The Growing Importance of Real-Time Insights in Manufacturing
In today’s fast-paced manufacturing landscape, the ability to access real-time insights has become increasingly crucial for businesses looking to stay competitive and agile in the market. Real-time data allows manufacturing companies to make informed decisions quickly, based on up-to-the-minute information about their operations, supply chain, and customer demands. This immediate access to key metrics and performance indicators empowers organizations to respond promptly to any fluctuations or issues that may arise, enabling them to optimize processes and enhance overall efficiency.
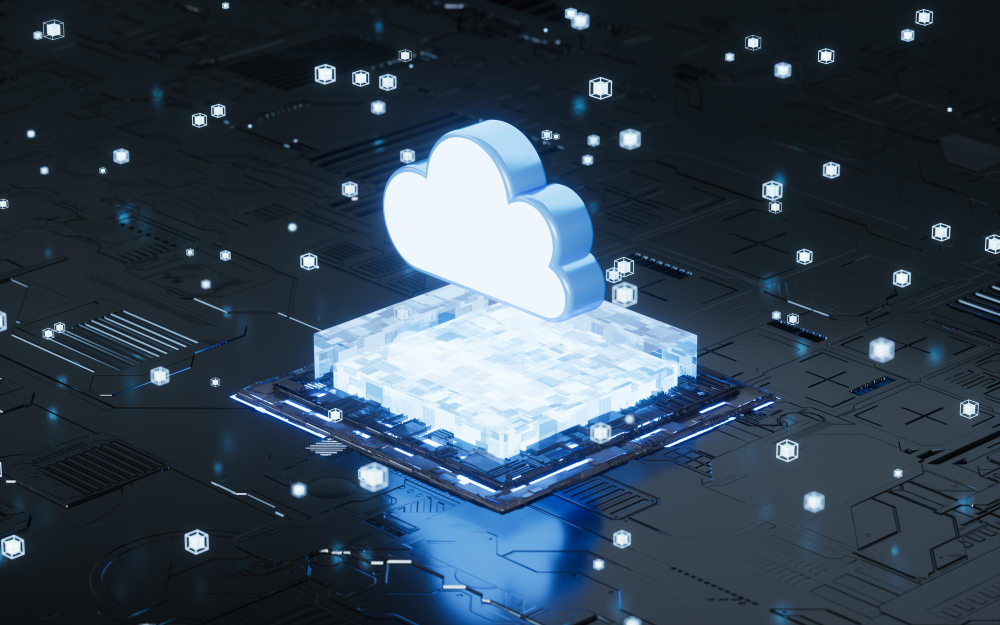
Moreover, real-time insights play a vital role in improving decision-making processes at all levels of a manufacturing enterprise. By utilizing real-time data, manufacturers can identify patterns, trends, and anomalies as they occur, allowing for proactive adjustments and strategic planning. With the rapid advancements in technology and data processing capabilities, harnessing real-time insights has become not just a competitive advantage, but a necessity for manufacturing companies looking to thrive in an increasingly dynamic and demanding market environment.
Challenges Faced by Traditional Data Processing Methods
Traditional data processing methods in manufacturing face significant challenges in keeping pace with the increasing demand for real-time insights. In the past, data collection and analysis were often performed in batches, leading to delays in decision-making and potential disruptions in production. This lag in processing data hinders the ability of manufacturers to quickly respond to changing conditions on the factory floor, impacting operational efficiency and overall productivity.
Moreover, the sheer volume of data generated by modern manufacturing technologies can overwhelm traditional processing systems, resulting in bottlenecks and data latency issues. As a result, critical information may not be processed in a timely manner, leading to missed opportunities for optimization and improvement. In today’s fast-paced manufacturing environment, the limitations of traditional data processing methods are becoming increasingly apparent, highlighting the need for more agile and efficient solutions such as edge computing.
How Edge Computing Revolutionizes Data Processing in Manufacturing
Edge computing is transforming data processing in the manufacturing sector by bringing computational power closer to where data is generated. Unlike traditional methods that rely on centralized servers for processing, edge computing enables data to be analyzed and acted upon in real-time at the edge of the network. This decentralization of data processing reduces latency, improves response times, and enhances overall operational efficiency for manufacturers.
By leveraging edge computing, manufacturers can gain immediate insights from their production processes, enabling them to make informed decisions faster. This real-time data processing capability empowers organizations to monitor equipment performance, detect anomalies, and optimize production workflows seamlessly. Ultimately, the adoption of edge computing in manufacturing is revolutionizing the way data is processed, leading to enhanced productivity, reduced downtime, and improved decision-making throughout the production cycle.
• Edge computing brings computational power closer to where data is generated
• Enables real-time analysis and action at the edge of the network
• Reduces latency, improves response times, and enhances operational efficiency
• Immediate insights from production processes for faster decision-making
• Monitor equipment performance, detect anomalies, and optimize workflows seamlessly
• Revolutionizing data processing in manufacturing for enhanced productivity
Benefits of Implementing Edge Computing in Manufacturing
Edge computing offers numerous advantages when implemented in manufacturing settings. One key benefit is the reduction in latency, as data processing and analysis occur closer to the data source, leading to quicker decision-making. This real-time data processing capability enables manufacturers to respond promptly to issues, optimize processes, and enhance overall operational efficiency.
Moreover, edge computing contributes to cost savings by minimizing the need for large-scale data transmission and storage. By processing data locally at the edge, manufacturing facilities can lower bandwidth costs while efficiently utilizing existing resources. This streamlined approach not only improves performance but also simplifies data management, paving the way for greater scalability and flexibility in operations.
Real-Time Monitoring of Machinery and Equipment
Real-time monitoring of machinery and equipment has become a critical aspect of modern manufacturing processes. By constantly collecting and analyzing data from various sensors and devices installed on machines, manufacturers can gain valuable insights into the performance and health of their equipment. This enables proactive maintenance strategies to be implemented, preventing costly downtime and ensuring optimal operational efficiency.
Moreover, real-time monitoring allows manufacturers to identify potential issues or anomalies as they occur, facilitating quick decision-making and reducing the risk of production disruptions. By continuously monitoring key parameters such as temperature, vibration, and energy consumption, manufacturers can detect abnormalities and take corrective actions in a timely manner. This proactive approach not only helps in maximizing equipment uptime but also enhances overall product quality and customer satisfaction.
Enhancing Predictive Maintenance with Edge Computing
An essential aspect of leveraging edge computing in manufacturing is the enhancement of predictive maintenance practices. By implementing edge computing technologies, manufacturers can collect and process real-time data from machinery and equipment to predict potential issues before they escalate into costly downtime. This proactive approach allows for timely maintenance interventions, thus minimizing disruptions to production schedules and reducing maintenance costs.
Moreover, the integration of edge computing enables manufacturers to move away from traditional scheduled maintenance towards a predictive maintenance strategy. Through the analysis of continuous streams of machine data at the edge, anomalies and patterns indicative of potential failures can be detected early on. This shift not only extends the lifespan of machinery and equipment but also optimizes maintenance schedules, ensuring that resources are allocated efficiently based on actual usage and performance metrics.
Improving Operational Efficiency through Edge Computing
Operational efficiency is a critical aspect of manufacturing processes, as it directly impacts the overall productivity and profitability of a facility. By implementing edge computing solutions, manufacturers can streamline their operations and optimize resource utilization. Real-time data processing at the edge enables quicker decision-making and enhances the responsiveness of machinery and equipment on the shop floor.
Furthermore, edge computing facilitates the automation of routine tasks, reducing manual intervention and human errors. By leveraging edge devices to collect and analyze data closer to the data source, manufacturing facilities can achieve greater process efficiency and minimize downtimes. The seamless integration of edge computing technologies into existing systems paves the way for a more agile and adaptive manufacturing environment.
Ensuring Data Security and Privacy in Edge Computing
Data security and privacy are paramount concerns in the realm of edge computing for manufacturing facilities. As data is processed and analyzed closer to the source at the edge, it is imperative to implement robust security measures to safeguard against potential threats and breaches. By ensuring end-to-end encryption protocols and access controls, manufacturers can mitigate risks and protect sensitive information from unauthorized access.
Moreover, continuous monitoring and regular auditing of systems are essential to identify any vulnerabilities and proactively address potential security gaps. By maintaining a vigilant stance towards data security, manufacturing facilities can uphold the integrity of their operations and instill confidence in employees, customers, and stakeholders regarding the protection of sensitive data in the era of edge computing.
Integration of Edge Computing with IoT Devices in Manufacturing
Linking edge computing with IoT devices in manufacturing is a game-changer, allowing for enhanced data processing and analysis at the network’s edge. By leveraging the computing power of IoT devices situated closer to the data source, companies can reduce latency, improve response times, and make quicker decisions based on real-time insights. This integration facilitates faster communication between devices, enabling seamless data exchange and enabling more efficient monitoring and control of manufacturing processes.
Furthermore, the amalgamation of edge computing with IoT devices opens up avenues for predictive maintenance and proactive interventions in production facilities. With real-time data streaming from various connected sensors and machines, manufacturers can identify potential issues before they escalate, preventing costly downtime and optimizing operational efficiency. This proactive approach ensures that equipment health is monitored continuously, allowing for timely maintenance and minimizing unplanned disruptions in the manufacturing workflow.
Case Studies Demonstrating Successful Implementation of Edge Computing in Manufacturing
In a notable case study within the manufacturing sector, Company X implemented edge computing to enhance its production efficiency and minimize downtime. By deploying edge devices at various points in their manufacturing process, Company X was able to collect and analyze real-time data from machinery and equipment. This allowed them to proactively identify potential issues and take corrective actions promptly, thereby significantly reducing operational disruptions and improving overall productivity.
Another compelling example comes from Company Y, which integrated edge computing with IoT devices in their manufacturing facilities. This integration enabled Company Y to not only monitor their production processes in real-time but also optimize them for maximum efficiency. By leveraging the power of edge computing, Company Y could automate data processing at the edge, leading to faster decision-making and more agile operations. This successful implementation underscored the transformative impact that edge computing can have on manufacturing operations, paving the way for improved performance and competitiveness in the industry.
Future Trends and Developments in Edge Computing for Manufacturing
The future of edge computing in manufacturing is poised for significant growth and innovation. As technology continues to evolve, we can expect to see advancements in edge computing solutions that offer even greater processing power and efficiency. This will enable manufacturers to access real-time insights and analytics faster than ever before, leading to enhanced decision-making processes and operational efficiencies.
Furthermore, with the increasing integration of artificial intelligence and machine learning algorithms into edge computing systems, manufacturers can look forward to more intelligent and autonomous processes. These developments will not only streamline operations but also enable predictive maintenance capabilities that can prevent costly downtime and maintenance issues. In the coming years, edge computing is set to become an indispensable tool for manufacturers looking to stay competitive in an increasingly fast-paced and data-driven industry.
Considerations for Implementing Edge Computing in Manufacturing Facilities
When considering the implementation of edge computing in manufacturing facilities, it is crucial to evaluate the connectivity infrastructure available within the facility. Robust and reliable network connectivity is essential for the seamless transfer of data between edge devices and centralized systems. Conducting a thorough assessment of the existing network capabilities can help in identifying potential bottlenecks and optimizing network configurations to support the deployment of edge computing solutions effectively.
Another important consideration for implementing edge computing in manufacturing facilities is the selection of suitable edge devices. These devices play a pivotal role in processing and analyzing data at the edge of the network. Factors such as processing power, memory capacity, durability, and compatibility with existing systems need careful evaluation to ensure that the chosen edge devices align with the specific requirements of the manufacturing environment. Moreover, considering the scalability and future expansion of the edge computing infrastructure is essential to accommodate the evolving needs of the facility in the long run.
Conclusion: The Future of Manufacturing Lies in Real-Time Insights Powered by Edge Computing
In conclusion, the future of manufacturing is increasingly reliant on real-time insights provided by edge computing. This technology enables manufacturers to process data closer to the source, resulting in faster decision-making and improved operational efficiency. By leveraging edge computing, companies can gain a competitive edge by streamlining processes, enhancing predictive maintenance efforts, and ensuring data security and privacy.
Moreover, the integration of edge computing with IoT devices in manufacturing facilities holds immense potential for generating valuable insights and optimizing production processes. As industry 4.0 continues to evolve, embracing real-time data processing with edge computing will be essential for companies striving to stay ahead in a rapidly changing and increasingly connected manufacturing landscape.
Additional Resources:
[catlist categorypage=”yes”]
Table of Contents
Categories:
[categories orderby=name]
Latest Posts:
[sbs_latest_posts]
FAQs:
What are the benefits of implementing edge computing in manufacturing?
Implementing edge computing in manufacturing allows for real-time monitoring of machinery, enhances predictive maintenance, improves operational efficiency, ensures data security and privacy, and enables integration with IoT devices.
How does edge computing revolutionize data processing in manufacturing?
Edge computing brings data processing closer to the source of data generation, reducing latency and enabling real-time insights for better decision-making in manufacturing processes.
What are some challenges faced by traditional data processing methods in manufacturing?
Traditional data processing methods in manufacturing are often slow, inefficient, and struggle to handle the large volumes of data generated by machinery and equipment in real-time.
How can edge computing enhance predictive maintenance in manufacturing?
Edge computing can analyze real-time data from machinery and equipment to detect potential issues before they occur, enabling proactive maintenance and reducing downtime in manufacturing facilities.
What are some future trends and developments in edge computing for manufacturing?
Future trends in edge computing for manufacturing include the adoption of 5G technology, increased use of artificial intelligence and machine learning algorithms, and the development of more advanced edge computing platforms tailored for manufacturing needs.