Challenges of Implementing Human-Machine Collaboration
Implementing human-machine collaboration in manufacturing processes poses several challenges that need to be addressed. One of the primary hurdles is the resistance from workers who may fear losing their jobs to advanced machines. This fear of displacement can lead to a lack of cooperation and hinder the smooth integration of human-machine teams on the factory floor.
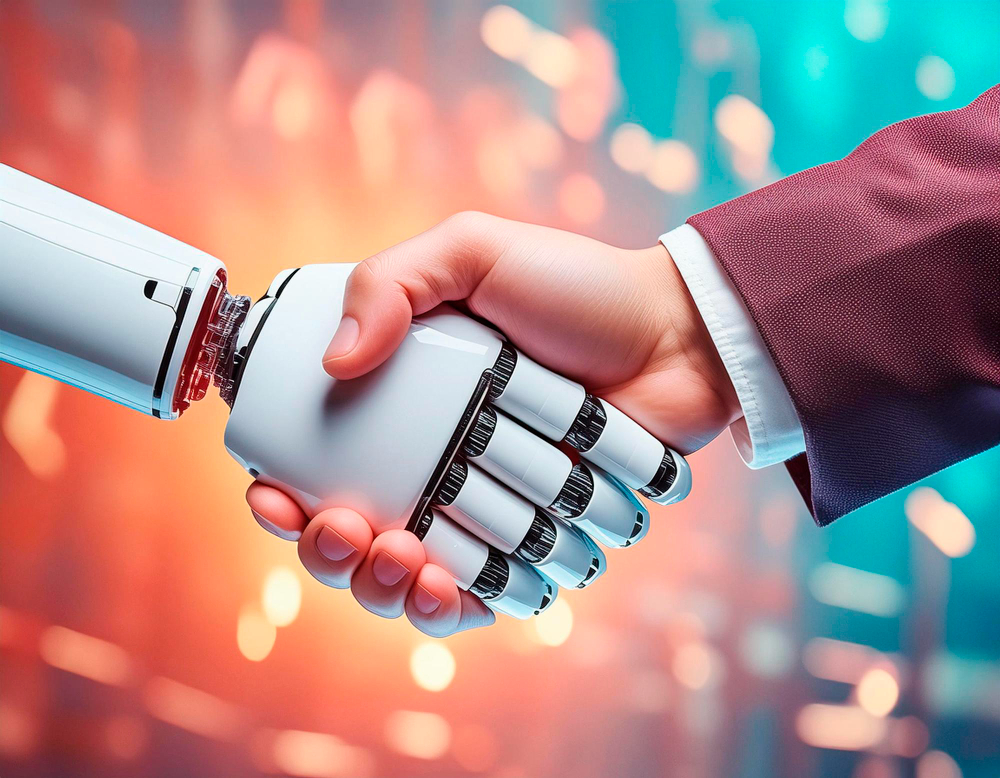
Additionally, another challenge is the need for extensive training programs to upskill workers and help them adapt to working alongside machines. This can be time-consuming and costly for companies, especially for those with a large workforce. Ensuring that employees are equipped with the necessary skills to effectively collaborate with machines is crucial for the successful implementation of human-machine partnerships in smart factories.
Benefits of Integrating Humans and Machines in Smart Factories
Integrating humans and machines in smart factories brings numerous advantages to the manufacturing industry. By leveraging the unique strengths of both humans and machines, smart factories can achieve higher levels of productivity and efficiency. Humans can provide creativity, critical thinking, and problem-solving skills, while machines offer precision, speed, and scalability. Together, they form a powerful partnership that can drive innovation and competitiveness in the market.
Moreover, the collaboration between humans and machines in smart factories leads to improved safety and reduced risks for workers. Machines can handle repetitive and hazardous tasks, allowing humans to focus on more complex and strategic activities. This not only enhances the overall well-being of workers but also ensures a safer working environment. Additionally, integrating humans and machines can lead to cost savings, as the combined efforts of both can streamline production processes and minimize errors.
Role of Artificial Intelligence in Enhancing Collaboration
Artificial Intelligence (AI) is playing a pivotal role in transforming the landscape of human-machine collaboration within smart factories. By harnessing the power of AI algorithms, machines are becoming increasingly adept at learning from human interactions and adapting to dynamic manufacturing environments. Through predictive analytics and machine learning capabilities, AI can enhance collaboration by enabling machines to anticipate human needs and preferences, leading to more seamless and efficient workflows.
Moreover, AI is revolutionizing the way machines interact with humans by enabling natural language processing and speech recognition capabilities. This allows for more intuitive communication between humans and machines, facilitating real-time decision-making and problem-solving. With AI algorithms continuously learning and improving their performance based on feedback from human operators, the potential for enhancing collaboration in smart factories is vast.
The Impact of Robotics on Manufacturing Processes
Robotics has revolutionized manufacturing processes by introducing automation and precision into various production tasks. Robots are capable of handling repetitive and labor-intensive jobs with unparalleled speed and accuracy, leading to increased efficiency in manufacturing operations. By taking over mundane tasks, robots free up human workers to focus on more complex and strategic aspects of production, ultimately enhancing overall productivity in the manufacturing industry.
Furthermore, the integration of robotics in manufacturing processes has resulted in improved quality control and reduced error rates. Robots can consistently perform tasks with precision, minimizing the risk of human error and ensuring the uniformity of finished products. This enhanced quality assurance not only boosts customer satisfaction but also helps manufacturers save costs associated with product defects and rework. As a result, robotics have become indispensable in modern manufacturing facilities striving for excellence in both production efficiency and product quality.
How IoT Devices Facilitate Communication Between Humans and Machines
IoT devices play a crucial role in enabling seamless communication between humans and machines in smart factory environments. These devices serve as intelligent intermediaries, allowing real-time data exchange and coordination between various components of the manufacturing process. By leveraging IoT technology, human operators can remotely monitor and control machines, track production statuses, and receive notifications about potential issues or maintenance requirements.
Furthermore, IoT devices facilitate the integration of predictive maintenance strategies, enabling machines to proactively alert operators about potential malfunctions or breakdowns based on data analytics and machine learning algorithms. This predictive capability not only reduces downtime and maintenance costs but also enhances overall operational efficiency by ensuring that machines are functioning at optimal levels. In essence, IoT devices bridge the gap between humans and machines by providing a constant flow of data and insights, ultimately improving collaboration and productivity within smart factory settings.
Improving Efficiency Through Collaborative Automation
In smart factories, collaborative automation plays a crucial role in enhancing efficiency by seamlessly integrating human operators with robotic systems. By automating repetitive and labor-intensive tasks, workers can focus on more complex and strategic responsibilities, leading to increased productivity and improved quality in manufacturing processes. This collaborative approach allows human workers to leverage the precision and speed of machines, resulting in a more streamlined and efficient workflow.
Moreover, collaborative automation enables real-time data sharing between humans and machines, facilitating quick decision-making and adaptive responses to changing production demands. Through the interconnected network of devices and systems, information flows seamlessly, enabling a synchronized operation that minimizes downtime and maximizes overall output in smart factory environments. This interconnectedness and collaboration between humans and machines not only improve efficiency but also lay the foundation for advanced manufacturing practices in the industry.
Addressing Security Concerns in Human-Machine Partnerships
Security concerns in human-machine partnerships within smart factories have become a focal point of discussion in the manufacturing industry. With the increasing connectivity between humans and machines, there is a growing apprehension regarding data breaches, malicious attacks, and system vulnerabilities that could compromise the integrity of the collaborative processes. As such, it is imperative for organizations to prioritize cybersecurity measures to safeguard their operations and sensitive information from potential threats.
One of the key strategies for addressing security concerns in human-machine partnerships is the implementation of robust authentication protocols and access controls. By requiring multi-factor authentication, strong passwords, and restricted access to critical systems, manufacturers can significantly reduce the risk of unauthorized access and data breaches. Additionally, regular security audits, vulnerability assessments, and employee training programs can help enhance awareness and compliance with security protocols, ensuring a more resilient and secure human-machine collaboration environment.
Training Programs for Workers to Adapt to Smart Factory Environments
Training programs for workers to adapt to smart factory environments play a crucial role in the successful implementation of advanced technologies in manufacturing settings. These programs aim to equip employees with the necessary skills and knowledge to operate and interact with automated systems effectively. By providing hands-on training and guidance, workers can overcome initial uncertainties and embrace the technological changes in the workplace.
Moreover, training programs also focus on fostering a culture of continuous learning and innovation among employees. By staying abreast of the latest advancements in technology and automation, workers can enhance their adaptability and problem-solving abilities in a rapidly evolving industrial landscape. Through targeted training initiatives, organizations can empower their workforce to leverage the full potential of smart factory environments, driving productivity and efficiency across the manufacturing process.
The Role of Data Analytics in Optimizing Human-Machine Collaboration
Data analytics plays a crucial role in enhancing the collaboration between humans and machines in smart factories. By utilizing advanced algorithms to analyze vast amounts of data generated by machines and human input, organizations can gain valuable insights to optimize processes, identify areas for improvement, and make informed decisions in real-time. Through data analytics, smart factories can achieve higher efficiency, reduced downtime, and improved overall performance, leading to cost savings and increased productivity.
Furthermore, data analytics enable predictive maintenance capabilities, allowing machines to anticipate maintenance needs based on historical data and performance indicators. This proactive approach helps prevent unexpected breakdowns, extends equipment lifespan, and ensures seamless operations. By harnessing the power of data analytics, organizations can fine-tune human-machine collaboration to achieve optimal outcomes and drive innovation in manufacturing processes.
• Data analytics enhances collaboration between humans and machines in smart factories
• Advanced algorithms analyze vast amounts of data to optimize processes and make informed decisions
• Smart factories achieve higher efficiency, reduced downtime, and improved performance through data analytics
• Predictive maintenance capabilities prevent unexpected breakdowns and extend equipment lifespan
• Data analytics fine-tunes human-machine collaboration for optimal outcomes and innovation in manufacturing processes
Creating a Seamless Workflow Between Humans and Machines
Achieving a seamless workflow between humans and machines is imperative for optimizing productivity in smart factories. By integrating advanced technologies and automation systems, manufacturing processes can be streamlined to ensure smooth operations. This seamless collaboration between humans and machines not only enhances efficiency but also minimizes errors and delays in production cycles.
In order to create a harmonious workflow, it is essential to establish clear communication channels between humans and machines. This can be facilitated through the implementation of IoT devices and real-time monitoring systems that enable effective data exchange and feedback mechanisms. With proper synchronization and coordination between human operators and machines, tasks can be efficiently allocated and executed to achieve maximum output in a smart factory setting.
Innovations in Human-Machine Interfaces
Human-machine interfaces (HMIs) have evolved significantly in recent years, moving beyond traditional control panels to more intuitive and interactive systems. One notable innovation is the integration of touchscreens and gesture recognition technology, allowing operators to interact with machines in a more natural and seamless manner. These advanced interfaces enable real-time feedback and visualization of data, empowering workers to make informed decisions quickly and efficiently on the factory floor.
Another emerging trend in HMIs is the use of virtual and augmented reality to enhance the interaction between humans and machines. By providing immersive experiences and simulations, these technologies enable operators to access information and perform tasks in a more engaging and dynamic way. This not only improves efficiency and accuracy but also enhances the overall user experience, contributing to a more productive and collaborative work environment.
Ethical Considerations in Smart Factory Operations
When it comes to smart factory operations, ethical considerations play a crucial role in ensuring that the integration of humans and machines is done responsibly. One of the key ethical dilemmas faced in this context is the potential impact on the workforce. As automation takes over some tasks traditionally performed by humans, there is a concern about job displacement and the need to upskill workers to adapt to the changing work environment.
Another ethical consideration is related to data privacy and security. With the extensive use of sensors, IoT devices, and data analytics in smart factories, there is a wealth of information being collected about both machines and human workers. It is essential to establish clear guidelines on how this data is collected, stored, and used to prevent any misuse or violations of privacy rights. Transparency and accountability are essential principles to uphold in order to maintain trust among all stakeholders involved in the human-machine collaboration within smart factories.
Future Trends in Human-Machine Collaboration in Manufacturing Industries
As technology continues to advance at a rapid pace, the future of human-machine collaboration in manufacturing industries looks promising. One of the key trends we can expect to see is the widespread adoption of collaborative robots, known as cobots, that can work alongside human workers to enhance productivity and efficiency on the factory floor. These cobots are designed to be safe and intuitive to use, making them valuable assets in various manufacturing processes.
Another trend on the horizon is the integration of augmented reality (AR) and virtual reality (VR) technologies into manufacturing operations. By incorporating AR and VR tools, workers can receive real-time information, instructions, and visual aids that can improve accuracy and decision-making processes. Furthermore, these technologies can provide immersive training experiences for employees, ensuring they are well-equipped to handle complex tasks in smart factory environments.
Additional Resources:
[catlist categorypage=”yes”]
Table of Contents
Categories:
[categories orderby=name]
Latest Posts:
[sbs_latest_posts]
FAQs:
What are some of the challenges of implementing human-machine collaboration in manufacturing industries?
Some challenges include resistance from workers, integration of new technologies with existing systems, and cybersecurity risks.
What are the benefits of integrating humans and machines in smart factories?
Benefits include increased productivity, improved safety, enhanced decision-making, and the ability to handle complex tasks more efficiently.
How does artificial intelligence enhance collaboration between humans and machines in manufacturing?
AI can automate repetitive tasks, analyze data to make predictions, and improve communication between humans and machines.
What is the impact of robotics on manufacturing processes?
Robotics can increase efficiency, accuracy, and speed in manufacturing processes, leading to cost savings and improved quality.
How do IoT devices facilitate communication between humans and machines in smart factories?
IoT devices can collect and share real-time data, enabling seamless communication and coordination between humans and machines.
How can collaborative automation improve efficiency in manufacturing industries?
Collaborative automation allows humans and machines to work together in a coordinated manner, leading to increased efficiency and productivity.
What security concerns should be addressed in human-machine partnerships?
Security concerns include data breaches, hacking of automated systems, and unauthorized access to sensitive information.
Are there training programs available for workers to adapt to smart factory environments?
Yes, there are training programs that help workers develop the skills needed to operate and maintain advanced technologies in smart factories.
How does data analytics optimize human-machine collaboration in manufacturing industries?
Data analytics can analyze large volumes of data to identify patterns, trends, and insights that can be used to improve collaboration between humans and machines.
What innovations are being made in human-machine interfaces in manufacturing industries?
Innovations include wearable technology, augmented reality, and voice-activated devices that make it easier for humans to interact with machines in a smart factory environment.
What ethical considerations should be taken into account in smart factory operations?
Ethical considerations include job displacement, worker safety, data privacy, and the impact of automation on society.
What are some future trends in human-machine collaboration in manufacturing industries?
Future trends include the use of autonomous robots, predictive maintenance, digital twins, and the integration of AI and machine learning in manufacturing processes.