The Evolution of Manufacturing
Manufacturing has undergone a remarkable evolution over the years, adapting to changing dynamics and embracing innovation to stay competitive in the global market. From traditional manual labor-intensive processes to modern automated systems, the sector has witnessed a significant shift towards efficiency and sustainability. The introduction of advanced technologies and the integration of data analytics have revolutionized the way products are designed, produced, and delivered to consumers, marking a new era in the manufacturing industry.
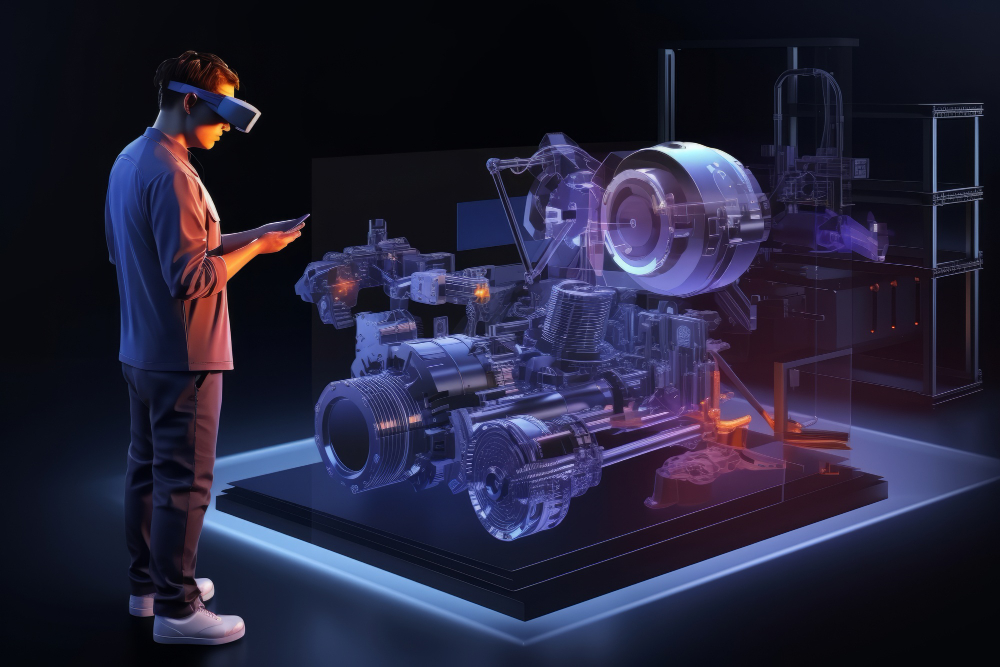
With the rise of smart factories and the Internet of Things (IoT), manufacturing processes have become more interconnected and streamlined, leading to improved productivity and cost savings. This transformation has not only accelerated production timelines but has also enhanced product quality and customer satisfaction. As manufacturers continue to embrace digitalization and automation, the evolution of manufacturing is poised to bring about further advancements in efficiency, customization, and sustainability, shaping the future of the industry.
Increased Efficiency and Productivity
One of the key drivers of progress in the manufacturing industry is the pursuit of increased efficiency and productivity. Companies are constantly seeking ways to streamline their processes and optimize their operations to meet growing demands and stay ahead of the competition. By leveraging technological advancements and adopting innovative strategies, manufacturers have been able to enhance their output while reducing costs and minimizing waste.
The implementation of automation and robotics in factory settings has revolutionized the way products are manufactured. These sophisticated systems are capable of performing repetitive tasks with precision and speed, leading to higher production rates and improved overall efficiency. By integrating machines and smart devices into the manufacturing process, companies have been able to augment their capabilities and achieve greater levels of productivity than ever before.
Integration of Technology in Manufacturing
Automation and technology have become integral components in modern manufacturing processes, revolutionizing the way products are made. The integration of advanced technologies, such as robotics, artificial intelligence, and data analytics, has led to increased efficiency, reduced waste, and improved overall productivity in factories. With the use of these technologies, manufacturers are able to streamline operations, optimize supply chains, and respond more swiftly to changing market demands.
The implementation of technology in manufacturing has also paved the way for enhanced safety and quality control measures. Automated systems and sensors can detect potential issues in real-time, allowing for immediate intervention and minimizing the risk of defects or accidents. By leveraging technology, manufacturers can ensure that their products meet the highest standards of quality and comply with regulatory requirements, thereby enhancing customer satisfaction and brand reputation.
• Automation and technology have revolutionized modern manufacturing processes
• Integration of advanced technologies like robotics, AI, and data analytics has increased efficiency
• Technology helps streamline operations, optimize supply chains, and respond swiftly to market demands
• Enhanced safety and quality control measures with automated systems and sensors detecting issues in real-time
• Technology ensures products meet high quality standards and comply with regulations for customer satisfaction
Automation in the Factory Setting
Automation in the factory setting has revolutionized traditional manufacturing processes by streamlining operations and maximizing efficiency. With the integration of advanced technologies such as robotics and artificial intelligence, tasks that once required manual labor are now being performed with precision and speed. This shift towards automation not only increases productivity but also ensures consistency in product quality, leading to higher customer satisfaction.
Furthermore, automation in the factory setting has played a significant role in enhancing workplace safety by removing workers from hazardous tasks and minimizing human errors. By implementing automated systems for routine and dangerous operations, companies can create a secure working environment while optimizing operational output. As the manufacturing industry continues to evolve, the adoption of automation in factories is poised to become a standard practice rather than an exception.
Advancements in Robotics and Artificial Intelligence
Advancements in robotics have revolutionized the manufacturing industry, allowing for increased precision, speed, and efficiency in production processes. Industrial robots are now capable of performing complex tasks with high accuracy, leading to a significant reduction in errors and waste in manufacturing operations.
Artificial intelligence (AI) has also played a crucial role in the evolution of manufacturing, enabling machines to learn from data, make decisions, and adapt to changing conditions in real-time. AI-driven systems can analyze vast amounts of data to optimize production schedules, predict maintenance needs, and enhance overall productivity in the factory setting.
Data Analytics and Predictive Maintenance
With the advent of advanced technologies in manufacturing, data analytics has become a crucial tool in optimizing processes and ensuring higher efficiency. Analyzing vast amounts of data allows manufacturers to identify patterns, trends, and anomalies that would have otherwise gone unnoticed. By leveraging data analytics, companies can take proactive measures to address potential issues before they escalate, ultimately leading to reduced downtime and increased productivity.
Predictive maintenance is another key application of data analytics in manufacturing that is revolutionizing how equipment is maintained. By utilizing historical data and real-time monitoring, manufacturers can predict when a machine is likely to fail and schedule maintenance activities accordingly. This predictive approach minimizes unexpected breakdowns, extends the lifespan of equipment, and lowers maintenance costs, ultimately leading to a more streamlined and cost-effective manufacturing process.
Enhanced Safety and Quality Control Measures
Safety and quality control are paramount in any manufacturing setting. By implementing advanced technologies such as sensors and real-time monitoring systems, companies can ensure that their processes adhere to strict safety standards. These measures not only protect workers from potential hazards but also contribute to the overall quality of the products being produced.
Furthermore, the use of data analytics plays a crucial role in identifying any deviations from the set quality standards. By analyzing vast amounts of data in real-time, manufacturers can proactively address any issues that might affect the quality of their products. This proactive approach not only enhances overall quality control but also minimizes the risk of defects reaching the end consumer, thereby safeguarding the reputation of the company.
Supply Chain Optimization in Smart Factories
Supply chain optimization in smart factories leverages advanced technologies to streamline operations and enhance overall efficiency. Through the integration of Internet of Things (IoT) devices and data analytics, manufacturers can monitor and manage inventory levels in real-time, reducing stockouts and minimizing excess inventory. This real-time visibility also enables companies to make informed decisions proactively, ensuring a smoother flow of materials and goods throughout the supply chain.
Furthermore, smart factories are embracing predictive maintenance strategies to anticipate and address potential disruptions in the supply chain. By utilizing sensors and machine learning algorithms, manufacturers can predict equipment failures before they occur, leading to reduced downtime and increased productivity. These predictive maintenance practices not only optimize the supply chain but also contribute to cost savings and improved customer satisfaction.
Impact of Internet of Things (IoT) in Manufacturing
The integration of the Internet of Things (IoT) in manufacturing has revolutionized how factories operate. IoT devices such as sensors, actuators, and connected machinery collect real-time data that enables decision-makers to monitor processes remotely and make informed decisions swiftly. This seamless flow of information has greatly enhanced operational efficiency and enabled predictive maintenance to prevent costly downtime.
Furthermore, the IoT has enabled manufacturers to track and optimize the entire production process from raw material sourcing to distribution. By harnessing IoT data analytics, companies can streamline supply chain logistics, reduce waste, and improve overall quality control measures. The IoT’s impact on manufacturing is undeniable, paving the way for smarter factories that are more agile, responsive, and adaptive to market demands.
Environmental Sustainability in Smart Factories
One key aspect of smart factories is their focus on environmental sustainability. By integrating advanced technology and data analytics, smart factories have the capability to monitor and optimize energy consumption, reducing waste and minimizing the carbon footprint of their operations. This proactive approach not only benefits the environment but also leads to cost savings for manufacturers in the long run.
Additionally, smart factories often implement green practices such as recycling and waste reduction programs, as well as the use of eco-friendly materials and packaging solutions. These initiatives align with the growing global demand for sustainable and environmentally responsible production methods. By prioritizing environmental sustainability, smart factories are not only contributing to a greener future but also enhancing their brand reputation and market competitiveness in an increasingly environmentally conscious world.
Challenges and Opportunities in Implementing Smart Factory Concepts
Implementing smart factory concepts presents several challenges that organizations need to navigate. One significant hurdle is the high initial investment required to set up smart manufacturing systems. Companies may face resistance to change from employees accustomed to traditional factory processes, necessitating training and organizational restructuring. Additionally, ensuring the compatibility of various technologies and software within the integrated smart factory framework poses a complex task for decision-makers.
On the flip side, embracing smart factory concepts offers a world of opportunities for manufacturers. Enhanced efficiency and productivity can lead to cost savings and increased competitiveness in the market. Smart factories enable real-time data monitoring and analytics, empowering businesses to make informed decisions swiftly. Furthermore, the integration of advanced technologies like robotics and artificial intelligence can revolutionize production processes, promoting innovation and growth for organizations willing to adopt these transformative manufacturing practices.
Case Studies of Successful Smart Factory Implementations
One notable case study of a successful smart factory implementation is that of Company X, a global manufacturing giant that integrated cutting-edge IoT technology into its production processes. By leveraging real-time data analytics and machine learning algorithms, Company X was able to optimize its production schedule, reduce downtime, and enhance quality control measures significantly. As a result, the company experienced a substantial increase in overall efficiency and productivity, ultimately leading to significant cost savings and improved customer satisfaction.
Another compelling example comes from Company Y, a leading automotive manufacturer that embraced automation and robotics in its factory setting. By deploying advanced robotic systems for tasks such as assembly and material handling, Company Y streamlined its operations and achieved a remarkable increase in output without compromising on quality. The integration of these technologies not only allowed the company to meet growing market demands more effectively but also enhanced workplace safety by reducing the risk of human errors. Company Y’s successful implementation of smart factory concepts serves as a testament to the transformative power of leveraging technology in manufacturing processes.
The Future of Manufacturing: Smart Factory Revolution
The Smart Factory Revolution is set to transform the landscape of manufacturing as we know it. With the integration of cutting-edge technologies such as artificial intelligence, robotics, and data analytics, factories are becoming increasingly efficient, adaptable, and interconnected. This revolution is paving the way for a new era of production, where processes are streamlined, downtime is minimized, and quality is optimized to unprecedented levels.
By harnessing the power of the Internet of Things (IoT) and implementing sustainable practices, smart factories are redefining the way products are manufactured and delivered. Real-time data insights, predictive maintenance, and automated processes are enabling manufacturers to optimize their supply chains, reduce waste, and improve overall environmental sustainability. As these advancements continue to evolve, the smart factory revolution is poised to usher in a new era of industry where innovation, efficiency, and sustainability converge seamlessly.
Additional Resources:
[catlist categorypage=”yes”]
Table of Contents
Categories:
[categories orderby=name]
latest Posts:
[sbs_latest_posts]
FAQs:
What is a smart factory?
A smart factory is a manufacturing facility that utilizes advanced technologies such as automation, robotics, data analytics, and the Internet of Things (IoT) to improve efficiency, productivity, and safety.
How does technology integration benefit manufacturing?
Technology integration in manufacturing leads to increased efficiency, reduced downtime, improved quality control, and enhanced decision-making through data analytics.
What role does automation play in the factory setting?
Automation in the factory setting involves the use of machines and robots to perform tasks traditionally done by humans, leading to higher productivity, accuracy, and cost-effectiveness.
How are robotics and artificial intelligence advancing manufacturing?
Robotics and artificial intelligence are revolutionizing manufacturing by enabling tasks that were previously too complex or dangerous for humans, increasing precision, speed, and flexibility in production processes.
What is predictive maintenance and how does it impact manufacturing?
Predictive maintenance uses data analytics to anticipate equipment failures and schedule maintenance before breakdowns occur, reducing downtime and improving overall equipment effectiveness in manufacturing.
How do smart factories enhance safety and quality control measures?
Smart factories use sensors, cameras, and AI algorithms to monitor processes in real-time, identifying potential hazards, ensuring compliance with safety regulations, and maintaining high standards of product quality.
What is the role of the Internet of Things (IoT) in manufacturing?
The IoT connects devices, sensors, and machines in the manufacturing process, enabling real-time data collection, analysis, and communication to optimize production, maintenance, and supply chain management.
How do smart factories contribute to environmental sustainability?
Smart factories reduce energy consumption, waste generation, and carbon emissions through efficient resource utilization, recycling practices, and environmentally-friendly production processes.
What are the challenges and opportunities in implementing smart factory concepts?
Challenges in implementing smart factory concepts include high initial costs, cybersecurity risks, and workforce training needs, while opportunities include improved operational efficiency, competitive advantage, and innovation potential.
Can you provide examples of successful smart factory implementations?
Case studies of successful smart factory implementations include companies like Siemens, Bosch, and BMW, which have seen significant improvements in production efficiency, quality control, and customer satisfaction through the adoption of smart technologies.