The Importance of Preventive Maintenance
Preventive maintenance is a crucial aspect of ensuring the smooth operation of machinery and equipment in various industries. By regularly conducting inspections, servicing, and repairs before any breakdowns occur, organizations can avoid costly downtime and production delays. This proactive approach helps in identifying potential issues early on, allowing for timely interventions to prevent more significant problems from arising.
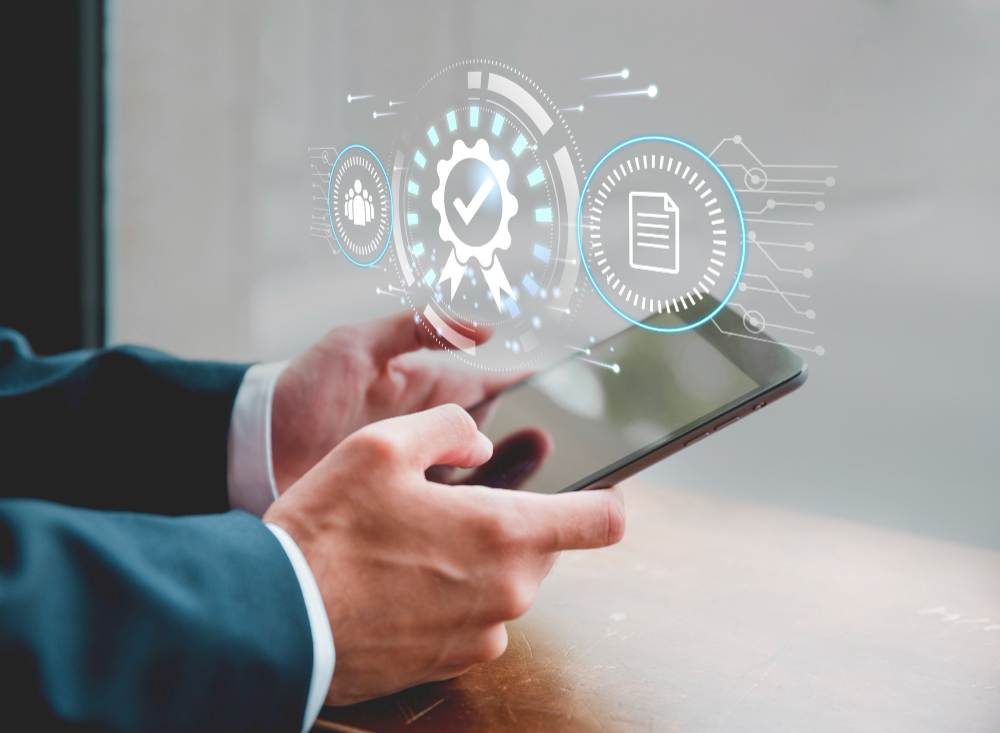
Incorporating preventive maintenance not only extends the lifespan of assets but also enhances their overall performance and efficiency. By adhering to a scheduled maintenance plan, businesses can minimize unexpected breakdowns, reduce repair costs, and improve operational reliability. Additionally, a well-maintained system leads to increased safety for workers, ensuring a secure working environment and regulatory compliance.
Understanding the Role of Data Analytics
Data analytics plays a vital role in predictive maintenance strategies by utilizing historical and real-time data to identify patterns, anomalies, and potential failures in machinery and equipment. By analyzing large datasets, maintenance teams can proactively address issues before they escalate, reducing downtime and maintenance costs. This data-driven approach enables companies to shift from reactive to proactive maintenance practices, ultimately enhancing overall operational efficiency.
Moreover, data analytics allows for the optimization of maintenance schedules and resource allocation based on machine health and performance data. By leveraging predictive analytics models, organizations can prioritize maintenance tasks, allocate resources efficiently, and minimize unplanned downtime. This proactive approach not only improves equipment reliability but also extends the lifespan of assets, leading to increased productivity and cost savings in the long run.
Implementing Condition Monitoring Technologies
Condition monitoring technologies play a crucial role in modern maintenance strategies by enabling real-time monitoring of equipment health and performance. By utilizing various sensors and data collection devices, organizations can proactively identify potential issues before they escalate into costly downtime or failures. This proactive approach allows for timely interventions and targeted maintenance actions, ultimately extending the lifespan of assets and improving overall operational efficiency.
Implementing condition monitoring technologies involves strategically placing sensors on critical equipment to capture relevant data points. This data is then analyzed through advanced algorithms and machine learning techniques to detect patterns and anomalies indicative of potential faults or failures. By continuously monitoring equipment condition, organizations can move away from traditional reactive maintenance practices towards a more predictive and proactive maintenance approach, saving both time and resources in the long run.
Utilizing IoT Sensors for Real-Time Monitoring
One of the key advancements in predictive maintenance is the utilization of IoT sensors for real-time monitoring in smart factories. These sensors are capable of collecting vast amounts of data from various machines and equipment, providing real-time insights into their performance and health. By continuously monitoring parameters such as temperature, vibration, and energy consumption, these IoT sensors enable maintenance teams to detect potential issues before they escalate into costly breakdowns.
Moreover, IoT sensors facilitate the implementation of condition-based maintenance strategies by allowing maintenance teams to track equipment performance trends over time. This data-driven approach enables predictive maintenance actions to be taken based on actual equipment condition rather than predetermined maintenance schedules. With the help of IoT sensors, organizations can optimize their maintenance practices, reduce downtime, and extend the lifespan of critical assets, ultimately leading to improved operational efficiency and cost savings.
The Benefits of Predictive Maintenance in Smart Factories
Predictive maintenance in smart factories offers numerous benefits to organizations looking to optimize their operations. By leveraging advanced data analytics and condition monitoring technologies, companies can proactively identify potential equipment failures before they occur. This proactive approach helps minimize unplanned downtime, improve overall equipment efficiency, and ultimately reduce maintenance costs.
Furthermore, predictive maintenance enables smart factories to transition from traditional reactive maintenance practices to a more strategic and efficient maintenance model. With real-time monitoring through IoT sensors and predictive maintenance software, manufacturers can schedule maintenance tasks based on actual equipment conditions rather than fixed time intervals. This shift not only increases equipment lifespan but also enhances production consistency and quality in the long run.
Challenges in Implementing Predictive Maintenance Strategies
One of the challenges encountered in implementing predictive maintenance strategies is the initial investment required for acquiring and setting up the necessary technology and tools. Many organizations may find it daunting to allocate resources for such systems, especially if they are already operating on tight budgets. Additionally, integrating predictive maintenance software with existing infrastructure and processes can be complex and time-consuming, requiring careful planning and execution.
Another obstacle in the adoption of predictive maintenance strategies is the resistance or lack of buy-in from employees at various levels within the organization. Some may be skeptical about the effectiveness of predictive maintenance or may fear that it will replace their roles. Overcoming this challenge involves transparent communication, extensive training, and showcasing the benefits of predictive maintenance in improving overall efficiency and reducing downtime.
Choosing the Right Predictive Maintenance Software
When selecting predictive maintenance software, it is crucial to consider the specific needs and requirements of your organization. Evaluate the features and functionalities of different software options against your maintenance goals and existing infrastructure. Look for a software solution that offers scalability, real-time monitoring capabilities, integration with IoT sensors, and user-friendly interfaces to ensure seamless implementation and user adoption.
Additionally, assess the vendor’s track record, customer support services, and potential for customization to tailor the software to your unique operational processes. Conduct thorough research, request demos, and gather feedback from other industry professionals to make an informed decision. Investing in the right predictive maintenance software can lead to improved asset reliability, reduced downtime, and increased productivity in your maintenance operations.
Creating a Predictive Maintenance Schedule
To create an effective predictive maintenance schedule, it is essential to start by conducting a thorough assessment of the equipment and machinery in your facility. This assessment should include identifying critical assets, determining their failure modes and consequences, and establishing baseline performance metrics. By understanding the specific needs of each asset, you can tailor your maintenance schedule to focus on preventing the most impactful failures.
Once you have gathered the necessary data and insights, the next step is to develop a detailed maintenance plan that outlines the tasks, frequencies, and resources required for each asset. This plan should consider factors such as equipment usage patterns, environmental conditions, and historical maintenance records. By having a clear schedule in place, you can proactively address potential issues before they escalate, minimize downtime, and maximize the lifespan of your assets.
• Conduct a thorough assessment of equipment and machinery
• Identify critical assets, failure modes, and consequences
• Establish baseline performance metrics
• Tailor maintenance schedule to prevent impactful failures
Once the necessary data is gathered:
• Develop a detailed maintenance plan for each asset
• Outline tasks, frequencies, and required resources
• Consider equipment usage patterns and environmental conditions
• Utilize historical maintenance records for insights
Having a clear schedule in place allows you to:
• Proactively address potential issues before escalation
• Minimize downtime
• Maximize the lifespan of assets
Training Employees on Predictive Maintenance Practices
To ensure the successful implementation of predictive maintenance practices in a manufacturing facility, providing adequate training to employees is crucial. Training sessions should cover various aspects of predictive maintenance, including the importance of data collection, analysis techniques, and interpreting results. By investing in comprehensive training programs, employees can develop the necessary skills to effectively utilize predictive maintenance tools and technologies.
Moreover, incorporating hands-on training exercises can enhance employees’ understanding and proficiency in conducting predictive maintenance tasks. Practical sessions allow employees to apply theoretical knowledge in real-world scenarios, improving their problem-solving abilities and decision-making skills. By continuously updating training programs to align with the latest industry trends and advancements in predictive maintenance technology, companies can empower their workforce to proactively manage equipment maintenance and optimize operational efficiency.
Integrating Predictive Maintenance with Overall Maintenance Strategies
Predictive maintenance is a powerful tool that can enhance overall maintenance strategies within a manufacturing setting. By integrating predictive maintenance techniques with existing maintenance practices, organizations can proactively address equipment failures before they occur, minimizing downtime and reducing operational costs. This seamless integration allows maintenance teams to transition from reactive to proactive maintenance, resulting in improved equipment reliability and increased productivity.
When incorporating predictive maintenance into overall maintenance strategies, it is essential to establish clear communication channels between maintenance technicians and data analysts. This collaboration ensures that data collected from predictive maintenance technologies is effectively analyzed and translated into actionable insights for maintenance activities. By fostering a culture of data-driven decision-making, organizations can optimize maintenance schedules, prioritize critical assets, and continuously improve predictive maintenance processes to achieve operational excellence.
Measuring the Success of Predictive Maintenance Programs
To evaluate the effectiveness of predictive maintenance programs, key performance indicators (KPIs) play a crucial role in providing insights into the program’s success. KPIs such as equipment uptime, maintenance costs, mean time between failures (MTBF), and overall equipment effectiveness (OEE) are commonly used metrics to assess the impact of predictive maintenance initiatives. By tracking these KPIs over time, organizations can quantify the benefits of implementing predictive maintenance strategies and identify areas for improvement.
Additionally, feedback from maintenance technicians and operators can offer valuable perspectives on the effectiveness of predictive maintenance efforts. Their input on the ease of use of predictive maintenance tools, the accuracy of predictive alerts, and the overall impact on daily operations can provide qualitative data to complement quantitative KPIs. Creating a feedback loop that encourages continuous improvement based on frontline experiences can help refine predictive maintenance programs and optimize their success in enhancing equipment reliability and productivity.
Case Studies of Successful Predictive Maintenance Implementation
Smart factories have been at the forefront of leveraging predictive maintenance to optimize their operations. One case study that exemplifies successful implementation is a leading automotive manufacturer that utilized sensor data and analytics to predict potential equipment failures before they occurred. By adopting a proactive approach, the company reduced downtime, increased productivity, and saved on maintenance costs significantly.
Another notable case study involves a large food processing plant that integrated IoT sensors with predictive maintenance software. By collecting real-time data on machine performance and using advanced analytics, the plant was able to identify patterns indicating potential issues. This proactive approach allowed the plant to schedule maintenance during planned downtime, ensuring uninterrupted production and maximizing overall efficiency.
Future Trends in Predictive Maintenance Technology
Looking ahead, the future of predictive maintenance technology is poised for significant advancements. One key trend on the horizon is the integration of artificial intelligence and machine learning algorithms to enhance predictive maintenance capabilities. These sophisticated technologies will enable even more accurate predictions of when equipment failures are likely to occur, allowing maintenance teams to intervene proactively and prevent costly downtime.
Another emerging trend is the increased use of drones for inspection and monitoring purposes in industrial settings. Drones equipped with cameras and sensors can efficiently survey large and hard-to-reach areas, providing valuable data for predictive maintenance analysis. This application of drone technology not only improves the efficiency of maintenance operations but also enhances overall safety by reducing the need for manual inspections in hazardous environments.
Additional Resources:
[catlist categorypage=”yes”]
Table of Contents
Categories:
[categories orderby=name]
Latest Posts:
[sbs_latest_posts]
FAQs:
What is the difference between preventive maintenance and predictive maintenance?
Preventive maintenance involves regularly scheduled maintenance tasks to prevent equipment failure, while predictive maintenance uses data and analytics to predict when maintenance is needed.
How does data analytics play a role in predictive maintenance?
Data analytics helps to analyze historical data, identify patterns, and make predictions about when maintenance is needed to prevent breakdowns.
What are some challenges in implementing predictive maintenance strategies?
Some challenges include getting buy-in from management, collecting and analyzing the right data, and integrating predictive maintenance with overall maintenance strategies.
How can IoT sensors be utilized for real-time monitoring in predictive maintenance?
IoT sensors can collect real-time data on equipment performance, allowing for immediate detection of issues and predictive maintenance actions.
What are the benefits of predictive maintenance in smart factories?
Predictive maintenance can help reduce downtime, extend equipment lifespan, improve efficiency, and save costs in smart factory environments.
How can companies measure the success of their predictive maintenance programs?
Companies can measure success through metrics such as reduced downtime, increased equipment reliability, cost savings, and improved productivity.
What are some future trends in predictive maintenance technology?
Future trends include advanced AI and machine learning algorithms, edge computing for real-time analytics, and the integration of predictive maintenance with Industry 4.0 technologies.