscious consumers.
How can collaboration and partnerships advance sustainable manufacturing?
Collaboration and partnerships among manufacturers, suppliers, governments, and NGOs can help share best practices, drive innovation, and create a more sustainable ecosystem for manufacturing industries.