The Impact of Robotics on Efficiency in Manufacturing
In the realm of manufacturing, the integration of robotics has revolutionized production processes, catapulting efficiency to unprecedented levels. From automating repetitive tasks to streamlining complex operations, robots have emerged as invaluable assets in driving productivity. The precision and speed at which robots operate not only reduce the margin for error but also enhance workflow consistency, ultimately leading to significant gains in overall efficiency.
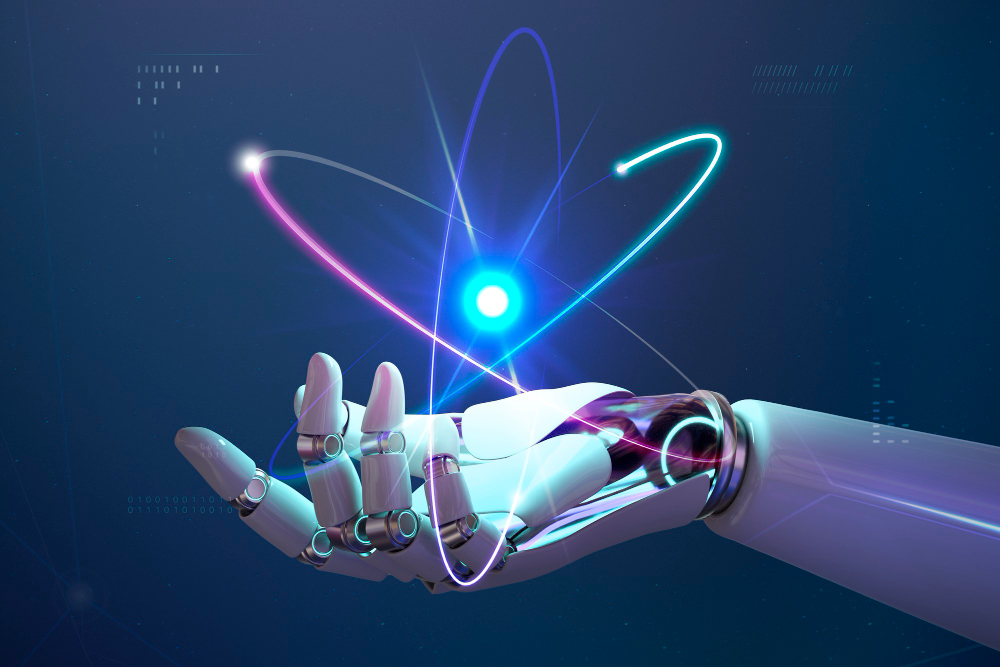
Furthermore, the flexibility of robotics in adapting to various production demands has enabled manufacturers to optimize their operations and respond swiftly to market fluctuations. By employing robots for tasks that are labor-intensive or hazardous for human workers, companies can ensure a safer working environment while bolstering efficiency. As technology continues to advance, the role of robotics in manufacturing is set to evolve, offering new possibilities for improved efficiency and innovation within the industry.
Enhancing Quality Control with Automation
Quality control is a crucial aspect of manufacturing processes, ensuring that products meet the required standards before they reach consumers. Automation has revolutionized quality control by introducing precision and consistency in inspecting products. With advanced sensors and machine learning algorithms, automated systems can detect even the slightest defects or deviations from specifications, reducing the likelihood of faulty products reaching the market.
Automated quality control systems can perform inspections at a much faster rate than manual labor, leading to increased efficiency in production lines. By leveraging technologies such as computer vision and robotics, manufacturers can streamline the inspection process and identify defects with higher accuracy. This not only improves the overall quality of products but also saves time and resources in the long run.
Safety Measures for Robotics in Manufacturing
Robotic systems are powerful tools in manufacturing processes, but they also come with inherent risks if proper safety measures are not implemented. One key aspect of ensuring safety is the fencing or physical barriers that limit access to the robotic work areas. By creating a designated space for the robots to operate, the risk of accidents involving human workers is significantly reduced.
Additionally, safety sensors play a crucial role in preventing collisions between robots and human workers or other machinery. These sensors can detect the presence of objects in the robot’s path and trigger a stop in operation, averting potential accidents. Regular maintenance and inspection of these safety sensors are essential to guarantee their effectiveness in keeping the manufacturing environment safe for all individuals involved.
Integration of Robotics with Existing Machinery
Integrating robotics with existing machinery in manufacturing processes has become a key focus for many companies looking to enhance efficiency and productivity. By seamlessly incorporating robotics into the current setup, businesses can streamline operations and optimize output without the need for major overhauls or disruptions. This integration enables a smooth transition towards automation, allowing for a more agile and responsive manufacturing environment.
The compatibility of robotics with existing machinery presents opportunities for cost-effective improvements in production processes. Manufacturers can leverage the latest advancements in robotics technology to complement their current equipment, maximizing the overall efficiency and output capacity of their operations. This integration paves the way for a harmonious coexistence between human workers and robots, creating a synergistic workflow that capitalizes on the strengths of both entities.
Cost Considerations for Implementing Automation
When considering the implementation of automation in manufacturing processes, one of the primary concerns that businesses face is the cost involved. The initial investment for purchasing robotics equipment, integrating it with existing machinery, and training employees to operate alongside these automated systems can be significant. Additionally, ongoing maintenance costs and potential software upgrades must also be factored in when evaluating the overall expenses associated with automation.
Despite the upfront costs, it is essential for businesses to look beyond the initial financial investment and consider the long-term benefits that automation can bring. Increased efficiency, improved quality control, and enhanced productivity are among the key advantages that automation offers. When weighing the cost considerations for implementing automation, it is crucial for companies to conduct a thorough cost-benefit analysis to assess the potential return on investment and the overall impact on the bottom line in the future.
Training Employees to Work Alongside Robots
To successfully integrate robots into the workforce, it is crucial to provide comprehensive training programs for employees. These training sessions should focus on familiarizing workers with the operation and maintenance of the robotic systems, as well as teaching them how to collaborate effectively with the machines. Hands-on training in simulated work environments can help employees build confidence in working alongside robots and increase their efficiency in completing tasks.
Additionally, offering ongoing support and resources for employees who may feel apprehensive about the use of robots in the workplace is essential. Encouraging open communication and providing avenues for feedback can help address any concerns or challenges that employees may encounter during the transition to a more automated environment. By fostering a culture of continuous learning and improvement, companies can ensure that their employees are equipped with the skills and knowledge needed to thrive in a collaborative work setting with robots.
The Role of Artificial Intelligence in Automation
Artificial intelligence (AI) plays a crucial role in automation by enabling machines to learn from patterns in data and make decisions without human intervention. In manufacturing, AI algorithms can analyze large datasets to identify inefficiencies in production processes and suggest optimizations. By leveraging AI technology, companies can streamline operations, reduce errors, and enhance overall productivity.
Moreover, AI-powered automation systems can adapt to changing conditions in real-time, allowing manufacturing facilities to respond swiftly to fluctuations in demand or supply chain disruptions. With the ability to predict maintenance needs and detect anomalies in production lines, AI contributes to improved efficiency and cost savings in the long run. As the capabilities of AI continue to advance, its integration with automation is expected to revolutionize the manufacturing industry by enabling smarter, more agile production processes.
Challenges of Implementing Robotics in Small Businesses
Small businesses face a myriad of challenges when it comes to implementing robotics in their operations. One common obstacle is the initial investment required to purchase and install robotic technology. For many small businesses operating on tight budgets, the cost of automation can be prohibitive, leading to hesitation in adopting these modern technological solutions. Additionally, the complexity of integrating robotics into existing workflows can pose a significant challenge for smaller enterprises that may lack the resources and expertise to navigate this process seamlessly.
Another key challenge for small businesses looking to implement robotics is the potential disruption to their current workforce. Concerns about job displacement and the need to retrain employees to work alongside robots can create uncertainty and resistance within the organization. The adjustment period as employees adapt to new technologies and processes can also result in temporary decreases in productivity and efficiency, further complicating the implementation of robotics in small business settings.
Improving Workflow with Automated Processes
Creating a seamless workflow is crucial for achieving optimal efficiency in manufacturing processes. Automation plays a significant role in streamlining tasks, reducing human errors, and expediting production timelines. By implementing automated processes, companies can eliminate bottlenecks, minimize downtime, and enhance overall productivity within their operations.
Automated workflows also enable real-time monitoring and data analysis, providing valuable insights for decision-making and continuous improvement efforts. With the integration of robotics and smart technology, tasks that were once time-consuming and labor-intensive can now be completed swiftly and accurately. This not only improves the speed of production but also ensures consistent quality outputs, leading to enhanced customer satisfaction and increased competitiveness in the market.
The Future of Manufacturing with Robotics
As technology continues to advance rapidly, the future of manufacturing with robotics looks promising. With the increasing integration of artificial intelligence and automation systems, industries are witnessing a transformation in their production processes. Robots are being designed to perform complex tasks with precision and efficiency, leading to higher productivity and streamlined operations. As a result, manufacturers are able to meet the demands of the market more effectively while also ensuring consistent quality in their products.
Moreover, the future of manufacturing with robotics also presents opportunities for customization and flexibility in production. Advanced robotics systems can be programmed to adapt to different tasks quickly, allowing manufacturers to respond to changing consumer preferences and market trends efficiently. By leveraging robotics technology, companies can achieve greater agility in their operations, enabling them to stay competitive in an ever-evolving market landscape.
Case Studies of Successful Automation Implementations
Automation has significantly revolutionized the manufacturing sector, leading to improved efficiency, reduced errors, and enhanced production capacities. A case study of a metal fabrication company showcased how incorporating robotic welding arms increased production output by 40% and reduced defect rates by 25%. The implementation of these robots not only optimized the manufacturing process but also enhanced workplace safety by handling hazardous tasks.
In another instance, a pharmaceutical company successfully integrated automated packaging systems, resulting in a 30% reduction in manual labor and an impressive 60% increase in packaging speed. This automation not only streamlined the packaging process but also ensured greater precision and accuracy in dosage and labeling. Overall, these case studies highlight the transformative impact of automation in boosting productivity and quality in manufacturing operations.
• Automation in manufacturing has led to improved efficiency and reduced errors
• Robotic welding arms increased production output by 40% and reduced defect rates by 25%
• Automated packaging systems resulted in a 30% reduction in manual labor and a 60% increase in packaging speed
• Automation ensures greater precision, accuracy, and workplace safety
Environmental Benefits of Robotics in Manufacturing
Automation in manufacturing processes utilizing robotics can lead to significant reductions in energy consumption and waste generation. By streamlining operations and optimizing production, robots can help manufacturers achieve higher levels of efficiency which ultimately results in a smaller carbon footprint. Additionally, the precision and accuracy of robotic systems contribute to minimizing errors in production, leading to less material wastage and overall increased resource efficiency.
Furthermore, the use of robotics in manufacturing can also improve air quality and workplace safety. With robots handling tasks that may be hazardous to human workers, the risk of accidents and exposure to harmful substances is reduced. This not only creates a safer working environment but also contributes to a healthier ecosystem by minimizing emissions and pollutants associated with traditional manufacturing processes.
Addressing Concerns About Job Displacement due to Automation
Job displacement due to automation is a legitimate concern in the manufacturing industry. As robots and other forms of automation become increasingly prevalent, there is a fear that many traditional manufacturing jobs may become obsolete. However, it is essential to acknowledge that while certain roles may be automated, new opportunities for employment may also arise as a result of technological advancements.
Businesses implementing automation should prioritize retraining and upskilling their workforce to adapt to the changing landscape. By investing in employee training programs focused on developing skills that complement automation, companies can ensure that their workforce remains relevant and valuable in the evolving manufacturing environment. It is crucial for businesses to communicate openly with employees about the impact of automation and provide support in navigating potential transitions within the organization.
Additional Resources:
[catlist categorypage=”yes”]
Table of Contents
Categories:
[categories orderby=name]
Latest Posts:
[sbs_latest_posts]
FAQs:
What is the impact of robotics on efficiency in manufacturing?
Robotics can greatly enhance efficiency in manufacturing by performing repetitive tasks at a faster pace and with higher accuracy than humans.
How can automation enhance quality control in manufacturing?
Automation can improve quality control by ensuring consistent production standards and detecting defects more effectively than manual inspection.
What safety measures should be taken when implementing robotics in manufacturing?
Safety measures for robotics in manufacturing include implementing barriers, emergency stop buttons, and regular maintenance to ensure safe operation.
How can robotics be integrated with existing machinery in manufacturing?
Robotics can be integrated with existing machinery through the use of compatible software and hardware interfaces, allowing for seamless operation within the manufacturing process.
What cost considerations should be taken into account when implementing automation in manufacturing?
Cost considerations for implementing automation in manufacturing include the upfront investment in robotics equipment, ongoing maintenance costs, and potential savings in labor expenses over time.
How can employees be trained to work alongside robots in manufacturing?
Employees can be trained to work alongside robots in manufacturing through hands-on training programs, workshops, and ongoing support from automation experts.
What is the role of artificial intelligence in automation?
Artificial intelligence plays a crucial role in automation by enabling robots to learn from data, make decisions, and adapt to changing conditions in the manufacturing environment.
What are the challenges of implementing robotics in small businesses?
Challenges of implementing robotics in small businesses include cost constraints, limited resources for training, and potential resistance from employees to adopt new technology.
How can workflow be improved with automated processes in manufacturing?
Workflow can be improved with automated processes in manufacturing by streamlining production tasks, reducing errors, and increasing overall efficiency in the manufacturing process.
What is the future of manufacturing with robotics?
The future of manufacturing with robotics includes increased automation, integration of artificial intelligence, and advancements in collaborative robotics to further enhance efficiency and productivity.
What are some case studies of successful automation implementations in manufacturing?
Case studies of successful automation implementations in manufacturing showcase companies that have successfully integrated robotics to improve production efficiency, quality control, and overall performance.
What are the environmental benefits of robotics in manufacturing?
The environmental benefits of robotics in manufacturing include reduced energy consumption, waste generation, and emissions, leading to a more sustainable and eco-friendly manufacturing process.
How can concerns about job displacement due to automation be addressed?
Concerns about job displacement due to automation can be addressed through retraining programs, upskilling initiatives, and creating new job opportunities in emerging industries related to robotics and automation.