Overview of Smart Factories
Smart factories, also known as smart manufacturing or intelligent manufacturing, are an integral part of the Industry 4.0 revolution. These advanced manufacturing facilities leverage cutting-edge technologies like the Internet of Things (IoT), big data analytics, robotics, and artificial intelligence to automate processes and improve operational efficiency. By seamlessly integrating physical production processes with digital technology, smart factories enable real-time data monitoring, predictive maintenance, and adaptive manufacturing capabilities.
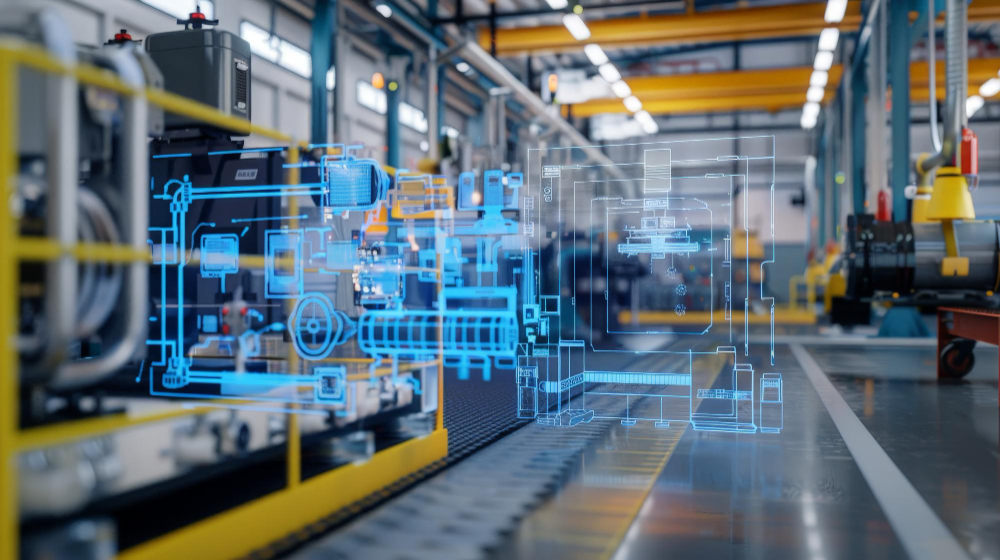
The key objective of smart factories is to enhance productivity, flexibility, and quality while reducing operational costs and time-to-market. By harnessing the power of interconnected systems and intelligent algorithms, these facilities can optimize production flows, minimize waste, and respond swiftly to changing market demands. Ultimately, smart factories represent the future of manufacturing, revolutionizing traditional production methods and paving the way for a new era of industrial innovation.
The Role of Artificial Intelligence in Smart Factories
Artificial intelligence plays a pivotal role in modern smart factories by revolutionizing traditional manufacturing processes. Through advanced algorithms and machine learning capabilities, AI enables machines to autonomously analyze data, make informed decisions, and optimize production efficiency. This transformative technology enhances overall operational performance while mitigating errors and reducing downtime, ultimately leading to increased productivity.
One key aspect of AI in smart factories is its ability to facilitate predictive maintenance. By continuously monitoring equipment performance and identifying potential issues before they occur, AI helps prevent costly breakdowns and ensures continuous operations. This proactive approach not only minimizes unplanned downtime but also extends the lifespan of machinery, resulting in significant cost savings for manufacturing businesses.
Challenges in Defect Detection in Smart Factories
Despite the advancements in AI and automation technologies, challenges still exist in defect detection within smart factories. One of the primary challenges is the complexity of identifying defects across various product types and production processes. Traditional defect detection methods may not always be suitable for the dynamic and fast-paced environment of smart factories, leading to gaps in detecting subtle defects.
Additionally, integrating AI-based defect detection systems with existing manufacturing processes can be a daunting task for many organizations. Ensuring seamless communication and data exchange between different systems and machines is crucial for the successful implementation of AI in defect detection. Resistance to change from workers who may be accustomed to traditional methods can also hinder the adoption of AI technology for defect detection in smart factories.
Benefits of Implementing AI for Defect Detection
Implementing AI for defect detection in smart factories offers numerous benefits to manufacturers. One key advantage is the ability to detect defects with a higher level of accuracy and consistency compared to traditional human inspection methods. AI systems can analyze vast amounts of data in real-time, detecting even the smallest imperfections that might be missed by the naked eye.
Furthermore, AI-enhanced defect detection systems can significantly improve production efficiency by reducing the occurrence of defective products. By identifying and addressing defects early in the manufacturing process, manufacturers can minimize waste, rework, and production delays. This proactive approach not only saves time and resources but also enhances overall product quality and customer satisfaction.
Types of Defects Detected by AI in Smart Factories
One of the key types of defects detected by artificial intelligence (AI) in smart factories is surface defects. AI algorithms are trained to identify imperfections such as scratches, dents, and discolorations on products or components with a high level of accuracy. By analyzing images or 3D scans, AI can swiftly pinpoint surface defects that may not be easily detectable by human inspectors.
Another common type of defect detected by AI in smart factories is dimensional inaccuracies. AI-powered systems can analyze measurements and compare them against specified tolerances to catch deviations that indicate potential quality issues. Whether it’s a misalignment, a deviation in length or width, or any other dimensional variation beyond the acceptable range, AI can quickly flag these discrepancies for further review and correction.
How AI Improves Efficiency in Defect Detection
Artificial Intelligence is revolutionizing defect detection in smart factories by streamlining processes and enhancing efficiency. AI algorithms can analyze vast amounts of data in real-time, enabling quick identification of defects that human eyes might miss. This rapid detection saves valuable time and resources, allowing manufacturers to address issues promptly and prevent defective products from reaching the market.
Moreover, AI systems can continuously learn and improve over time, adapting to new types of defects and evolving production environments. By leveraging machine learning and deep learning techniques, AI can fine-tune defect detection models, leading to higher accuracy rates and fewer false alarms. This adaptive capability ensures that defect detection in smart factories remains effective and efficient, even as manufacturing processes evolve.
Integration of AI with Quality Assurance Processes
One of the key aspects of integrating artificial intelligence (AI) with quality assurance processes in smart factories is the ability of AI systems to continuously analyze massive amounts of data in real-time. By leveraging machine learning algorithms, AI can quickly identify patterns and anomalies that may go unnoticed by human operators, leading to improved defect detection and quality control.
Furthermore, AI enhances the efficiency of quality assurance by automating repetitive tasks such as data collection, analysis, and reporting. This not only speeds up the inspection process but also reduces the chances of errors caused by human fatigue or oversight. By integrating AI into quality assurance processes, smart factories can achieve higher levels of accuracy and consistency in detecting defects, ultimately leading to improved product quality and customer satisfaction.
Key Technologies Used for Defect Detection in Smart Factories
One key technology used for defect detection in smart factories is computer vision. This technology utilizes cameras and image processing algorithms to visually inspect products for defects such as scratches, dents, or misalignments. By analyzing high-resolution images in real-time, computer vision systems can quickly and accurately identify imperfections that may be missed by the human eye.
Another vital technology for defect detection in smart factories is machine learning. This technology involves training algorithms to recognize patterns in data, enabling them to predict and classify defects based on historical information. By continuously learning from new data, machine learning models can adapt and improve their defect detection capabilities over time, helping manufacturers achieve higher levels of product quality and consistency.
Case Studies of Successful Implementation of AI in Defect Detection
Two prominent case studies exemplify the successful implementation of AI in defect detection within smart factories. In the first case, a leading automotive manufacturer integrated AI algorithms into their production line to identify and address defects in real-time. The system analyzed images of car parts using machine learning techniques to flag any imperfections, resulting in a significant reduction in faulty products reaching the market.
In another case, a pharmaceutical company utilized AI-driven defect detection to enhance the quality assurance of their drug manufacturing processes. By deploying cutting-edge AI models, the company was able to pinpoint minute deviations in drug composition that could potentially affect product efficacy and patient safety. This proactive approach not only ensured compliance with stringent regulatory standards but also optimized production efficiency and minimized the risk of product recalls.
Future Trends in AI for Quality Assurance in Smart Factories
As technology continues to advance, the future of AI in quality assurance for smart factories looks promising. One of the key trends that is expected to shape the industry is the increased integration of AI-powered predictive analytics for proactive defect detection. By analyzing vast amounts of data in real-time, AI systems can anticipate potential issues before they even occur, enabling manufacturers to take preventive measures and maintain high product quality standards.
Another emerging trend is the deployment of AI-driven autonomous robots equipped with advanced vision systems for defect detection tasks. These robots can navigate through the production line, inspect products with precision, and identify defects with a high degree of accuracy. This not only enhances the efficiency of defect detection processes but also reduces the reliance on manual labor, leading to cost savings and improved overall productivity in smart factories.
Considerations for Implementing AI in Defect Detection
When considering the implementation of AI in defect detection within smart factories, it is crucial to assess the readiness of the existing infrastructure and systems to accommodate such advanced technology. This involves evaluating the compatibility of AI solutions with the current manufacturing processes, equipment, and data collection methods. Integration of AI should be seamless and not disrupt the overall production flow.
Another key consideration is the availability and quality of data required for training AI algorithms. High-quality data is essential for accurate defect detection, and organizations need to ensure that they have access to comprehensive datasets that represent various types of defects. Additionally, data security and privacy measures must be in place to protect sensitive information utilized by AI systems for defect detection purposes.
• Assess the compatibility of AI solutions with existing manufacturing processes, equipment, and data collection methods
• Ensure seamless integration of AI to avoid disruptions in production flow
• Evaluate the availability and quality of data required for training AI algorithms
• Access comprehensive datasets representing various types of defects for accurate detection
• Implement data security and privacy measures to protect sensitive information used by AI systems
Training and Development for AI-Based Defect Detection Systems
Training and development play a crucial role in ensuring the successful implementation of AI-based defect detection systems in smart factories. Providing comprehensive training programs for employees involved in utilizing these systems is essential to enhance their understanding of AI technology and its application in defect detection. Continuous learning and skill development are necessary to keep pace with the evolving nature of AI algorithms and technologies.
Moreover, the development of specialized courses and workshops focused on AI-based defect detection can help employees hone their skills and expertise in utilizing these systems effectively. By investing in training and development programs, organizations can empower their workforce to leverage AI technology to its full potential for enhancing quality assurance processes in smart factories. This not only boosts operational efficiency but also ensures that employees are equipped with the necessary knowledge to adapt to the changing technological landscape.
Best Practices for Leveraging AI in Quality Assurance Processes
When leveraging AI in quality assurance processes, it is essential to ensure that the data used for training the AI models is of high quality. Garbage in, garbage out – this adage holds true in the context of AI, emphasizing the importance of clean, reliable data for optimal performance. Therefore, organizations must focus on data quality management to drive accurate insights and decision-making within their quality assurance frameworks.
Another best practice for leveraging AI in quality assurance processes is to continuously monitor and evaluate the performance of the AI models. Regular performance assessments can help identify any deviations or anomalies in the AI system’s outputs, allowing for timely adjustments and improvements. By establishing a robust monitoring mechanism, organizations can enhance the effectiveness and efficiency of their quality assurance processes, ensuring consistent and reliable results.
Additional Resources:
[catlist categorypage=”yes”]
Table of Contents
Categories:
[categories orderby=name]
Latest Posts:
[sbs_latest_posts]
FAQs:
What are smart factories?
Smart factories are manufacturing facilities that utilize automation, data exchange, and artificial intelligence to improve efficiency and productivity.
How does artificial intelligence play a role in smart factories?
Artificial intelligence in smart factories is used for defect detection, predictive maintenance, process optimization, and other quality assurance processes.
What are some challenges in defect detection in smart factories?
Challenges in defect detection include complex production processes, varying product specifications, and the need for real-time monitoring.
What are the benefits of implementing AI for defect detection in smart factories?
Implementing AI for defect detection can lead to improved accuracy, faster detection rates, reduced downtime, and overall cost savings.
What types of defects can AI detect in smart factories?
AI can detect various types of defects such as surface defects, dimensional defects, assembly errors, and more.
How does AI improve efficiency in defect detection?
AI improves efficiency by analyzing data at a faster rate, identifying patterns, and making real-time adjustments to production processes.
What key technologies are used for defect detection in smart factories?
Key technologies used for defect detection include machine learning, computer vision, sensors, and IoT devices.
Can you provide examples of successful implementation of AI in defect detection?
Case studies of successful implementation of AI in defect detection include companies in the automotive, electronics, and pharmaceutical industries.
What are some future trends in AI for quality assurance in smart factories?
Future trends include the use of advanced analytics, robotics, and collaborative robots for improved defect detection and quality control.
What considerations should be made when implementing AI in defect detection?
Considerations include data privacy, security, scalability, integration with existing systems, and training for personnel.
How can companies ensure proper training and development for AI-based defect detection systems?
Companies can ensure proper training by investing in employee education, partnering with AI experts, and implementing continuous learning programs.