Key Challenges in Smart Factory Data Flow Optimization
Smart factories are experiencing rapid advancements in technology, enabling seamless data flow optimization. However, amidst this progress, several key challenges have emerged. One major obstacle is the integration of diverse data sources from various production systems, leading to complexity and data silos. This can hinder the smooth flow of information critical for decision-making processes within the smart factory environment.
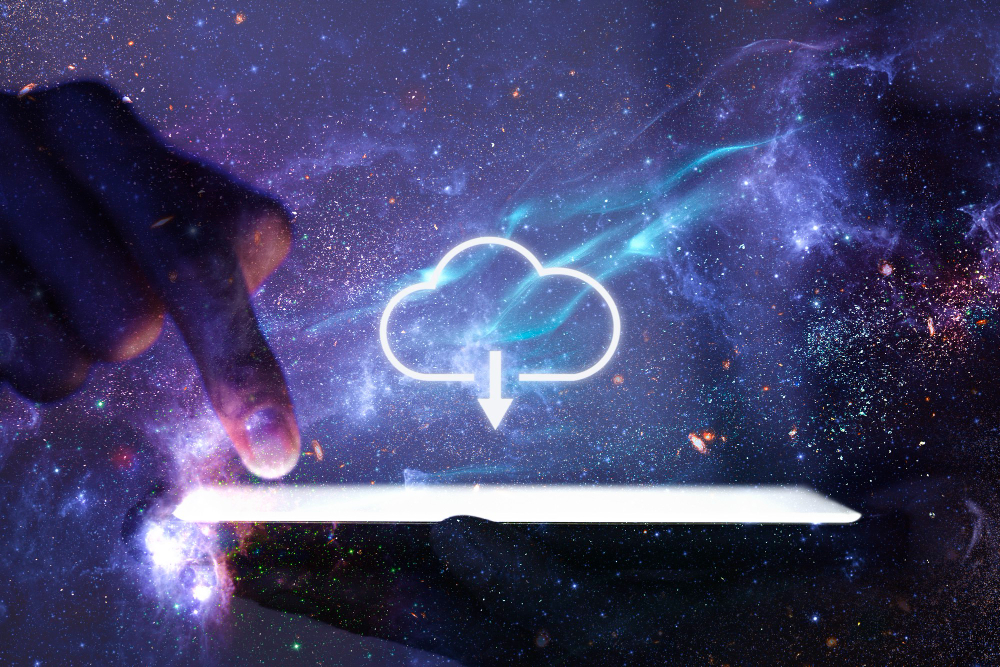
Another significant challenge lies in ensuring the security and privacy of data as it flows between edge devices and cloud platforms. With the increasing interconnectivity of devices and systems in smart factories, there is a heightened risk of cyber threats and unauthorized access to sensitive information. Finding robust solutions to protect data integrity and confidentiality is paramount in optimizing data flow and maintaining operational efficiency in smart factory settings.
Understanding the Role of Edge Computing in Smart Factories
Edge computing plays a crucial role in the realm of smart factories by enabling real-time data processing closer to the source of data generation. This approach helps minimize latency issues and reduces the burden on centralized cloud systems. By leveraging edge computing capabilities, smart factories can enhance operational efficiency, automate decision-making processes, and facilitate faster responses to production line demands.
Furthermore, edge computing enables smart factories to handle vast amounts of data with greater speed and agility. This decentralized approach not only optimizes data flow within the factory but also enhances overall system reliability and resilience. With edge computing technology, smart factories can process data at the edge of the network, enabling them to swiftly analyze and act upon data insights in a more efficient manner.
Benefits of Cloud Integration in Smart Factory Operations
Cloud integration offers numerous benefits in the realm of smart factory operations. One significant advantage is the ability to centralize data storage and processing, enabling real-time access to critical information from anywhere in the world. This centralized approach enhances collaboration among various teams within the smart factory, leading to faster decision-making and improved overall efficiency in operations.
Moreover, cloud integration provides scalability to smart factories, allowing them to adapt to changing business needs and technological advancements. By leveraging cloud resources, smart factories can easily expand their operations, implement new technologies, and accommodate increasing data volumes without the need for significant infrastructure investments. This flexibility ensures that smart factories can stay competitive and agile in today’s fast-paced manufacturing environment.
Importance of Real-Time Data Processing in Smart Factories
Real-time data processing in smart factories plays a crucial role in optimizing operational efficiency and decision-making processes. By enabling the immediate analysis of data as it is generated, organizations can respond swiftly to changing conditions on the factory floor, leading to enhanced productivity and quality control. This real-time insight allows for proactive measures to be taken, such as identifying and rectifying issues before they escalate, ultimately improving overall production outcomes.
Furthermore, the importance of real-time data processing extends to predictive maintenance practices in smart factories. By continuously monitoring equipment performance and analyzing data in real time, organizations can predict potential failures and schedule maintenance activities accordingly. This proactive approach helps prevent costly unplanned downtime, reduces maintenance costs, and extends the lifespan of machinery, ensuring smooth operations and optimal resource utilization in the manufacturing environment.
Real-time data processing in smart factories offers numerous benefits, including:
• Immediate analysis of data for swift decision-making
• Enhanced productivity and quality control on the factory floor
• Proactive measures to identify and rectify issues before they escalate
Moreover, real-time data processing is essential for predictive maintenance practices in smart factories. This includes:
• Continuous monitoring of equipment performance
• Analysis of data to predict potential failures
• Scheduling maintenance activities accordingly to prevent costly downtime
Security Considerations in Edge-to-Cloud Integration
When it comes to edge-to-cloud integration in smart factories, security considerations play a critical role in safeguarding sensitive data and ensuring the integrity of the system. One key aspect to address is data encryption, which helps protect information as it moves between devices and the cloud. Implementing robust encryption protocols can prevent unauthorized access and data breaches, providing a secure environment for data transmission and storage.
In addition to encryption, authentication measures are essential for verifying the identity of users and devices within the edge-to-cloud network. By implementing multi-factor authentication and access control mechanisms, smart factories can ensure that only authorized personnel and devices can interact with the system. This helps prevent potential security threats and unauthorized access to critical data, enhancing the overall security posture of the edge-to-cloud integration framework.
Maximizing Efficiency through Data Analytics in Smart Factories
Data analytics plays a crucial role in maximizing efficiency within smart factories. By leveraging advanced analytics tools, manufacturers can gain valuable insights from the vast amount of data generated in the production process. These insights enable them to identify patterns, trends, and inefficiencies that may otherwise go unnoticed, allowing for proactive decision-making and process optimization.
Through real-time monitoring and analysis of key performance indicators, smart factories can continuously improve their operations. Data analytics helps organizations track production metrics, equipment performance, and quality control in a more precise manner. By identifying bottlenecks, predicting maintenance needs, and optimizing workflows, manufacturers can streamline their processes, reduce downtime, and enhance overall productivity.
Integration of IoT Devices in Smart Factory Data Flow
The integration of IoT devices plays a crucial role in optimizing data flow within smart factories. These devices collect real-time data from various sensors and machines on the factory floor, enabling manufacturers to make informed decisions promptly. By seamlessly integrating IoT devices into the data flow system, smart factories can enhance operational efficiency, monitor equipment performance, and streamline production processes. This real-time data from IoT devices provides valuable insights that can drive continuous improvement and innovation in manufacturing operations.
Furthermore, the integration of IoT devices in smart factory data flow facilitates predictive maintenance strategies. By analyzing the data generated by IoT sensors, manufacturers can predict when equipment is likely to fail and proactively schedule maintenance before unplanned downtime occurs. This predictive maintenance approach not only increases the lifespan of machinery but also reduces operational costs and enhances overall productivity in smart factory settings. Additionally, by leveraging IoT device data, manufacturers can optimize energy usage, improve resource allocation, and ultimately achieve a more sustainable and competitive manufacturing environment.
Role of Artificial Intelligence in Optimizing Data Flow
Artificial Intelligence (AI) plays a crucial role in optimizing data flow within smart factories. By leveraging AI algorithms and machine learning techniques, manufacturers can analyze large amounts of data in real-time, identify patterns, and make data-driven decisions quickly and efficiently. AI technologies enable predictive maintenance, quality control, and process optimization by continuously learning from the data generated within the smart factory environment.
Furthermore, AI-powered systems can automate data processing tasks, reducing the need for manual intervention and streamlining operations. By implementing AI in data flow optimization, smart factories can enhance their overall efficiency, productivity, and quality output. The ability of AI to adapt and evolve based on changing data patterns makes it a valuable asset in managing and optimizing the flow of data within the smart factory ecosystem.
Implementing Predictive Maintenance in Smart Factories
Predictive maintenance plays a crucial role in enhancing the efficiency and productivity of smart factories. By leveraging advanced data analytics and machine learning algorithms, smart factories can proactively identify potential equipment failures before they occur. This proactive approach allows for scheduled maintenance activities, minimizing unplanned downtime and optimizing overall operational performance.
Implementing predictive maintenance involves collecting and analyzing vast amounts of data from sensors and IoT devices installed in machines and equipment. By monitoring key performance indicators in real-time, smart factories can predict when maintenance is needed, leading to cost savings and increased operational reliability. Additionally, predictive maintenance enables smart factories to transition from a reactive to a proactive maintenance strategy, ultimately improving asset lifespan and driving sustainable business growth.
Enhancing Supply Chain Management through Data Integration
Supply chain management plays a crucial role in the success of smart factories by ensuring timely delivery of components and products. Data integration within the supply chain allows for seamless communication and collaboration between various stakeholders, leading to improved efficiency and reduced operational costs. By integrating data from different sources such as suppliers, logistics partners, and production units, smart factories can gain real-time insights into inventory levels, demand forecasts, and shipment tracking, enabling them to make informed decisions for optimizing their supply chains.
Furthermore, data integration facilitates a more transparent and responsive supply chain, allowing smart factories to quickly adapt to changing market demands and unforeseen disruptions. With interconnected systems and shared data repositories, stakeholders can access accurate and up-to-date information, leading to better coordination and faster problem resolution. By leveraging data integration technologies, smart factories can streamline their supply chain processes, enhance inventory management, and ultimately deliver superior products and services to customers.
Scalability and Flexibility in Edge-to-Cloud Integration
Scalability and flexibility are imperative in the seamless integration of edge and cloud technologies within smart factories. The ability to scale the data flow infrastructure based on the evolving needs of the factory ensures smooth operations without bottlenecks. Moreover, flexibility allows for quick adjustments and accommodations to varying workloads and requirements, enabling the system to adapt rapidly to changing conditions and demands.
In the context of edge-to-cloud integration, scalability plays a crucial role in managing the increasing volume of data generated by IoT devices and sensors in smart factories. A scalable architecture can efficiently handle the growing data flow without compromising performance or creating latency issues. Additionally, flexibility in the integration allows for the easy addition of new components or services as the factory expands or adopts new technologies, ensuring that the data flow remains optimized and effective in supporting overall operations.
Best Practices for Data Flow Optimization in Smart Factories
Data flow optimization in smart factories is essential for streamlining operations and enhancing efficiency. One best practice is to establish clear data governance policies to ensure data accuracy, consistency, and security throughout the manufacturing process. This involves defining data ownership, access levels, and quality standards to maintain a reliable flow of information.
Another key practice is to leverage automation tools for data processing and analysis. By automating routine tasks such as data collection, cleansing, and reporting, smart factories can reduce manual errors and improve decision-making processes. Implementing advanced analytics tools can also help in extracting valuable insights from data streams, enabling real-time monitoring and proactive decision-making in production environments.
Case Studies: Successful Implementation of Edge-to-Cloud Integration
In a rapidly evolving industrial landscape, the successful implementation of edge-to-cloud integration has become a cornerstone for enhancing operational efficiency and driving innovation in smart factories. Several case studies highlight the transformative impact of integrating edge devices with cloud-based systems to streamline data flow and enable real-time decision-making. By seamlessly connecting edge computing capabilities with centralized cloud infrastructure, companies have been able to achieve unprecedented levels of agility and responsiveness in their manufacturing processes.
One such case study involves a leading automotive manufacturer that leveraged edge-to-cloud integration to optimize its production line efficiency. By deploying edge devices for data collection and analysis at key points along the assembly line, the company was able to monitor equipment performance in real-time and proactively address maintenance issues before they escalated. This not only minimized downtime but also improved overall equipment effectiveness, resulting in significant cost savings and enhanced production output. The seamless communication between edge devices and cloud servers enabled the factory to adapt quickly to changing production demands and continuously optimize its operations for maximum productivity.
Additional Resources:
[catlist categorypage=”yes”]
Table of Contents
Categories:
[categories orderby=name]
Latest Posts:
[sbs_latest_posts]
FAQs:
What are the key challenges in optimizing data flow in smart factories?
Key challenges in smart factory data flow optimization include ensuring real-time data processing, integrating IoT devices, and maintaining security in edge-to-cloud integration.
How does edge computing play a role in smart factories?
Edge computing helps in processing data closer to where it is generated, reducing latency and improving efficiency in smart factory operations.
What are the benefits of cloud integration in smart factory operations?
Cloud integration allows for centralized data storage, easy access to data from anywhere, and scalability for smart factory operations.
Why is real-time data processing important in smart factories?
Real-time data processing allows for quick decision-making, proactive maintenance, and efficient operations in smart factories.
What security considerations should be taken into account in edge-to-cloud integration?
Security considerations in edge-to-cloud integration include data encryption, authentication mechanisms, and secure communication protocols to protect sensitive data.
How can data analytics maximize efficiency in smart factories?
Data analytics can help in identifying trends, predicting maintenance needs, and optimizing operations for increased efficiency in smart factories.
What is the role of artificial intelligence in optimizing data flow in smart factories?
Artificial intelligence can help in analyzing large amounts of data, predicting outcomes, and automating processes for optimized data flow in smart factories.
How can predictive maintenance be implemented in smart factories?
Predictive maintenance in smart factories involves using data analytics and machine learning algorithms to predict equipment failures and schedule maintenance before issues occur.
How can data integration enhance supply chain management in smart factories?
Data integration in smart factories can provide real-time visibility into supply chain operations, optimize inventory management, and improve overall efficiency in the supply chain.
What best practices should be followed for data flow optimization in smart factories?
Best practices for data flow optimization in smart factories include ensuring data quality, implementing data governance policies, and regularly monitoring and analyzing data flow processes.
Can you provide examples of successful implementation of edge-to-cloud integration in smart factories?
Yes, case studies of successful implementation of edge-to-cloud integration in smart factories showcase how companies have improved efficiency, reduced downtime, and enhanced decision-making through seamless data flow integration.