Emergence of Automated Guided Vehicles (AGVs) in Smart Factories
Automated Guided Vehicles (AGVs) have emerged as a game-changer in the realm of smart factories. These driverless vehicles are equipped with advanced navigational technologies such as laser guidance systems and magnetic tape to efficiently transport materials within the production facility. The integration of AGVs in smart factories not only enhances operational efficiency but also reduces the risk of human errors, thereby improving overall productivity.
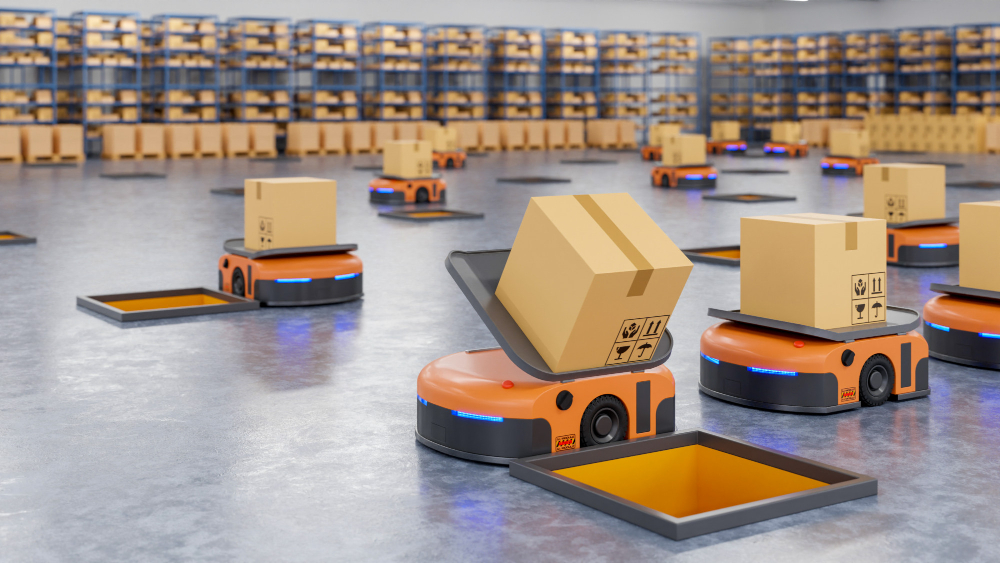
The flexibility and adaptability of AGVs make them indispensable in the modern manufacturing landscape. These autonomous vehicles can be programmed to follow predefined routes or dynamically adjust their paths based on real-time data, ensuring smooth material flow throughout the factory floor. Moreover, the ability of AGVs to collaborate with other smart technologies, such as robotics and IoT devices, paves the way for a more interconnected and agile production environment.
Integration of Robotic Arms in Manufacturing Processes
Robotic arms have become an indispensable component in modern manufacturing processes, revolutionizing the way products are assembled, handled, and processed on the factory floor . These sophisticated machines are equipped with precision controls and advanced sensors, allowing them to perform complex tasks with speed and accuracy. The integration of robotic arms in manufacturing operations has led to significant improvements in production efficiency, quality control, and overall output.
Moreover, the versatility of robotic arms enables them to adapt to a variety of tasks and applications within the manufacturing environment. From repetitive assembly line processes to intricate welding and material handling operations, robotic arms excel in streamlining workflows and enhancing productivity. Their ability to work alongside human operators in a collaborative manner further enhances operational flexibility and efficiency in the manufacturing setting.
Advancements in Vision Systems for Robotics in Smart Factories
Advancements in vision systems play a crucial role in enhancing the capabilities of robotics within smart factories. These systems utilize cameras and sensors to provide robots with the ability to perceive and interpret their surroundings, enabling them to navigate, manipulate objects, and perform tasks with greater precision. The integration of vision systems has led to significant improvements in quality control, as robots can now inspect products with high levels of accuracy, ensuring that only items meeting specified criteria are passed along the production line.
Furthermore, advancements in vision systems have also enabled robots to collaborate more effectively with human workers in factory settings. By incorporating technologies such as object recognition and tracking, robots can identify and adapt to the presence of individuals in their vicinity, ensuring a safer working environment. This enhanced level of interaction between humans and robots not only increases efficiency in manufacturing processes but also opens up new possibilities for more dynamic and flexible production workflows.
Collaborative Robots (Cobots) Revolutionizing Factory Operations
Collaborative robots, also known as cobots, are reshaping the landscape of factory operations by introducing a new era of human-robot collaboration. These advanced robotic systems are designed to work alongside human employees, enhancing efficiency and productivity while ensuring a safe working environment. Unlike traditional industrial robots that often require safety cages and operate in isolation, cobots can perform tasks in close proximity to humans without posing a risk of harm.
The flexibility and adaptability of cobots make them ideal for a wide range of applications in smart factories, from assembly and pick-and-place tasks to quality control and packaging. By seamlessly integrating into existing workflows, cobots facilitate a more agile and responsive production process, allowing manufacturers to quickly adapt to changing market demands. With their intuitive programming interfaces and ability to learn from human input, cobots empower workers to focus on higher-value activities while streamlining repetitive and mundane tasks.
Implementing Artificial Intelligence in Robotics for Increased Efficiency
Artificial Intelligence (AI) is transforming the landscape of robotics in smart factories by enhancing efficiency and productivity. By integrating AI algorithms into robotic systems, machines can analyze vast amounts of data in real-time, enabling them to make intelligent decisions and adapt to dynamic manufacturing environments. These AI-powered robots can optimize production processes, predict maintenance requirements, and improve overall operational efficiency.
Moreover, AI in robotics allows for advanced levels of autonomy and decision-making capabilities. Through machine learning and deep learning technologies, robots can continuously learn from their interactions and experiences, leading to improved performance and increased adaptability in diverse tasks. By harnessing the power of AI, manufacturers can revolutionize their production lines, streamline operations, and achieve higher levels of efficiency in smart factories.
Utilizing Machine Learning for Predictive Maintenance in Robotics
Predictive maintenance in robotics has been revolutionized by the integration of machine learning algorithms. By utilizing historical data and real-time information, these algorithms can predict potential failures in robotic systems before they occur. This proactive approach not only reduces downtime and maintenance costs but also enhances overall operational efficiency in smart factories.
Machine learning algorithms continuously analyze vast amounts of data generated by robotics systems, enabling them to identify patterns and deviations that may indicate impending issues. This predictive capability allows maintenance teams to schedule interventions precisely when needed, minimizing disruptions to production processes. As robotics technology continues to evolve, the application of machine learning for predictive maintenance is poised to play a crucial role in ensuring the seamless operation of smart factories.
Enhancing Safety Measures in Smart Factory Robotics
Ensuring the safety of workers in smart factory robotics is paramount to the success and sustainability of manufacturing operations. With the integration of advanced robotics and automation systems, there is a growing need to implement robust safety measures to prevent accidents and injuries. This includes the installation of sensors and emergency stop mechanisms on robotic equipment to quickly detect and respond to potential hazards in real-time.
Moreover, ongoing training programs and safety protocols must be established to educate workers on the proper procedures for interacting with robotic systems. Emphasizing the importance of following safety guidelines and using personal protective equipment can significantly reduce the risk of incidents in smart factory environments. By fostering a culture of safety and vigilance, organizations can create a secure working environment that promotes productivity and efficiency in the operation of robotics within smart factories.
• Implement sensors and emergency stop mechanisms on robotic equipment
• Establish ongoing training programs for workers
• Emphasize the importance of following safety guidelines
• Use personal protective equipment to reduce risk of incidents
• Foster a culture of safety and vigilance in smart factory environments
By adhering to these safety measures, organizations can not only protect their workers from harm but also improve overall operational efficiency and productivity in smart factory robotics. Prioritizing safety is essential for the long-term success and sustainability of manufacturing operations utilizing advanced automation systems. With proper precautions in place, companies can create a work environment that maximizes the benefits of robotics while minimizing potential risks to employees.
Incorporating Internet of Things (IoT) in Robotics for Data Analytics
The integration of Internet of Things (IoT) technology in robotics is revolutionizing data analytics in smart factories. By connecting robotic systems to the internet, manufacturers can collect real-time data on machine performance, production output, and maintenance needs. This data can then be analyzed to optimize operational efficiency, predict maintenance requirements, and identify areas for improvement within the manufacturing process.
IoT-enabled robotics also facilitate remote monitoring and control, allowing for increased flexibility and responsiveness in factory operations. Through sensors and connectivity, robots can communicate their statuses and receive commands from centralized control systems, leading to enhanced coordination and streamlined workflow. Furthermore, the use of IoT in robotics opens up possibilities for predictive analytics, enabling proactive decision-making and preventing downtime by addressing issues before they escalate.
Role of Virtual Reality (VR) in Training Robotics for Smart Factories
Incorporating virtual reality (VR) in the training of robotics for smart factories provides an immersive and interactive learning experience for operators and technicians. By simulating real-world scenarios within a virtual environment, trainees can practice handling various robotic systems, troubleshoot potential issues, and optimize operational processes. This hands-on approach helps to enhance their skills and confidence, leading to improved efficiency and productivity in the factory setting.
Furthermore, VR training enables individuals to familiarize themselves with different types of robotic equipment and programming interfaces without the need for physical access to actual machinery. This not only saves time and resources but also reduces the risk of accidents during the learning process. Additionally, by utilizing VR simulations, trainees can adapt to new robotics technologies and advancements quickly, ensuring that they stay up-to-date with the latest developments in the field.
Adoption of 3D Printing Technology in Robotic Manufacturing
3D printing technology has been making significant strides in revolutionizing the manufacturing industry, and its integration with robotic systems is reshaping the way products are being fabricated. By utilizing 3D printing technology in robotic manufacturing processes, companies can achieve greater flexibility and customization in their production lines. This innovative approach allows for rapid prototyping, on-demand manufacturing, and the ability to create intricate designs that were previously challenging to produce through traditional manufacturing methods.
Furthermore, the adoption of 3D printing technology in robotic manufacturing is driving advancements in automation and efficiency. Robotic systems equipped with 3D printing capabilities can work tirelessly to produce complex components with precision and speed, ultimately reducing production time and costs. This integration also opens up new opportunities for producing lightweight and durable parts, optimizing supply chains, and streamlining the overall manufacturing workflow in smart factories.
Challenges and Solutions in Implementing Swarm Robotics in Factories
Implementing swarm robotics in factories presents a unique set of challenges that require innovative solutions. One major challenge is coordinating the movements of multiple robots to work collectively towards a common goal without collisions or inefficiencies. This requires sophisticated algorithms and communication protocols to ensure seamless coordination among the swarm members. Additionally, ensuring robustness in swarm robotics systems to handle unexpected disturbances or failures is crucial for maintaining uninterrupted operations in a factory setting.
To address these challenges, researchers and developers are exploring advanced techniques such as artificial intelligence and machine learning to enhance the autonomy and decision-making capabilities of swarm robotics systems. By equipping robots with adaptive learning algorithms, they can better adapt to changing environments and optimize their collaborative behaviors. Moreover, incorporating sensor fusion technologies and real-time data processing can improve the overall situational awareness of the swarm, enabling them to react swiftly to dynamic conditions in the factory floor. Overall, overcoming the challenges in implementing swarm robotics will pave the way for more efficient and flexible manufacturing processes in smart factories.
Future Prospects of Robotics in Smart Factories
With the rapid advancements in technology, the future prospects of robotics in smart factories are promising. One of the key areas of development is the integration of artificial intelligence to enhance the decision-making capabilities of robots. By implementing AI algorithms, robots can adapt to changing conditions in real-time, improving efficiency and productivity in manufacturing processes. Additionally, the use of machine learning for predictive maintenance can help prevent potential breakdowns and reduce downtime, leading to cost savings for companies.
Another exciting prospect is the incorporation of the Internet of Things (IoT) in robotics for data analytics. By connecting robots to a network of sensors and devices, manufacturers can gather valuable insights into their operations and make informed decisions to optimize performance. This integration of IoT not only enables real-time monitoring but also opens up possibilities for remote operation and control of robotic systems, revolutionizing the way factories are run.
Impact of Robotics on the Future of Manufacturing Industry
As robotics technology continues to evolve and expand within the manufacturing industry, the future holds a myriad of transformative possibilities. With the integration of advanced robotics systems, factories can expect to see significant improvements in efficiency, productivity, and quality control. Tasks that once required manual labor can now be automated with precision and speed, resulting in streamlined operations and reduced costs.
Furthermore, the future of manufacturing industry will be marked by enhanced flexibility and adaptability, thanks to the advancements in robotics. Robots are increasingly being designed to work alongside human operators in collaborative environments, opening up new avenues for creativity and innovation. As robotics technology continues to mature, we can anticipate a shift towards more agile and responsive manufacturing processes that can quickly adapt to changing market demands and technological trends.
Additional Resource:
[catlist categorypage=”yes”]
Table of Contents
Categories:
[categories orderby=name]
Latest Posts:
[sbs_latest_posts]
FAQs:
What are some current trends in the robotics industry that are impacting the future of manufacturing?
Some current trends include the emergence of AGVs, integration of robotic arms, advancements in vision systems, the use of collaborative robots, implementing artificial intelligence and machine learning, enhancing safety measures, incorporating IoT, utilizing VR for training, adopting 3D printing, and exploring swarm robotics.
How are Automated Guided Vehicles (AGVs) changing the landscape of smart factories?
AGVs are revolutionizing smart factories by autonomously transporting materials and goods, increasing efficiency, reducing human error, and enhancing overall productivity.
What role do Collaborative Robots (Cobots) play in factory operations?
Cobots work alongside human workers in a shared workspace, increasing flexibility, improving safety, and optimizing production processes in factories.
How is Artificial Intelligence being implemented in robotics for increased efficiency?
AI algorithms are being used to optimize robotic tasks, predict maintenance needs, analyze data, and make real-time decisions to enhance efficiency in manufacturing operations.
What is the significance of incorporating Internet of Things (IoT) in robotics for data analytics?
IoT technology allows robotics to collect and share data in real-time, enabling predictive maintenance, remote monitoring, and data-driven decision-making in smart factories.
How can Virtual Reality (VR) be used for training robotics in smart factories?
VR simulations provide immersive training experiences for operators and engineers, allowing them to practice tasks, troubleshoot issues, and improve their skills in a virtual environment.
What are some challenges and solutions in implementing Swarm Robotics in factories?
Challenges include coordination among multiple robots and scalability issues. Solutions involve developing communication protocols, optimizing algorithms, and integrating swarm robotics with existing systems for efficient collaboration.
What are the future prospects of robotics in smart factories?
The future of robotics in smart factories includes increased automation, improved efficiency, enhanced safety measures, and the integration of advanced technologies such as AI, IoT, and VR to drive innovation and productivity in manufacturing industries.