Challenges Faced in Implementing Smart Factory Solutions
Implementing smart factory solutions can pose several challenges for organizations aiming to embrace digital transformation. One common hurdle is the significant initial investment required to upgrade existing manufacturing processes with advanced technologies. This financial commitment can deter some companies from taking the leap towards a smart factory setup, despite the long-term benefits it promises in terms of efficiency and productivity.
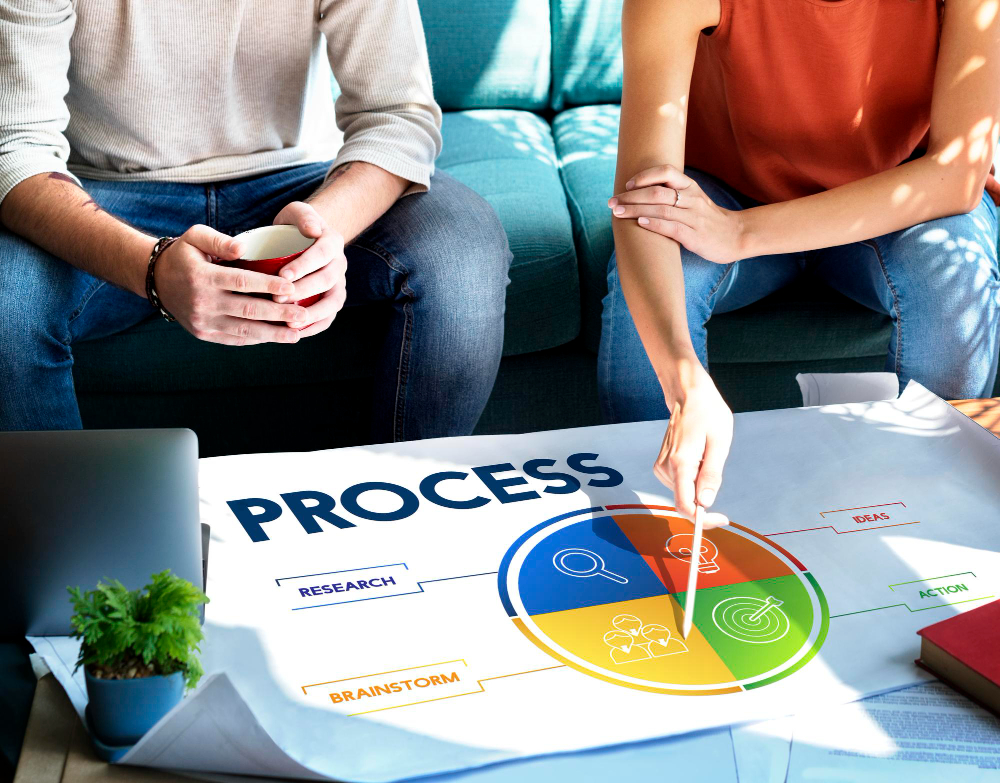
Another prevalent challenge is the resistance to change from employees accustomed to traditional manufacturing methods. Introducing automation and IoT devices into the production line may lead to concerns about job security or fears of being replaced by machines. Overcoming this resistance and ensuring proper training and upskilling of staff are crucial steps in the successful implementation of smart factory solutions.
Benefits of Adopting Smart Factory Technologies
Smart factory technologies offer a myriad of benefits to manufacturing companies. One of the key advantages is the significant improvement in operational efficiency through automation and real-time data analysis. By streamlining production processes and minimizing downtime, smart factories can enhance productivity and ultimately result in cost savings for the business. Additionally, the implementation of these technologies enables better resource utilization, leading to optimized performance across all facets of the manufacturing operation.
Furthermore, smart factory solutions play a crucial role in enhancing the overall quality control measures within a manufacturing setting. By leveraging advanced technologies such as IoT and data analytics, companies can proactively identify and address potential issues in the production line, ensuring a higher standard of quality in the manufactured products. This not only leads to increased customer satisfaction but also helps in building a strong reputation for the company in the market.
Successful Integration of IoT in Manufacturing Processes
The integration of IoT in manufacturing processes has revolutionized the way industries operate, providing real-time insights and data that enable better decision-making. By connecting machines, devices, and sensors, manufacturers can monitor, analyze, and optimize their production lines with unprecedented levels of precision and efficiency. This seamless integration allows for predictive maintenance, reducing downtime, and improving overall equipment effectiveness.
Furthermore, IoT integration facilitates the automation of tasks that were once manual, leading to increased productivity and cost savings for manufacturers. The ability to remotely monitor and control production processes ensures that efficiency is maximized, and resources are utilized effectively. With IoT-enabled devices communicating with each other to streamline operations, manufacturers can achieve higher levels of output while maintaining quality standards.
Improving Efficiency with Automation in Smart Factories
Automation plays a vital role in enhancing efficiency within smart factories. By integrating automated systems into manufacturing processes, companies can streamline operations, reduce human error, and increase productivity. Machines can perform repetitive tasks with precision and consistency, leading to faster production cycles and ultimately driving efficiency gains. Additionally, automation enables real-time monitoring and control of various operations, allowing for quick adjustments to optimize performance and minimize downtime.
The implementation of automation in smart factories also brings about cost savings by reducing labor costs and enhancing resource utilization. With automated systems taking over manual tasks, employees can focus on more strategic and higher-value activities, such as problem-solving and innovation. This shift in workforce dynamics not only improves efficiency but also fosters a culture of continuous improvement within the organization, driving long-term success and competitiveness in the market.
• Automation streamlines operations and reduces human error
• Machines perform repetitive tasks with precision, leading to faster production cycles
• Real-time monitoring and control allow for quick adjustments to optimize performance
• Automation in smart factories reduces labor costs and enhances resource utilization
• Employees can focus on strategic activities like problem-solving and innovation
• Fosters a culture of continuous improvement within the organization
Enhancing Quality Control through Smart Factory Implementations
In the realm of manufacturing, quality control stands as a paramount aspect that directly impacts product excellence and customer satisfaction. Smart factory implementations have revolutionized traditional quality control methods by enabling real-time monitoring and data analysis throughout the production process. Through the integration of IoT devices and advanced sensors, manufacturers can gain valuable insights into product quality at various stages, thus facilitating proactive measures to address any potential defects before they escalate.
The seamless communication and interconnectedness of machines within a smart factory ecosystem play a pivotal role in enhancing quality control efforts. By harnessing the power of automation and AI-driven algorithms, manufacturers can identify deviations from established quality standards with precision and speed. This proactive approach not only minimizes the risk of defective products reaching the market but also empowers companies to continuously refine their quality control strategies for improved efficiency and consistency.
Case Study: How Company A Increased Productivity with Smart Factory Solutions
Company A, a leading manufacturer in the automotive industry, embraced smart factory solutions to enhance productivity and efficiency in their production process. By integrating IoT devices and automation technologies, they were able to streamline their operations and reduce manual errors. The implementation of real-time data analytics provided Company A with valuable insights into their manufacturing processes, allowing them to make data-driven decisions and optimize their workflow.
As a result of their smart factory initiatives, Company A experienced a significant increase in productivity and cost savings. By leveraging predictive maintenance techniques, they were able to minimize downtime and extend the lifespan of their equipment. This proactive approach to maintenance not only improved operational efficiency but also ensured the quality and consistency of their products. Company A’s successful adoption of smart factory solutions serves as a testament to the transformative power of technology in revolutionizing traditional manufacturing practices.
Optimizing Supply Chain Management with Smart Factory Technologies
Smart factory technologies are revolutionizing supply chain management by providing real-time visibility and transparency across the entire production process. By integrating IoT devices and data analytics tools, companies can track inventory levels, monitor production status, and anticipate potential disruptions in the supply chain. This enhanced visibility enables better decision-making, improves efficiency, and reduces costs associated with excess inventory or delays in production.
Additionally, smart factory technologies facilitate seamless communication and collaboration between different stakeholders in the supply chain. Through automated data sharing and communication channels, suppliers, manufacturers, and distributors can coordinate their activities more effectively, leading to streamlined operations and quicker response times to changing market demands. This interconnected ecosystem helps optimize supply chain management processes, from procurement to distribution, ultimately enhancing overall business performance and customer satisfaction.
Real-Time Data Analytics in Smart Factories: A Case Study
Real-time data analytics has revolutionized the way smart factories operate, allowing companies to make informed decisions promptly. An intriguing case study highlights Company B’s implementation of real-time data analytics to optimize their production processes. By harnessing data from various sensors and machines on the production line, Company B successfully identified bottlenecks and inefficiencies in real time, enabling them to take immediate corrective actions and improve overall productivity. The integration of real-time data analytics not only streamlined operations but also enhanced the quality of their products through precise monitoring and control.
Moreover, the case study demonstrates how real-time data analytics in smart factories can improve resource utilization and reduce downtime significantly. By analyzing live data on machine performance and production output, Company B was able to predict maintenance needs and schedule preventive measures effectively, thus minimizing unplanned downtime. This proactive approach to maintenance not only saved costs associated with emergency repairs but also increased the lifespan of their equipment, ultimately leading to higher operational efficiency and greater profitability.
Maximizing ROI with Smart Factory Investments
Smart factory investments have gained traction in the manufacturing industry, offering companies the opportunity to improve productivity, reduce costs, and enhance competitiveness. By leveraging advanced technologies such as IoT, automation, and data analytics, organizations can optimize their operations and achieve a higher return on investment. These innovations enable real-time monitoring of production processes, predictive maintenance, and improved decision-making based on actionable insights.
To maximize ROI with smart factory investments, companies need to strategically plan and implement these technologies across their manufacturing facilities. This involves assessing current operational inefficiencies, identifying key areas for improvement, and setting measurable goals to track the impact of smart factory solutions on performance. By aligning technology deployment with business objectives and continuously evaluating and adjusting strategies, organizations can unlock the full potential of smart manufacturing and drive sustainable growth.
Overcoming Resistance to Change in Implementing Smart Factory Solutions
When implementing smart factory solutions, resistance to change from employees can be a significant obstacle. This resistance often stems from fear of the unknown, concerns about job security, and a reluctance to embrace new technologies. To overcome this resistance, it is important for management to communicate effectively with employees, highlighting the benefits of smart factory technologies such as increased efficiency, improved quality control, and new opportunities for growth and development.
Furthermore, involving employees in the decision-making process and providing adequate training and support can help alleviate fears and build trust in the new system. By addressing concerns head-on and creating a culture of openness and collaboration, companies can pave the way for a successful implementation of smart factory solutions.
Case Study: Implementing Predictive Maintenance in a Smart Factory Setting
Implementing predictive maintenance in a smart factory setting can revolutionize the way machinery upkeep is managed. Company X, a leading automotive manufacturer, embarked on this journey to enhance operational efficiency and minimize downtime. By leveraging IoT sensors and data analytics, they were able to predict potential equipment failures before they occurred, allowing for proactive maintenance interventions and eliminating unexpected disruptions in the production line.
As a result of this predictive maintenance strategy, Company X experienced a notable decrease in unscheduled downtime, leading to significant cost savings and improved productivity. The real-time monitoring of equipment health enabled the maintenance team to schedule repairs during planned maintenance windows, optimizing the overall efficiency of the factory floor. Additionally, the implementation of predictive maintenance boosted employee morale as workers were no longer caught off guard by sudden breakdowns, fostering a more productive and positive work environment.
Creating a Connected Ecosystem in Smart Factories
Leveraging connected ecosystems in smart factories is crucial for streamlined operations and seamless data flow. By integrating various devices, machines, and systems into a unified network, manufacturers can enhance communication, monitor processes in real-time, and make data-driven decisions swiftly. This interconnected environment fosters collaboration among different components of the factory, leading to improved efficiency and productivity.
Moreover, a connected ecosystem in smart factories enables predictive maintenance and proactive management of equipment. Through continuous monitoring and analysis of data from sensors and machines, potential issues can be identified and addressed before they escalate, reducing downtime and enhancing overall equipment effectiveness. This predictive approach not only extends the lifespan of machinery but also minimizes unexpected failures, enabling manufacturers to uphold production schedules and meet customer demands effectively.
Future Trends in Smart Factory Implementations
Smart factory implementations are continuously evolving to keep pace with technological advancements and changing business landscapes. One of the future trends in smart factories is the utilization of 5G technology to enhance communication and connectivity within manufacturing processes. The high-speed, low-latency capabilities of 5G networks will enable real-time data transmission, facilitating quick decision-making and optimizing production efficiency.
Another emerging trend is the integration of Artificial Intelligence (AI) and Machine Learning algorithms in smart factories. These technologies will enable predictive maintenance, quality control, and production optimization through data analysis and pattern recognition. By harnessing the power of AI, smart factories can proactively identify maintenance needs, prevent equipment failures, and streamline operations for increased productivity.
Additional Resources:
[catlist categorypage=”yes”]
Table of Contents
Categories:
[categories orderby=name]
Latest Posts:
[sbs_latest_posts]
FAQs:
What are some challenges faced in implementing smart factory solutions?
Some common challenges include high initial investment costs, integration issues with existing systems, and resistance to change from employees.
What are the benefits of adopting smart factory technologies?
Some benefits include increased efficiency, improved quality control, reduced downtime, enhanced flexibility, and better decision-making capabilities.
How can IoT be successfully integrated into manufacturing processes?
IoT can be successfully integrated by connecting devices and machines to a central system, collecting and analyzing data in real-time, and using insights to optimize processes.
How can automation improve efficiency in smart factories?
Automation can improve efficiency by streamlining repetitive tasks, reducing errors, increasing productivity, and enabling faster response times to changes in demand.
How can smart factory implementations enhance quality control?
Smart factory solutions can enhance quality control by enabling real-time monitoring of production processes, detecting defects early, and ensuring consistency in product quality.
How can companies increase productivity with smart factory solutions?
Companies can increase productivity by optimizing workflows, reducing waste, minimizing downtime, and empowering employees with real-time data and insights.
What role do smart factory technologies play in optimizing supply chain management?
Smart factory technologies can optimize supply chain management by providing visibility into production processes, improving inventory management, and enhancing coordination with suppliers.
How can real-time data analytics be utilized in smart factories?
Real-time data analytics can be used to monitor performance metrics, identify trends and patterns, predict maintenance needs, and make data-driven decisions to improve efficiency.
How can companies maximize ROI with smart factory investments?
Companies can maximize ROI by setting clear goals, measuring performance metrics, continuously optimizing processes, and fostering a culture of innovation and continuous improvement.
How can resistance to change be overcome in implementing smart factory solutions?
Resistance to change can be overcome by involving employees in the decision-making process, providing training and support, communicating the benefits of the changes, and recognizing and rewarding success.
How can predictive maintenance be implemented in a smart factory setting?
Predictive maintenance can be implemented by using sensors to monitor equipment health, analyzing data to predict potential failures, scheduling maintenance proactively, and minimizing downtime.
What is the importance of creating a connected ecosystem in smart factories?
Creating a connected ecosystem is important for enabling seamless communication between devices, systems, and processes, optimizing data flow, and facilitating collaboration for better decision-making.
What are some future trends in smart factory implementations?
Future trends may include the adoption of AI and machine learning, the use of digital twins for simulation and optimization, the integration of blockchain for secure data sharing, and the expansion of smart factory concepts to other industries.