The Benefits of IIoT in Industrial Automation
One of the key benefits of IIoT in industrial automation is the ability to improve operational efficiency. By leveraging connected devices and sensors, manufacturers can gather real-time data on production processes, machine performance, and inventory levels. This data enables companies to identify bottlenecks, streamline workflows, and optimize resource allocation, ultimately leading to increased productivity and cost savings.
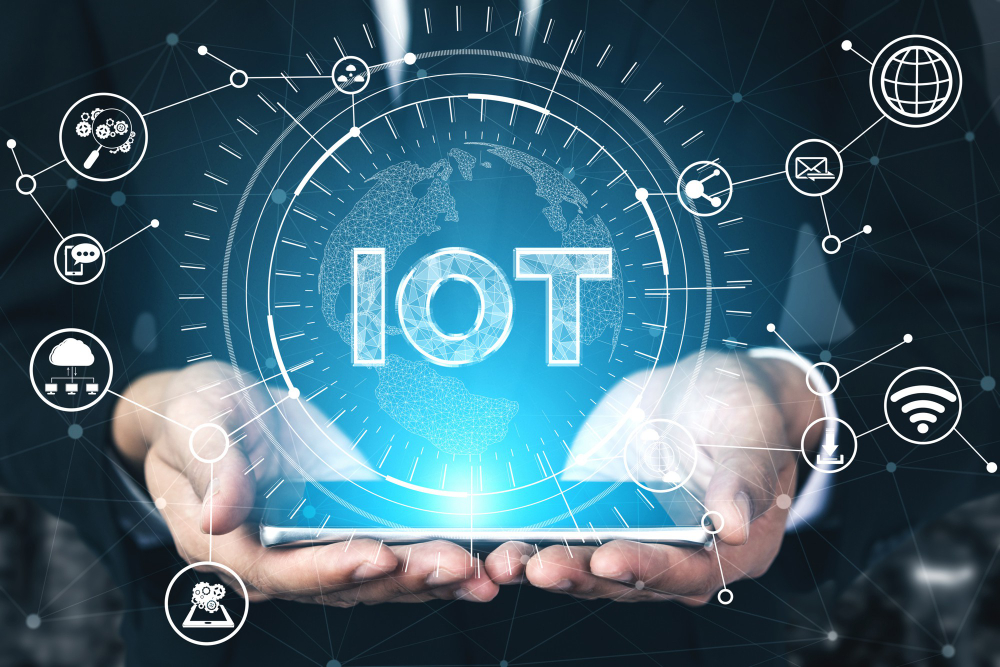
Another advantage of implementing IIoT in industrial automation is the enhanced visibility it provides across the entire manufacturing process. With interconnected systems and automated monitoring capabilities, businesses can gain valuable insights into their operations, identify potential issues before they escalate, and make data-driven decisions to improve overall performance. This level of visibility not only enhances operational efficiency but also enables companies to respond quickly to changing market demands and stay competitive in today’s fast-paced business environment.
The Impact of IIoT on Efficiency and Productivity
Industrial Internet of Things (IIoT) has revolutionized the way businesses operate by significantly enhancing efficiency and productivity in various industrial sectors. Through the utilization of sensors and connectivity, IIoT enables real-time monitoring and control of machines and processes, leading to streamlined operations and reduced downtime. This increased visibility and data-driven insights provided by IIoT systems allow organizations to optimize their production processes and make informed decisions promptly.
Furthermore, by harnessing the power of IIoT, companies can automate repetitive tasks, improve workflow management, and enhance overall productivity. The ability to gather, analyze, and act upon data in real-time empowers businesses to identify inefficiencies, implement preventive maintenance strategies, and boost operational efficiency. Ultimately, the integration of IIoT technologies into industrial automation systems paves the way for improved performance, reduced costs, and increased competitiveness in the ever-evolving market landscape.
How IIoT Enhances Predictive Maintenance
Predictive maintenance has been revolutionized by the implementation of Industrial Internet of Things (IIoT) technologies in industrial settings. IIoT enhances predictive maintenance through the continuous monitoring of equipment and systems in real-time, allowing for the detection of potential issues before they escalate into costly failures. By utilizing sensors and connectivity, IIoT enables predictive maintenance strategies to be more proactive and accurate, leading to increased equipment uptime and reduced maintenance costs.
Moreover, IIoT enhances predictive maintenance by facilitating condition-based monitoring, where equipment health metrics and performance data are constantly collected and analyzed. This real-time monitoring enables maintenance teams to make data-driven decisions about when maintenance or repairs are actually needed, optimizing maintenance schedules and avoiding unnecessary downtime. Additionally, IIoT allows for the integration of historical data, machine learning algorithms, and predictive analytics, further enhancing the accuracy and efficiency of predictive maintenance practices.
IIoT’s Role in Real-Time Data Analysis
Real-time data analysis plays a crucial role in industrial settings, enabling organizations to make informed decisions promptly. IIoT facilitates real-time data collection from various sensors and devices on the factory floor, providing valuable insights into the operational performance of equipment and processes. By analyzing this data in real-time, businesses can quickly identify inefficiencies, predict potential issues, and optimize production workflows for enhanced productivity.
The ability of IIoT to process data in real-time empowers industrial companies to proactively address maintenance needs and avoid costly downtime. By monitoring equipment performance continuously, anomalies and patterns can be detected early, allowing for predictive maintenance strategies to be implemented. This proactive approach not only extends the lifespan of machinery but also reduces unplanned maintenance expenses and improves overall operational efficiency.
• Real-time data analysis is crucial in industrial settings for making informed decisions promptly
• IIoT enables real-time data collection from sensors and devices on the factory floor
• Analyzing this data in real-time helps businesses identify inefficiencies, predict issues, and optimize workflows
• IIoT allows for proactive maintenance by detecting anomalies and patterns early
• Predictive maintenance strategies help extend machinery lifespan, reduce expenses, and improve operational efficiency
The Integration of IIoT with Machine Learning and AI
As industrial automation continues to advance, the integration of IIoT with machine learning and artificial intelligence (AI) is becoming more prevalent. IIoT technologies provide a vast amount of data from various sensors and devices, which can be analyzed and interpreted in real-time through machine learning algorithms. By leveraging AI capabilities, such as pattern recognition and predictive analytics, manufacturers can optimize processes, detect anomalies, and improve overall efficiency.
Machine learning and AI algorithms can help industrial facilities identify patterns and trends within the data collected by IIoT devices. This insight enables proactive decision-making and predictive maintenance strategies, leading to reduced downtime and increased productivity. Additionally, by combining IIoT with machine learning and AI, companies can unlock new opportunities for automation and optimization, ultimately paving the way for smarter and more efficient industrial operations.
IIoT’s Contribution to Safety in Industrial Settings
Industrial Internet of Things (IIoT) plays a crucial role in enhancing safety within industrial settings. By utilizing sensors, connected devices, and real-time data analysis, IIoT enables proactive identification of potential safety hazards. This empowers organizations to implement preventive measures and protocols to mitigate risks and create a safer work environment for employees.
Furthermore, IIoT facilitates the implementation of smart safety systems that can automatically detect unsafe conditions and trigger immediate responses or alerts. This real-time monitoring and control help in averting accidents and minimizing the impact of emergencies in industrial facilities. Overall, the integration of IIoT technologies not only enhances safety standards but also contributes to improving overall operational efficiency and productivity.
The Evolution of IIoT in Supply Chain Management
Supply chain management has always been a crucial aspect of running successful businesses, and the evolution of IIoT has brought about significant changes in how organizations approach this area. The integration of IIoT devices and sensors throughout the supply chain has enabled real-time tracking and monitoring of inventory, shipments, and production processes. This enhanced visibility allows for better decision-making, improved efficiency, and streamlined operations.
Moreover, the data collected through IIoT devices in the supply chain can be leveraged to optimize routes, reduce lead times, and minimize costs. By analyzing this data, companies can identify bottlenecks, anticipate potential disruptions, and proactively address issues before they escalate. As a result, the evolution of IIoT in supply chain management has paved the way for more agile, responsive, and optimized logistical operations, ultimately leading to enhanced customer satisfaction and competitive advantage.
IIoT’s Influence on Decision-Making Processes
The implementation of Industrial Internet of Things (IIoT) technology in industrial settings has significantly influenced decision-making processes. With the influx of real-time data provided by IIoT devices and sensors, managers and decision-makers now have access to a wealth of information to make informed and timely decisions. This data-driven approach allows for quicker identification of issues, proactive problem-solving, and optimization of operational strategies.
Furthermore, the integration of IIoT with advanced analytics tools enables a deeper understanding of trends, patterns, and correlations within the industrial environment. Decision-makers can now leverage this valuable insight to forecast potential outcomes, identify opportunities for improvement, and make data-driven decisions that align with organizational goals. Ultimately, IIoT’s influence on decision-making processes empowers industrial businesses to stay agile, competitive, and responsive to dynamic market conditions.
The Advantages of IIoT in Remote Monitoring and Control
Remote monitoring and control provided by IIoT technology offers numerous advantages for industrial settings. One significant benefit is the ability to oversee operations from anywhere in the world, allowing for real-time monitoring of equipment performance and production processes. This remote accessibility enables quick decision-making and intervention in case of any issues, leading to increased efficiency and minimized downtime.
Moreover, IIoT in remote monitoring and control facilitates predictive maintenance by continuously collecting and analyzing data from equipment and machinery. This proactive approach helps in identifying potential faults or breakdowns before they occur, thereby reducing maintenance costs and prolonging the lifespan of assets. Additionally, remote monitoring allows for remote troubleshooting and adjustments, optimizing operational performance and ensuring smooth production processes.
IIoT’s Effect on Energy Management in Industrial Facilities
Industrial Internet of Things (IIoT) plays a crucial role in enhancing energy management within industrial facilities. By leveraging connected devices and sensors, IIoT enables real-time monitoring and analysis of energy consumption patterns. This valuable data allows companies to identify opportunities for optimizing energy usage, reducing waste, and ultimately lowering operational costs. Additionally, IIoT facilitates the implementation of predictive maintenance strategies that can help prevent equipment failures and minimize energy inefficiencies.
Furthermore, IIoT provides the necessary tools for implementing automated energy management systems that can adjust energy usage based on demand, production schedules, and external factors such as weather conditions. These smart systems enable industrial facilities to operate more efficiently by ensuring that energy is utilized when needed and conserved when not in use. By integrating IIoT into energy management practices, companies can achieve greater sustainability, reduce their carbon footprint, and contribute to a more eco-friendly industrial landscape.
The Future of IIoT in Industrial Automation
The future of IIoT in industrial automation holds immense promise for revolutionizing how businesses operate and optimize their processes. With the advancements in technology and the increasing adoption of IIoT solutions, we can expect to see even greater integration of smart devices, sensors, and data analytics tools in industrial settings. This integration will enable real-time monitoring, predictive maintenance, and enhanced decision-making capabilities, ultimately leading to increased efficiency and productivity across various sectors.
As we look ahead, the evolution of IIoT in industrial automation is likely to pave the way for a more interconnected and intelligent manufacturing ecosystem. The convergence of IIoT with technologies such as artificial intelligence and machine learning will enable autonomous decision-making, predictive analytics, and adaptive control systems. This integration will not only streamline operations but also enhance the overall performance and sustainability of industrial processes, marking a significant shift towards a more efficient and responsive industrial landscape.
Challenges and Opportunities of Implementing IIoT in Manufacturing
Implementing IIoT in manufacturing presents a set of challenges that must be addressed to fully leverage its benefits. One of the key hurdles is the initial investment required for retrofitting existing machinery with IIoT sensors and connectivity. This can be a significant financial commitment for some companies, especially smaller ones with limited resources. Additionally, ensuring the security and privacy of data transmitted and stored through IIoT systems is crucial but can be complex and costly to implement effectively.
On the flip side, there are numerous opportunities that come with the successful integration of IIoT in manufacturing processes. By capturing real-time data and enabling predictive maintenance, companies can reduce downtime, optimize operations, and improve overall efficiency. Furthermore, IIoT opens up possibilities for remote monitoring and control, allowing for more flexibility and agility in responding to production needs. Embracing IIoT in manufacturing presents a pathway to staying competitive in the ever-evolving landscape of Industry 4.0.
IIoT’s Role in Sustainable and Eco-Friendly Practices in Industries
Industrial Internet of Things (IIoT) plays a crucial role in fostering sustainable and eco-friendly practices in industries today. By leveraging IIoT technologies, companies can efficiently monitor and optimize their resource consumption, leading to reduced waste and enhanced environmental stewardship. The real-time data insights provided by IIoT devices enable businesses to make informed decisions that contribute to long-term sustainability goals.
Furthermore, IIoT facilitates enhanced energy management strategies within industrial facilities. Through the utilization of smart sensors and connected devices, organizations can monitor energy usage patterns, identify areas for optimization, and implement energy-saving measures effectively. This not only reduces operational costs but also minimizes the environmental impact of industrial activities, aligning with the growing global emphasis on sustainable business practices.
Additional Resources:
[catlist categorypage=”yes”]
Table of Contents
Categories:
[categories orderby=name]
Latest Posts:
[sbs_latest_posts]
FAQs:
What are some key benefits of IIoT in industrial automation?
IIoT can improve efficiency, productivity, predictive maintenance, real-time data analysis, safety, decision-making processes, supply chain management, remote monitoring and control, and energy management in industrial settings.
How does IIoT enhance predictive maintenance?
IIoT enables sensors to gather real-time data on equipment performance, allowing for predictive maintenance schedules to be implemented based on actual usage and conditions, rather than fixed time intervals.
In what ways does IIoT contribute to safety in industrial settings?
IIoT can monitor equipment performance and environmental conditions in real-time, alerting operators to potential safety hazards or issues before they escalate, helping to prevent accidents and injuries.
How does IIoT impact decision-making processes in industries?
IIoT provides actionable insights and data analytics that can help decision-makers make informed choices, optimize processes, and improve overall efficiency and productivity.
What role does IIoT play in sustainable and eco-friendly practices in industries?
IIoT enables industries to optimize energy management, reduce waste, and improve resource efficiency, leading to more sustainable and environmentally-friendly operations.